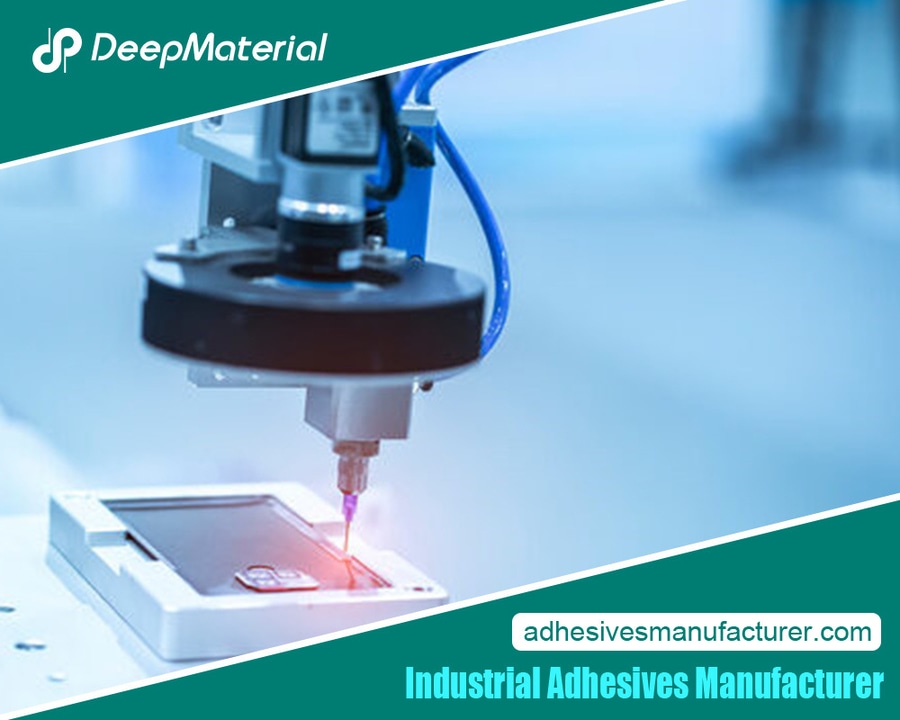
#Industry News
Illuminating Bonding Solutions: A Deep Dive into UV Light Curing Adhesives
Best UV Light Curing Adhesive Glue Manufacturer
UV light curing adhesives have gained immense significance in modern manufacturing and assembly processes. These adhesives offer a rapid and highly reliable bonding solution that has revolutionized various industries.
Their importance lies in their ability to enable fast, precise, and durable bonds in applications ranging from electronics to healthcare. UV light curing adhesives enhance efficiency, product quality, and performance.
UV light curing adhesive technology is based on the principle of photopolymerization, where exposure to UV light initiates a chemical reaction that transforms liquid adhesives into solid bonds within seconds.
The post highlights the fundamental mechanism of UV curing and the advantages it brings, including speed, precision, and adaptability. It sets the stage for a deeper exploration of this transformative adhesive technology.
Applications Across Industries
UV light curing adhesives find versatile applications across a spectrum of industries, enhancing manufacturing processes and product performance:
Electronics and Electronics Manufacturing – UV light curing adhesives play a pivotal role in electronics assembly, bonding components like semiconductors, displays, and PCBs. They enable miniaturization, improve thermal management, and enhance device durability, contributing to the efficiency and reliability of electronic products.
Automotive and Aerospace – In the automotive industry, UV adhesives are used for structural bonding, sealing, and encapsulation. They aid in vehicle assembly and contribute to weight reduction. Aerospace applications include bonding of composite materials, cockpit assembly, and aircraft interior fabrication, where precision and reliability are critical.
Medical Devices and Healthcare – UV light curing adhesives are biocompatible and suitable for medical device manufacturing, including bonding sensors, optics, and disposable medical components. Their rapid curing minimizes production time, crucial for meeting healthcare demands, and ensures patient safety.
Construction and Architectural Applications – In construction, UV adhesives are employed for bonding glass in façades, railings, and interior design elements. Their clarity and durability enhance architectural aesthetics. They are also used for laminating glass, ensuring structural integrity in large architectural projects.
These different applications demonstrate the adaptability and advantages of UV light curing adhesives, underlining their role in improving product quality and facilitating innovation across multiple industries.
Factors Influencing UV Light Curing Adhesive Selection
Selecting the right UV light curing adhesive depends on several crucial factors, each influencing the choice:
Substrate and Surface Considerations – The type and characteristics of the substrates being bonded significantly influence adhesive selection. Considerations include the material composition, surface roughness, and whether the substrates are porous or non-porous. Adhesive compatibility with substrates ensures proper adhesion and durability of the bond.
