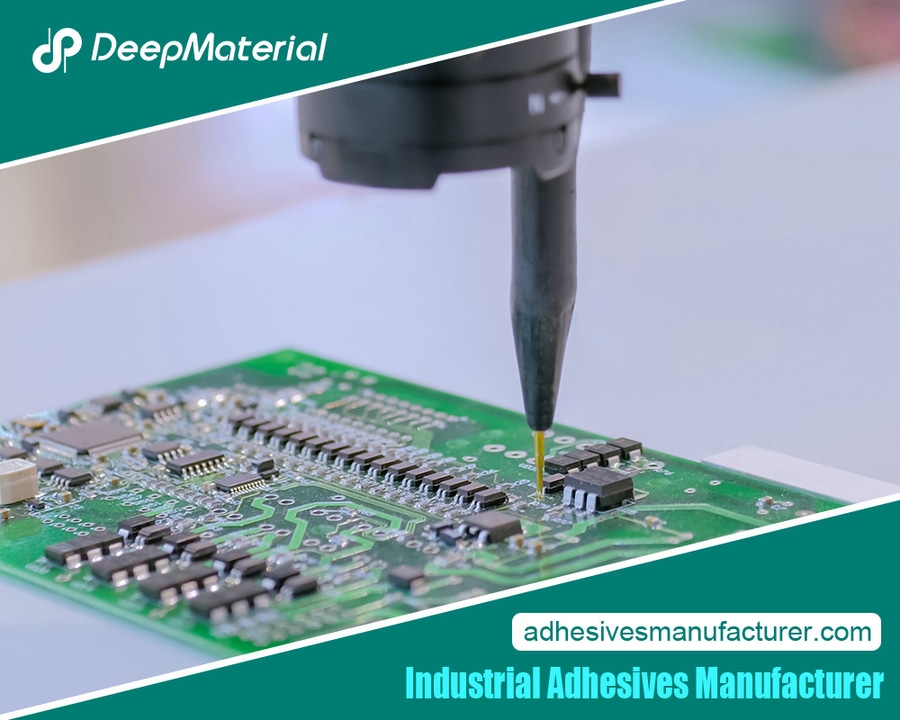
#Industry News
What Is Silicone Conformal Coating For PCB?
Best Silicone Conformal Coating Adhesive Glue For PCB Manufacturer
Silicone conformal coatings are just like any other form of coating when it comes to protecting electronic components and PCBs; only these ones have the extra advantage of being able to stand up against temperatures that more ordinary versions simply wouldn’t be able to cope with.
Usually, you’d need a solvent along with this type of protection, but there’s now been a breakthrough in the development of a new kind of coating that doesn’t require one!
Conformal coatings are becoming increasingly popular, as they act like a thin, protective shield over PCBs and their components, shielding them from physical, mechanical, and chemical damage.
Specifically speaking, the demand for silicone conformal coating is soaring – mainly because it steps up to do the job when other coatings fail. Evolving along with PCB technology itself, this advanced form of protection is without doubt crucial in safeguarding today’s tech!
What is Silicone Conformal Coating for PCB?
Silicone conformal coatings have been rising in popularity since they offer PCBs a more comprehensive range of temperature protection as compared to other coatings. With its resistance to chemicals, moisture, and vibrations – this coating stands out from the rest. The only hiccup? Well, it’s hard to remove or repair, so you must be extra careful when dealing with it.
What is So Unique About These Compounds?
Silicone conformal coatings are a safe bet for any PCB materials, as IPC standards vouch for their reliability. Plus, they’re compatible with thermal paste – an integral part of hot-blooded circuit configurations.
But no silver bullet comes without drawbacks: these coverings attract water like nobody’s business during the application process itself!
This is why it’s especially crucial to apply them evenly; it wouldn’t take many H2O molecules glancing off imperfections in the covering for cascading corrosion to start chipping away at your defense shield before you know what hit you!
Not only that, but this moisture could also carry corrosive elements right in with it, acting as an icing on the slow death cake.
This nature makes silicone conformal coatings hazardous for circuitry as they can disrupt data flow if made of non-conductive material. It won’t be long after applying them and leaving them exposed until their elasticity affects thickness such that two coats may soon appear one – kind of like how thin upper lines emerge over time across glass windows, too!
The Flexibility of Silicone Conformal Coating
Flexible PCBs draw on a lot of the same circuits and components as regular boards – but they can bend and twist into all sorts of shapes that rigid ones simply can’t. So, in order to provide flexible PCBs with reliable protection, you need something that bends too – enter silicone conformal coating!
Anything else won’t fully cover the flex board’s crevices adequately and could even lead to malfunctioning. The key here is to make sure hunky-dory protection comes through correctly so those precious flex boards don’t flop!
The Coating Process Ensures High Returns
Silicone conformal coating can be a cost-effective solution – if it’s applied with precision. But when mistakes occur, reverting makes the supervised hassle seem not worth the risk. Unlike other coatings that are easier to repair, any misstep in silicone’s application can turn into a costly downfall!
If designers have to remove it, they need long and grueling chemical treatments that could cause physical or even chemical damage to existing circuits – delaying production significantly. Even though rewards are tempting, forethought must prevail before applying this tricky process of protection; planning for the potential consequences, if errors arise, is essential for ultimate success.
Industry Use
Silicone conformal coatings are currently on the rise; they have become the King in the Conformant Coating world! Not only are they popular across many industries, but their ability to handle extreme temperatures is likely why Automotive parts use them most. From hot to cold, these tough guys keep up through it all!
The Advancement of Silicone Coating Process
With the incredible advancements of technology often come leaps in coatings. Such is the case with solventless silicone conformal coatings that illustrate a perfect example of innovation. These new-age creations are now widely available on the market and offer ways to protect components from extreme conditions – such as those present in outer space!
In comparison to other types of silicon conformal coatings, this new coating doesn’t require any solvents during application. It does its job exceptionally well to freeze each piece exactly how it should be without constricting flexibility. It’s also able to create an impeccably smooth surface, courtesy of ultra-small particles barely visible under a microscope – just one micrometer wide!
Thanks to its ability for ultrafast curing through UV light or simply air-drying at room temperature (even on rigid PCBs) – maintaining accuracy upon all shapes makes having this type of silicon coating a desirable option indeed, particularly by top players within the aerospace industry.
Thinking of manufacturing reliable and resilient electronic components that can handle high temperatures while still being flexible? Try adding silicone conformal coating to your production process. It’s a surefire way to protect your electronics against extreme conditions for optimal performance. Plus, it’ll make them dead simple to maintain in the long run!
Final Thoughts
Silicone conformal coating for PCBs is essential to extend the life of electronics and make sure they remain reliable. When applied, it provides a thin layer that serves as a barrier against environmental elements – such as moisture, chemicals, and extreme temperature fluctuations. Since its properties include high dielectric strength, flexibility and thermal stability all at once – silicone has become very popular with industries facing challenging conditions.
The return on this form of protection can’t be underestimated, mainly when more electronics are being used in hostile environments; one way or another, an investment in silicone coatings will pay off down the line by ensuring long-term performance under any strain.
For more about a complete guide to the Silicone Conformal Coating For PCB, you can pay a visit to Deepmaterial at https://www.adhesivesmanufacturer.com/ for more info.