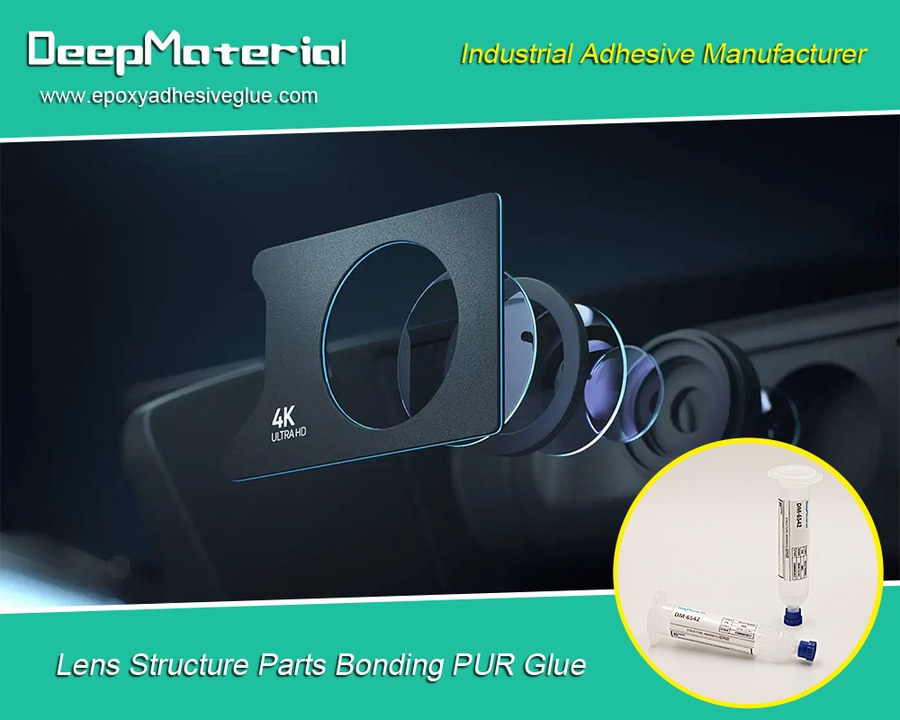
#Industry News
Addressing the Myths and Misconceptions About UV Curable Conformal Coatings
Best UV Curable Conformal Coatings Adhesive Glue Manufacturer
UV curable conformal coatings are special protective layers put on electronic parts to shield them from things like moisture, dust, and chemicals. They’re set hard using UV light, making the process quick and effective. This kind of protection is crucial in the electronics world to make sure devices work well and last a long time.
These coatings are super important because they stop bad things like moisture and dust from damaging the electronics. Without this protection, devices could easily get corroded, short out, or stop working altogether. UV curable conformal coatings are great because they dry fast, stick well, and can cover complex shapes and surfaces really well.
Common Myths and Misconceptions About UV Curable Conformal Coatings
Even though UV curable conformal coatings offer a lot of benefits, there are some myths out there that could lead folks in the industry astray. It’s key to clear up these myths so people use the coatings correctly and don’t miss out on what they offer.
Myth 1
One myth is that these coatings aren’t tough. Some people think they can’t stand up to harsh conditions as well as other coatings. But that’s not true—there are plenty of durable UV curable coatings out there designed to protect electronics no matter what.
Myth 2
Another myth is that they’re bad for the environment, maybe because people think they release harmful chemicals when they cure. But actually, UV curable coatings are pretty green. They don’t have volatile organic compounds (VOCs), they don’t use a lot of energy to cure, and they don’t mess with the air quality or add to pollution.
Myth 3
Some folks think UV curable conformal coatings are too pricey. They look at the upfront costs for the curing equipment or the higher price tags on the coatings themselves and get skeptical. But this idea doesn’t hold up when you look at the bigger picture. In reality, these coatings can actually save you money over time.
Here’s why: First off, they dry super fast. This speed boosts how much you can produce, cuts down on labor costs, and lets you make more in less time. Plus, they last longer on the shelf than coatings that use solvents, so you waste less and spend less on materials. And because they stick so well, electronics need less fixing and more staying power, saving you the hassle and expense of redoing work.
Myth #4
Another myth is that these coatings are a hassle to put on, maybe because people think you need fancy gear or special skills. But that’s not true. You can use the usual methods and equipment to apply UV curable conformal coatings just fine.
These coatings come in different thicknesses, so you can brush, dip, or spray them on without a fuss. They flow smoothly, cover evenly, and you don’t have to worry about imperfections much. Plus, they dry in a snap, so you don’t have to wait around forever for things to set. This makes the whole process a lot easier.
Addressing the Myths: Debunking the Misconceptions About UV Curable Conformal Coatings
So, we’ve gone through and busted some big myths about UV curable conformal coatings. Science, industry know-how, and real-life use show that these coatings do what they promise, protecting electronics and making them last longer. It’s important to clear up these myths so everyone knows how useful these coatings really are.
By understanding the truth, manufacturers can feel confident about adding UV curable conformal coatings to their processes. They get all the perks—tough protection, eco-friendly options, versatility for different materials, money-saving efficiency, and straightforward application.
Benefits of UV Curable Conformal Coatings
UV curable conformal coatings are a big win for the electronics world. They do an amazing job at keeping electronic parts safe from moisture, dust, chemicals, and other stuff that could ruin them. This layer of protection makes devices more reliable and long-lasting, cutting down on the chances they’ll break down or not perform well.
These coatings stick really well to a bunch of different materials without causing any damage, which means they can be used on a wide range of electronic parts and materials. They’re also great for covering complex shapes and surfaces, making sure the coating is even and there are no spots that are missed.
On top of all that, these coatings are kind to the environment. They don’t have nasty chemicals or let off harmful things into the air. They use less energy when they’re being cured and don’t add to air pollution. Plus, they last longer before they go bad compared to coatings that use solvents, which means less waste and saving on costs for materials.
Applications of UV Curable Conformal Coatings
These protective coatings aren’t just for electronic gadgets; they’re used in a bunch of different fields. Cars, planes, medical devices, and telecom gear all benefit from them. In cars, they keep the electronic bits working smoothly despite the tough conditions they face. In planes, they help protect against the bumps, moisture, and temperature changes that come with flying.
For medical devices, like pacemakers and insulin pumps, these coatings are super important. They keep the electronics safe from body fluids, making sure these vital devices keep working for a long time. And in the world of telecom, they protect circuit boards and connectors from corrosion, which helps keep signals clear and reliable.
The Future of UV Curable Conformal Coatings in the Electronics Industry
In conclusion, UV curable conformal coatings are super important in the electronics world. They protect electronic devices and help them work better. Even though some people have the wrong idea about these coatings, a lot of research and experience in the industry have shown that these worries aren’t true. These coatings have a lot of good points.
Looking ahead, things seem bright for UV curable conformal coatings in the electronics field. As gadgets get more advanced, smaller, and more complicated, they need protection that’s even more reliable. UV curable conformal coatings are just the ticket for this. They’re tough, don’t hurt the environment, work with many materials, are cost-effective, and are not hard to put on.
People who make electronics and those who work in the industry should really get into using UV curable conformal coatings. Learning all about what these coatings can really do can help make electronic devices more reliable and last longer. Plus, it can make making these devices more efficient and help make the electronics industry more eco-friendly.
For more about addressing the myths and misconceptions about UV curable conformal coatings, you can pay a visit to DeepMaterial at https://www.epoxyadhesiveglue.com/category/epoxy-adhesives-glue/ for more info.