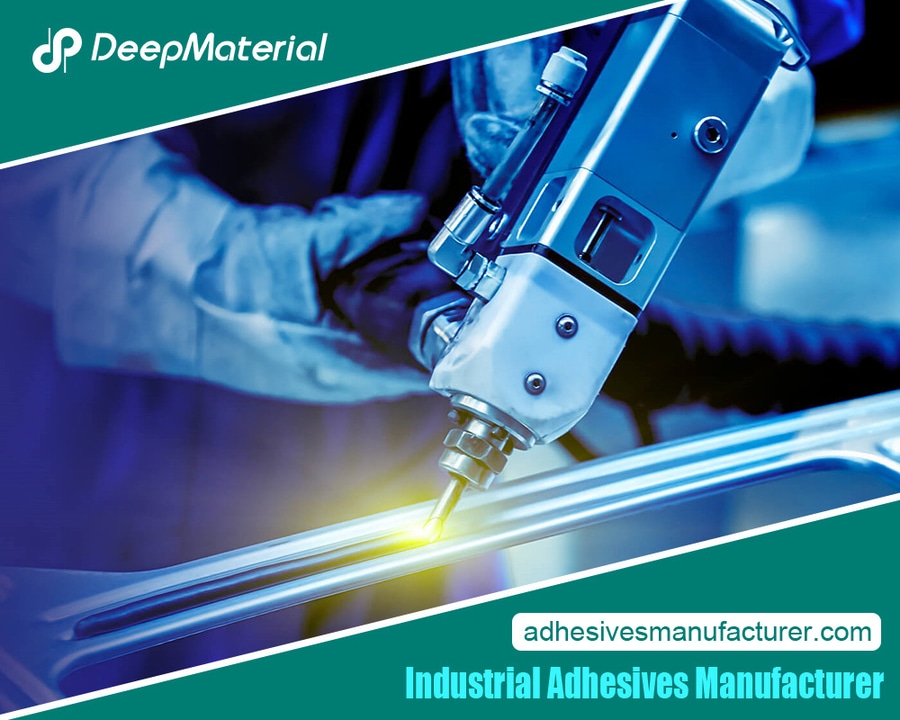
#Industry News
Benefits of conformal coating in the electronics market
Best Conformal Coating Adhesive Glue Manufacturer
The electronic market is serving the diverse needs of customers in various industries. To efficiently serve the customers, they must put in efforts to ensure exceptional performance, reliability, and longevity of electronic devices. Modern electronics are formulated with compact designs and intricate layout of electric circuitry which is more prone to get affected by mechanical stress, electric interference, and environmental effects. To protect electronic devices and ensure that they work efficiently, conformal coating in the electronics market is the right choice. It safeguards the electronic devices from internal connections and external effects to ensure that electronics perform optimally.
In this article, I am going to highlight the essential benefits of conformal coating in the electronics market to give you an idea of why it is a wise decision to apply these coatings on electric equipment.
Protection against environmental effects: Electronics serve many major industries where they are exposed to harsh environmental factors such as humidity, temperature variation, moisture, chemicals, and dust. Conformal coating in the electronics market serves as a protective layer that protects the electric components and circuitry from these environmental factors. It safeguards the components from dust accumulation, moisture ingress, and chemical degradation. The conformal coating keeps the electric components protected and ensures they function optimally even when exposed to a challenging environment.
Resistance against moisture: Moisture can seep through the electric device and proceed toward delicate circuitry leading to short circuits, corrosion, and even component malfunction. Conformal coating in the electronics market works as a moisture barrier that seals the electrical device and protects the components from the harmful effects of water immersion, humidity, and condensation. The conformal coating acts as a resistance against moisture and is applied in multiple major industries including aerospace, automotive, and outdoor applications.
Resistance against chemicals: Exposure to solvents and chemicals is very common in multiple industries including chemical processing units, manufacturing plants, and automotive garages. Exposure to chemicals can disrupt the electrical components and sabotage their functionality. Conformal coating offers exceptional resistance against chemicals. It works as a strong shield to prevent chemical attacks, delamination, and electric failures. Chemical resistance not only helps to protect the internal circuitry but also works to extend the useful life of electronics while lowering the costs related to component maintenance, replacement, or repair.
Mechanical safeguarding: Mechanical stressors including shock, vibration, and physical impact during transit, installation, and function are common in almost all major industries. You cannot minimize the occurrence of these mechanical stressors. So, to protect your electric device against these stressors, the best way is to use a conformal coating. It acts as a durable shield that absorbs the mechanical forces and disperses them without letting them reach the delicate circuitry. It reduces the stress on components, and solder joints and minimizes the risk of mechanical degradation, and, component dislodgement. Conformal coating, when used against mechanical stressors, can enhance the reliability and structural integrity of electronic devices.
Insulation: Without adequate electric insulation, your electronics can face several issues such as electrical leakage, short circuits, electromagnetic interference, and even electric component failure. The conformal coating acts as an ideal insulation that isolates the conductive elements and components and keeps them farther away from each other as well as from external electric instigators. It also helps to maintain the signal integrity and overall performance of electric devices while lowering the risks of electric failure and damage. Electrical insulation is of utmost priority in applications like RF devices, high-voltage applications, and delicate electronic systems.
Efficient thermal management: To maintain the ideal operating temperature for electronic devices, it is necessary to efficiently manage thermal dissipation. Conformal coating proposes high thermal conductivity which aids in efficient heat dissipation that is emitted by active electrical components including central processing units, light-emitting diodes, and power transistors. By efficiently dissipating the heat, conformal coating facilitates minimizing the thermal stress on electric components and adds to its useful life and reliability. In addition, the thermal conductivity of conformal coating can be further enhanced by using additives or thermal conductive fillers during its formulation if you desire an elevated heat dissipation feature for your industry.
Dielectric strength: High-voltage industries need effective insulation that can ensure that the electrical devices functions optimally. Conformal coating formulated with high dielectric strength is powerful enough to bear the high voltages without compromising on operations or electrical arcing. This coating lowers the risk of short circuits and improves the safety of electronic devices in various applications such as telecommunications, power electronics, and medical devices.
Resistance against UV radiations: electronic assemblies that are kept outdoors are exposed to UV radiations that can cause discoloration and degradation of electrical components. Conformal coating that is specially formulated with materials that are UV-resistant extends protection against any possible damage. Using these coatings also ensures that the functionality of electrical circuits is not compromised in any manner. It works as a protective shield that blocks harmful UV rays and prevents electronic devices from degradation in addition to maintaining color stability, optical clarity, and mechanical integrity. These coatings extend the useful life of electronics that are kept outdoors and ensure that they keep on giving reliable performance.
Protection against corrosion: Electrical devices that are exposed to moisture, water, or humidity have a high chances of getting damaged by corrosion. This issue persists in industries that have inevitable contact with moisture, humidity, corrosive gases, or salt spray such as the automotive, marine, and food industries. The conformal coating in the electronics market works as a strong shield against corrosion that protects the electronics from oxidation and rust formation on solder joints and metal surfaces. By protecting against corrosion, these coatings ensure mechanical integrity, electrical conductivity and long-run reliability even when they are exposed to highly corrosive environments.
Aesthetic appeal: Along with protective properties, conformal coating in the electronics market also works on the aesthetic appeal of the electronic assemblies. It offers a consistent, matte, or glossy finish. These coatings are also available in different colors to choose from to give an elegant appeal to your electronic device.
For more about a complete guide to the benefits of conformal coating in the electronics market, you can pay a visit to Deepmaterial at https://www.adhesivesmanufacturer.com/ for more info.