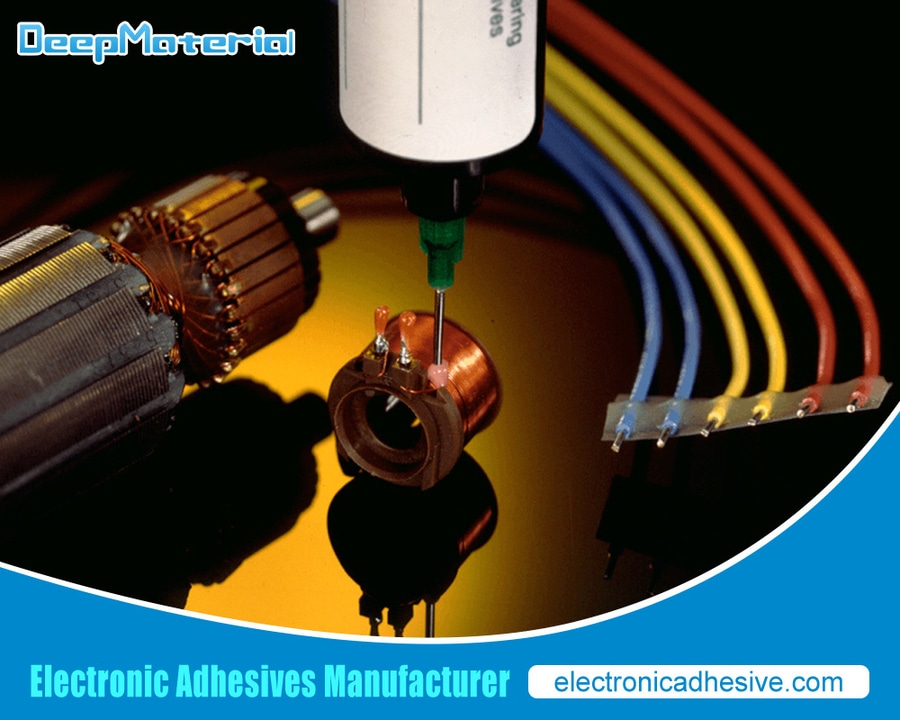
#Industry News
What Are The Functions of A Low Adhesion Protective Coating Manufacturer?
Best Low Adhesion Protective Coating Adhesive Glue Manufacturer
Low-adhesion protective coatings are essential for shielding surfaces and products from weathering, corrosion, destruction, and wear. These specific coatings are used in a variety of industries to promote longevity and performance.
This article looks into the significant role of low adhesion protective coatings as well as how producers in the industry play a part — e.g., planning, designing coatings, testing them to make sure they meet quality standards for particular applications, offering technical assistance & consultation services, managing supply chains & logistical needs, taking environmental protection considerations into account, researching new coating technologies, and forecasting future trends within this space.
Importance of Protective Coatings in Various Industries
Protective coatings are indispensable for various industries, shielding surfaces from hostile environments and shielding against damage. These enigmatic enablers serve to forestall corrosion, abrasion, chemical aggression, and other types of stress; plus, they expand the lifespan of products and frameworks dramatically, so replacements or renovations become far less frequent – taking a tremendous load off businesses in whatever arena they ply their trade.
In automotive, aerospace, marine, oil/gas development, construction activity, and electronics manufacturing, protective coatings have an essential role to play. Just look at motor vehicles: these coats guard vehicle bodies from rusting & corroding while up there looking down on us. All aircraft benefit greatly, too, with paint protection giving respite from searing temps as well as atmospheric conditions that would otherwise take a hefty toll on their surface areas.
The maritime industry offers another example – applying coats to ships & offshore structures, warding off saltwater incursions that’d turn them to ruin without even batting an eyelid.
Role of a Low Adhesion Protective Coating Manufacturer
A low-adhesion protective coating manufacturer is integral to the industry, with its savvy in designing, developing, producing, and supplying top-grade coatings that fulfill customer requirements. Their combination of tech know-how and insights into specific materials and processes makes it easy for them to craft tailored solutions.
Which company you entrust with your project can determine success. Longstanding manufacturers that have served the business’s most prominent names are likely a safe bet – as well, they should be replete with cutting-edge facilities and exemplary staff. This guarantees prime quality products meeting all industry certifications.