Environmental Factors and Bonding Conditions – Environmental conditions, such as temperature, humidity, and exposure to chemicals or UV radiation, must align with the adhesive’s capabilities. Some adhesives are engineered for specific environmental challenges. Bonding conditions, including indoor vs. outdoor applications, also influence adhesive choice. Adhesives with appropriate resistance to environmental factors ensure long-term performance.
Strength and Performance Requirements – The intended application’s mechanical demands dictate adhesive strength requirements. High-stress applications, such as load-bearing structures, may necessitate adhesives with enhanced tensile and shear strengths. Temperature resistance, impact resistance, and flexibility are additional performance considerations aligned with the specific application.
Curing Equipment and Process Considerations – The type of UV curing equipment, such as UV LED lamps or mercury vapor lamps, influences adhesive selection. Adhesives should match the curing equipment’s wavelength and intensity specifications. Process considerations include curing time, cure depth, and the geometry of the bonded components. Some adhesives may require longer or shorter exposure times to cure fully.
Comprehensively evaluating these factors is critical to selecting the most suitable UV light curing adhesive for a given application. Failure to consider these elements may result in suboptimal bonding performance and product reliability.
Best Practices for Successful UV Light Curing Adhesive Application
Achieving optimal results with UV light curing adhesives requires adherence to best practices throughout the bonding process:
Surface Preparation and Cleanliness – Ensure that substrates are clean, dry, and free from contaminants, such as grease, dust, or oils. Thoroughly clean surfaces using appropriate methods and solvents. Consider additional surface treatments, such as UV ozone cleaning or plasma treatment, to improve surface adhesion.
Proper Dispensing and Curing Techniques – Use precise dispensing equipment to apply the adhesive evenly and consistently. Ensure that adhesive coverage is uniform without gaps or excess material. Select the appropriate curing equipment and parameters, including UV light source intensity and exposure time. Monitor the curing process to ensure complete and uniform curing.
Quality Control and Testing Procedures – Implement quality control measures at various stages of the bonding process. Conduct visual inspections to identify defects, incomplete curing, or uneven adhesive distribution. Perform adhesion testing and mechanical tests, such as tensile or shear strength assessments, to verify bond quality and performance. Keep detailed records of the curing process parameters and testing results for quality assurance and process optimization.
Following these best practices ensures consistent and reliable results when using UV light curing adhesives. Proper surface preparation, precise application, and thorough quality control are essential for achieving strong and durable bonds in various application.
Common Challenges & Solutions
Adhesion challenges and substrate compatibility are critical factors to address when working with UV light curing adhesives:
Substrate Compatibility
Different materials exhibit varying surface properties and compositions, which can affect adhesive bonding. Compatibility between the adhesive and substrates is essential for a strong and durable bond.
Surface energy, roughness, and chemical composition are factors that influence substrate compatibility. Adhesives should be chosen or formulated to adhere well to specific substrates, whether they are metals, plastics, glass, or composites.
Some substrates may require surface treatments, such as cleaning, abrasion, or chemical modification, to enhance adhesion. Proper surface preparation ensures the adhesive can wet and bond effectively to the substrate.
Adhesion Challenges
Bonding dissimilar materials or substrates with varying thermal expansion coefficients can pose challenges. Differential expansion and contraction during temperature fluctuations may lead to stress at the bond line, potentially compromising adhesion.
In applications where substrates have low surface energy, achieving strong adhesion can be challenging. Specialized adhesives or surface treatments, like plasma or flame treatment, are often necessary to improve bonding to low-energy substrates.
Adhesion challenges may also arise when bonding to surfaces contaminated with oils, greases, or release agents. Proper cleaning and surface preparation are essential to overcome such challenges.
Compatibility Testing
Prior to production, compatibility testing should be conducted to ensure that the chosen adhesive bonds effectively with the specific substrates in the intended application.
Testing may include measuring bond strength, conducting adhesion tests, and assessing the adhesive’s resistance to environmental conditions relevant to the application.
Custom Formulations
In cases where standard adhesives may not provide the required substrate compatibility, custom formulations may be developed in collaboration with adhesive manufacturers. Custom formulations can address unique challenges and improve bonding performance.
For more about a Deep Dive into UV Light Curing Adhesives, you can pay a visit to Deepmaterial at https://www.adhesivesmanufacturer.com/ for more info.