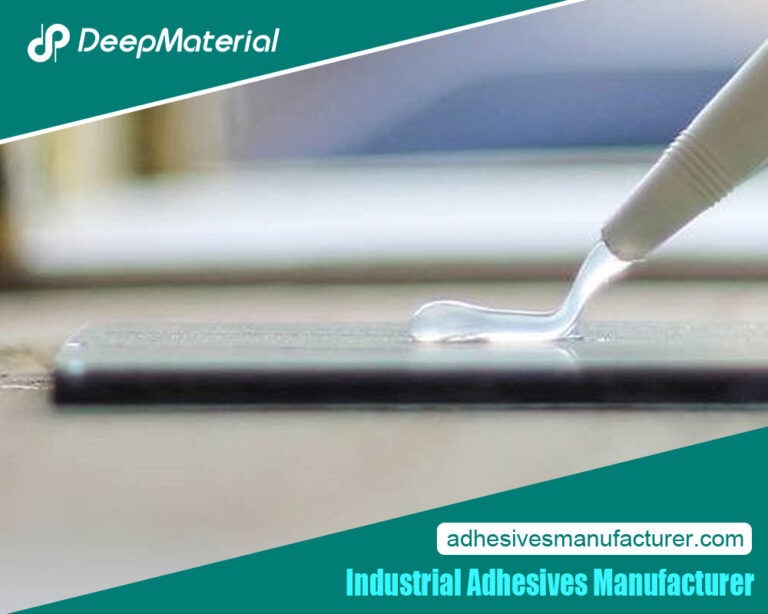
#Industry News
What Is PCB Conformal Coating Services
Best PCB Conformal Coating Adhesive Glue Manufacturer
PCBs are the cornerstone of modern electronic devices, forming the base on which everything else is connected. As technology progresses, these gadgets have become smaller and more intricate – often while being exposed to horrific conditions.
Guaranteeing their performance in challenging situations (and those that may arise) requires PCB conformal coating services, providing a solid defense, shielding them from harmful elements, and helping keep them ticking for longer!
What is PCB Conformal Coating?
Conformal coating is a thin layer of protection that shields your PCB against the elements – dust, moisture, chemicals, and temperature changes. This dielectric material wraps around components and tracks without affecting their performance. It’s vital to keep those delicate circuits guarded from harsh conditions.
Types of Conformal Coating
Several different types of conformal coatings are out there with unique attributes tailor-made for various applications. The most prevalent ones include:
Acrylic Coating– No wonder acrylic coatings are everyone’s go-to – they resist moisture virtually and protect from fungi like a pro! Not only that, but their ease of application and repairability make them the perfect pick for nearly any task.
Silicone Coating– Silicone coatings give superior elasticity and can bear blistering temperatures. Moreover, they have exceptional imperviousness to chemicals and moisture – making them ideal for any environment in which they are utilized. In other words, you can depend on their relentless effectiveness and optimum performance!
Urethane Coating – Urethane coatings are renowned for their strength and imperviousness to wear. They offer a reliable guard against hazardous substances and environmental contaminants. Boasting immense industrial use, these dependable coverings are truly the defenders of our well-being!
Parylene Coatings– Parylene coatings are laid down as a sheer, ethereal, misty fog, an ultra-thin covering like none other, providing the ultimate shielding against humidity levels and hazardous substances found in nature. This remarkable cloak of protection never wavers, not even when exposed to syrupy summer heat or sub-zero frostbite!
The Benefits of PCB Conformal Coating Services
Environmental Protection– Conformal coatings on printed circuit boards act as an impenetrable shield against dust, moisture, and corrosion—ensuring that precious electronic devices can survive whatever rough environments life throws their way. This protection is essential for operations where these components are exposed to the outdoors or other harsh industrial conditions—and ensuring a circuit board is adequately coated up serves as a practical advantage and peace of mind.
Chemical Resistance– Conformal coatings are like a shield for electrical components, offering protection against corrosive chemicals to increase lifespan. Automotive, aerospace, and medical device industries can all benefit from this barrier that guards vulnerable parts against any unwanted exposure to chemical agents.
Improved Reliability– Conformal coatings help reduce environmental effects on electronic devices, which is a must-have for reliable performance, especially in critical use areas like healthcare – a hiccup there could result in dire consequences. In other words, reducing disaster risk means assimilating eco-protective measures into each device’s design.
Temperature Stability– Conformal coatings don’t just look pretty – they provide an essential layer of protection for PCBs against temperature fluctuations. Just think about automotive electronics, where having reliable insulation from heat could mean the difference between proper performance and a breakdown on the side of the highway. So yeah, conformal coatings are vital in those situations – never underestimate their importance!
Methods of Application
Figuring out how to apply conformal coatings comes down to several factors, like what the coating is made of and how complicated the PCB assembly is. High-volume production also counts when picking an application method. Some of the most common ones are:
Dip Coating– The PCBs are submerged deep into a vat full of liquid conformal coating. Any excess is then drained off, sealing the deal and forming an impenetrable layer for protection. ‘Voila’ – after curing, the transistors and circuit boards emerge from their bath with a glorious brand-new safety net around them!
Spray Coating– Spraying a precise stream of conformal coating onto Printed Circuit Boards (PCBs) is the method of choice for mass-producing complex geometries. This approach ensures manufacturers can quickly and efficiently produce large-scale orders – without all the fuss!
Brush Coating– Brushing convolutes conformal coating onto precise areas of the Printed Circuit Board – an excellent solution for those short, low-volume production runs. Not to mention, it’s easily done by hand, so you don’t need any fancy equipment; just a brush will do!
Selective Coating– Automated machines only protect certain areas, mysteriously leaving others behind. This mode of application is perfect for scenarios where particular components need that extra bit of TLC. It’s like a guardian who sentinels over the vulnerable parts!
Special Considerations and Challenges
PCB conformal coating services certainly bring their advantages – no question about that! However, manufacturers must keep in mind the challenges and considerations that come with it. Acknowledging this stuff upfront can be a real lifesaver down the road!
Compatibility– When protecting a printed circuit board, selecting the right type of conformal coating is critical. It should suit the application and materials featured in that PCB assembly. Make sure these components are properly shielded from dirt, dust, and other outside elements -now that’s what you call intelligent design!
Thickness Control– It’s essential to guarantee a consistent level of coating thickness for the best protection without affecting the PCB’s ability to perform. Don’t let your guard down; subpar coverage could spell disaster!
Curing Process– Making sure you get it right is the key to unlocking the full potential of your conformal coating – and make sure to take advantage of those curing processes. Folks better abide by them if they want to reap all their rewards!
Reworkable– It can be tough to strip away certain coatings, so you’d better think about the potential of repairing or changing things up.
Final Thoughts
PCB conformal coating services enormously guarantee the dependability and durability of electronics across numerous industries. As electronic components march forward into tomorrow, ensuring protection from exterior forces grows more urgent. Companies must thoroughly select and apply coatings with their specific applications in mind. With decent coverage, gadgets can battle harsh conditions like a champ, delivering consistency and robustness for many miles.
For more about a complete guide to the PCB conformal coating services, you can pay a visit to Deepmaterial at https://www.adhesivesmanufacturer.com/ for more info.