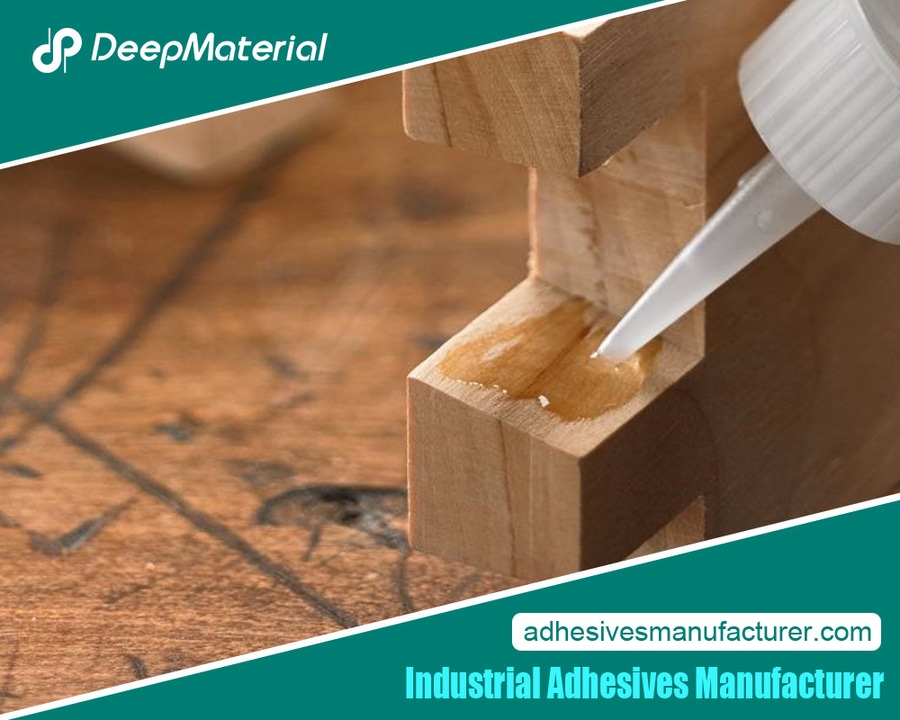
#Industry News
Fast and Reliable: UV Curing Adhesive Glue for Plastic Bonding
Best UV Curing Adhesive Glue Manufacturer
UV curing adhesive for plastic has now become a big deal in the bonding industry. These adhesives have become top choice in industries where plastics are manufactured. UV curing adhesives have certainly revolutionized the plastics industry.
In this post, we look at what has changed since the emergence of UV curing adhesive glue for plastic bonding. You can base your decision on the information you will gather from this post. We will get things started with a quick overview of the UV curing adhesive glue technology.
A Quick Overview of UV Curing Adhesive Glue for Plastic Bonding
Fundamental Principles – UV curing adhesive technology relies on a photopolymerization process, where the adhesive undergoes a chemical transformation when exposed to ultraviolet (UV) light. This transformation changes the adhesive from a liquid or gel state to a solid state, forming a strong bond.
Mechanism – The UV curing process involves the use of photo initiators, which are compounds in the adhesive that become highly reactive when exposed to UV light. When these photo initiators absorb UV radiation, they initiate a chain reaction that leads to the crosslinking of the adhesive molecules. As a result, the adhesive solidifies and bonds the plastic substrates together.
Advantages – UV curing adhesive technology offers several key advantages for plastic bonding. It is exceptionally fast, with curing times measured in seconds, making it suitable for high-speed production processes. Additionally, it provides precise control over the curing process, ensuring that the adhesive only cures when exposed to UV light. This precision minimizes the risk of adhesive migration or contamination. UV curing also offers superior bond strength and durability.
Applications – UV curing adhesive technology is widely employed in industries where plastic bonding is a common practice. This includes applications in plastic assembly, electronics manufacturing, medical device production, and automotive manufacturing, among others.
Understanding this technology’s fundamental principles and its advantages in plastic bonding is crucial for professionals seeking to harness its capabilities effectively in their specific applications. In the subsequent sections of this post, we will elaborate above points if need be.
