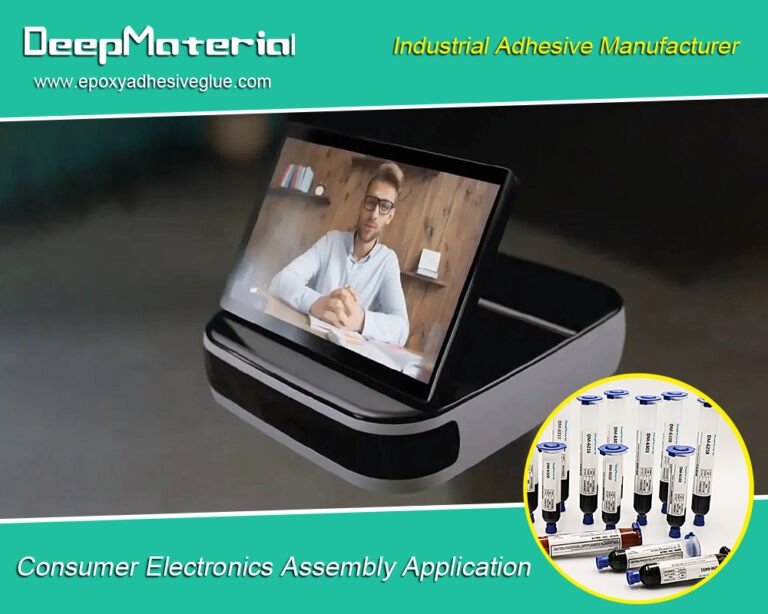
#Industry News
Can non-conductive coating for electronics be used for automotive or aerospace applications?
Best non-conductive coating Adhesive Glue for electronics Manufacturer
No matter the industry, protecting delicate electronics from external wear and tear is absolutely vital. Non-conductive coatings make that protection an absolute must for parts living in harsh environments – like the automotive and aerospace business.
These create a stress shield against moisture, chemicals, temperature extremes, and anything else that may tarnish their workmanship or muck up performance! It’s this added layer of safeguarding that guarantees durability, reliability, and optimal functioning all around.
Benefits of using non-conductive coatings in automotive and aerospace industries
Non-conductive coatings are a blessing in disguise for the automotive and aerospace industries. For starters, they boost the lifespan of electrical units by forming an airtight layer against moisture, chemicals and elements – especially in scenarios with high vibration or temperature changes. This shields connections from short circuits or corrosion, resulting in flawless performances every time!
Furthermore, using these coatings saves money that would otherwise have been spent on maintenance or repairs later down the line – what a brilliant way to keep checks on costs without compromising quality. And as if that wasn’t enough to draw cheers all around, fewer replacements mean added sustainability amidst industrial production processes, too.
Challenges faced by electronics in harsh environments
Electronics used in the automotive and aerospace industries are put through an absolute gauntlet. From extreme cold to searing heat, not only do components expand and contract—often leading to fatigue cracks or stress fractures—but they can come up against moisture control issues such as condensation that can cause corrosion and electrical failure.
Then there’s the chemical risk that must be managed, especially when dealing with fuels, lubricants, or other potentially hazardous substances; you could have subtle degradation of parts before it fully kicks in. Don’t forget about vibration, either!
All those engines going like crazy, and transport movements take their toll on the electronic components if adequate care isn’t taken–and sudden jolts of shock from impacts mean delicate electronics may never find their way back into one piece again.
How non-conductive coatings protect electronics from environmental factors
Non-conductive coatings provide a robust shield around electronic components, defending them from the perils of environmental factors. They work like trusty knights to protect against any moisture or chemicals that might creep in and harm delicate electrical connections.
Not only can this layer of waterproofing halt corrosion or short circuits, but it also acts as an insulator, masterfully regulating jarring temperatures by both reducing heat transfer and adding insulation against the coldest chill.
On top of all that, non-conductive coatings offer shock absorption properties – a cushion for any vibrations or jerks present that may otherwise cause mechanical failure or head off potential disconnection due to rough handling.
Types of non-conductive coatings available for electronics
When it comes to safeguarding electronics from extreme temps, moisture, and impact in automotive or aerospace applications, you’ve got a few choices.
Silicone-based coatings offer flexible protection that can repel chemical damage and withstand temperature shifts as well as rattling motions. Epoxies are great for adhering to things securely – they fare exceptionally well under heat and stress incurred by vibrations – making them popular amongst aeronautical engineering vehicles.
Polyurethane has incredible abrasion resistance, so that’s an obvious go-to when looking for something elastic yet long-lasting. Perfect for dealing with the harsh environment found in any car or plane!
But suppose absolute perfection is what matters most. In that case, then perylene coating is your mate: moisture-proof plus a completely sealed guard against autopsy compounds, temp fluxes & plumbing thrash, making them perfect for the highest levels of electro-defense within aircraft!
Factors to consider when selecting a non-conductive coating for automotive or aerospace applications
When selecting a non-conductive coating for cars or airplanes, there are a few things to take into account. It all boils down to the environment that the electrical parts will be exposed to – temperature swings, moisture levels, chemicals and vibrations or shocks must be considered when choosing the right product so it can endure these situations and protect your electric components.
Moreover, you’ve got to make sure the material is compatible with what already exists in those systems; otherwise, it’s tearing up money: compatibility trials should tell you if this coating will react badly with anything inside.
Plus, there are always application methods to think of; some coatings may need spray coating while others might require dip coating or even vacuum deposition depending on how wide an area needs coverage or how deep they want their protection layer!
Bottom line: cost – both short-term, like initial costs/equipment needed, as well as longer-term maintenance wins, must also be taken into consideration here.
In other words, do your research first before picking one because the balance between cost and performance ensures you get bang for the buck.
Application methods for non-conductive coatings on electronics
Non-conductive coatings can be applied to electronics by a variety of means, from spraying them on with a gun or automated system to going the dip coating route and actor even the more sophisticated vacuum deposition.
Spray painting is a trendy choice because it covers everything in an even layer, no matter how intricate the surface shape may be. With dip coating, you get uniformity and accuracy, but for delicate components or complex structures, it might not do the trick.
When you opt for vacuuming up that layer instead, then you’re sure to get a precise thickness regardless of your equipment’s specs – so long as they meet stated criteria like complexity levels and production volume requirements.
So carefully consider each method before choosing one – depending on what electronics task you have at hand – And select wisely.
Last Words
The arena of non-conductive coatings for electronics, which have to endure the most challenging conditions, has been becoming more and more advanced day by day. Research and development keep revitalizing these protective systems, promising higher performance as well as more extended durability.
To make sure this level of protection is kept at its highest, new technologies as well as materials are being examined constantly– things like nanotech for improved barriers plus better resistance towards moisture, chemicals, or even extreme temperatures! If all goes right with that research, this could mean lengthy defense for electronics utilized in aviation and automobiles.
Furthermore, the efficiency and effectiveness of coating processes are currently seeing significant improvements due to advancements in their applications. For instance, robot sprays are very much in development to ensure that complex forms or surfaces get precisely and uniformly covered each time– leading to shorter timespan on coating procedures while making them cost less money, too!
For more about choosing the best non-conductive coating for electronics, you can pay a visit to DeepMaterial at https://www.epoxyadhesiveglue.com/category/epoxy-adhesives-glue/ for more info.