Designing and Developing Low Adhesion Coatings
Understanding the exact specifications of a project is essential when it comes to designing and producing low-adhesion coatings. Environmental conditions, surface type, and expected results – all must be taken into account for the ideal outcome. With that knowledge in hand, manufacturers can then choose suitable materials and formulate an appropriate coating that will meet all needs.
Tailoring coatings to different applications takes some real finesse, too; one size does not always fit all! The composition has to be just right – thinner than required won’t do – as well as texture and other fine details adjusted accordingly for optimal performance. Companies ensure this attention to detail by talking closely with their customers so that each recipe is personalized for perfection.
Testing and Quality Control of Coatings
It’s essential to test and have a quality control process in place for low-adhesion coatings. Companies carry out lots of exams, from adhesion tests to corrosion resistance tests, abrasion assessments to chemical inspections – all with the aim of meeting industry standards and achieving desired performance.
The process of quality control is there at every stage. From inspecting raw materials to carrying out checks while products are made to examining the finished item. What’s more, businesses have also devised comprehensive management systems that guarantee steady procedures plus enable them to track their production processes accurately.
Customization of Coatings for Specific Applications
Customization is absolutely crucial for low-adhesion protective coatings since it gives manufacturers the power to tailor them perfectly to meet any application’s specific needs. This can mean tinkering with their composition, thickness, texturing or even other properties.
In the automotive business, scratch resistance, UV protection, and chemical resistance must be a top priority. At the same time, in oil and gas engineering, those coatings must take on high temperatures, corrosive substances, and mechanical stress aplenty. By customizing these coverings so that they tackle every challenge head-on, manufacturers guarantee maximum performance as well as optimal protection.
Technical Support and Consultation for Clients
The acclaimed, low-adhesion coating manufacturer offers its customers technical support and personal consultation services. Their highly trained experts are here to help with product selection, application methods, problem-solving, and enhancing performance – whatever is needed!
Looking out for their clients like a hawk, the team provides advice that helps them make educated decisions while assisting when they hit any bumps in the road along the way. Technical support is invaluable; it’s like having an extra pair of hands on deck at all times.
Supply Chain Management and Logistics
Effective supply chain management and logistics are a must for manufacturers of low-adhesion protective coatings. To guarantee smooth sailing throughout the whole production process, you need to make sure all materials, equipment, and information pistons are turning – from maintaining relationships with suppliers to ensuring timely delivery of finished products. It’s all got to be coordinated appropriately.
Bottom line: if you’re in the business of manufacturing specialized coatings like this, efficient supply chains are crucial. Not only do they help satisfy customers’ requirements, but they also cut down costs and minimize lead times. Plus, they give overall control over one’s marketability by responding quickly when change is required or new orders come in.
Environmental and Safety Considerations in Coating Production
As producers of low-adhesion protective coatings, manufacturers must be mindful not only of environmental stewardship but also of safety awareness. This means being conscious of using sustainable resources with minimal waste production while utilizing proficient energy practices.
Furthermore, the utmost cause should be the promotion of a secure work environment for their workers, which would include having proper training protocols in place before operating any dangerous elements and granting appropriate gear when necessary. Naturally, the best approaches in managing hazardous materials need to adhere to well-established standards or else risk dire consequences down the road.
Research and Development for New Coating Technologies
Research and development efforts are instrumental in the progress of low-adhesion protective coverings. Manufacturers put serious capital into R&D to whip up cutting-edge coating technologies that offer a better track record, longevity, and eco-friendliness. This could mean dabbling with fresh materials, perfecting creative concoctions, and adjusting coating systems.
What’s more, R&D keeps manufacturers one step ahead of their rivals by consistently refining their products plus methods – making it possible for them to alter according to changing market swings and consumer needs. Hence, they keep sitting at the peak of the estimation ladder.
Final thoughts
The future of low-adhesion protective coatings looks bright, with multiple trends set to influence the industry’s direction. Sustainability is a big deal, as companies invest in greener solutions like sustainable materials, water-based formulations and low VOC content.
Innovative coatings are also rising stars; they bring self-healing and self-cleaning properties that need less maintenance and boost performance at the same time. But arguably most excitingly, nanotechnology offers further enhancements – not only improved adhesion, corrosion resistance or wearability but even things like antimicrobial coverage or thermal insulation.
For more about choosing the best low adhesion protective coating manufacturer, you can pay a visit to DeepMaterial at https://www.electronicadhesive.com/ for more info.