Applications of UV Curing Adhesive Glue in the Plastic Industry
UV curing adhesive technology finds diverse applications within the plastic industry.
Plastic Assembly and Fabrication
UV curing adhesives are extensively used in bonding plastic components, whether for structural or decorative purposes. They offer rapid bonding without the need for heat or solvents, preserving the integrity of plastic parts. Applications include the assembly of plastic enclosures, housings, consumer goods, and display screens.
Electronics and Plastic Components
The electronics industry benefits from UV curing adhesives for attaching plastic components in electronic devices. These adhesives ensure precise and secure bonding while maintaining the integrity of sensitive electronic parts. Common applications include bonding plastic connectors, displays, and printed circuit boards.
Medical Devices and Plastic Materials
UV curing adhesives are crucial in the medical field, where biocompatible and fast-curing adhesives are essential for bonding plastic materials in medical devices. Applications encompass the assembly of diagnostic equipment, catheters, surgical instruments, and wearable medical devices.
Automotive and Plastic Parts Bonding
In the automotive industry, UV curing adhesives are employed for bonding plastic components, contributing to lightweight vehicle design and improved fuel efficiency. Applications extend to bonding plastic interior components, exterior trims, headlamp assemblies, and automotive electronics.
These diverse applications illustrate the adaptability and advantages of UV curing adhesive technology in addressing the bonding needs of plastic materials across various sectors of the industry.
Factors Influencing the Choice of UV Curing Adhesive
Selecting the appropriate UV curing adhesive for a particular plastic application depends on several key factors:
Plastic Substrate Considerations – The nature of the plastic substrates being bonded plays a key role. Consider factors such as the type of plastic, surface energy, roughness, and whether the plastic is treated or untreated. Ensuring compatibility between the adhesive and the specific plastic substrates is crucial for achieving strong and durable bonds.
Environmental Conditions and Bonding Settings – The environmental conditions under which bonding occurs must align with the adhesive’s properties. Assess factors like temperature, humidity, exposure to chemicals, and UV radiation. Consider whether the application is indoors, outdoors, or in a controlled environment. Adhesive selection should accommodate these conditions.
Strength and Performance Requirements – The mechanical demands of the application determine the adhesive’s strength requirements. High-stress situations may necessitate adhesives with enhanced tensile, shear, or impact strength. Performance requirements, such as temperature resistance, flexibility, and resistance to environmental factors, should also be considered.
UV Curing Equipment and Process Consideration – Ensure that the UV curing adhesive aligns with the UV curing equipment being used. Factors to consider include the type of UV light source, intensity, and wavelength. Process considerations encompass curing time, cure depth, and the geometry of the bonded components. Some adhesives may require longer or shorter exposure times to cure fully, depending on the equipment and process parameter.
Considering these factors during adhesive selection customizes the UV curing adhesive to suit the precise requirements and conditions of the plastic bonding application, ultimately enhancing the likelihood of successful bonds and product dependability.
Sustainability Initiatives and Eco-friendly Solutions
When discussing UV curing adhesives, sustainability initiatives entail the actions taken by adhesive manufacturers and industries to diminish the ecological footprint associated with adhesive products and their production processes.
Reducing Harmful Chemicals – Manufacturers strive to develop adhesive formulations that contain fewer or no harmful chemicals. This includes minimizing volatile organic compounds and hazardous air pollutants (HAPs), which can be detrimental to both human health and the environment.
Energy Efficiency – Sustainable adhesive formulations are designed to cure more efficiently, requiring less energy during the UV curing process. This reduces the carbon footprint associated with adhesive production and use.
Biodegradability – Some eco-friendly formulations are engineered to be biodegradable, ensuring that adhesive residues break down naturally in the environment, reducing long-term pollution.
Recyclability – Efforts are made to develop adhesives that are compatible with recycling processes. This promotes the circular economy by allowing for the reclamation and reuse of materials.
Reduced Waste – Eco-friendly formulations aim to minimize material waste during adhesive application. This is achieved by optimizing dispensing techniques and reducing excess adhesive use.
For more about a complete guide to UV Curing Adhesive Glue for Plastic Bonding, you can pay a visit to Deepmaterial at https://www.adhesivesmanufacturer.com/ for more info.