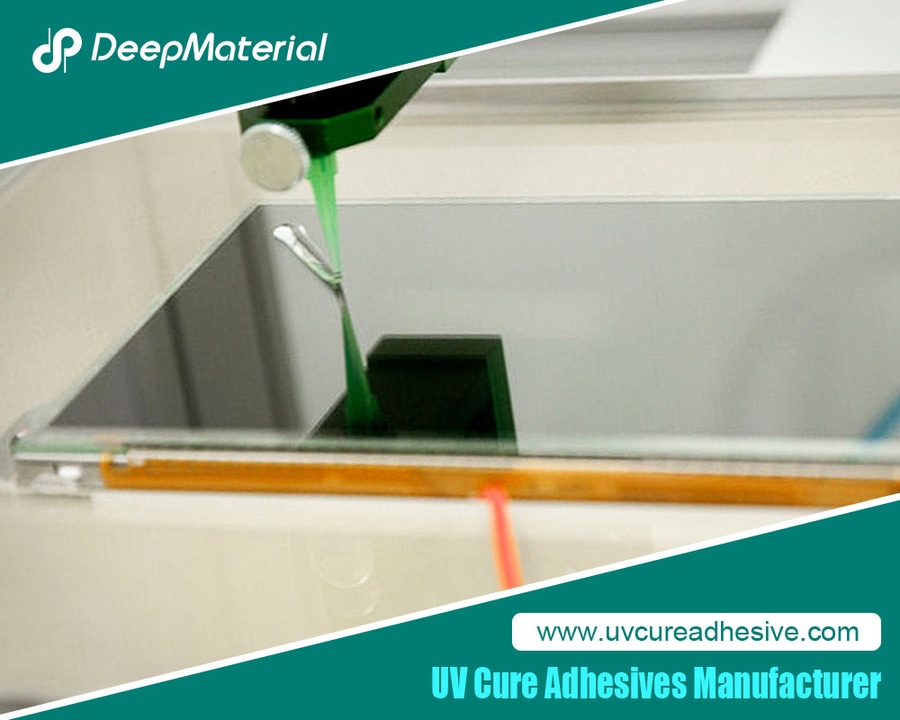
#Industry News
How to Choose the Right UV Cure Adhesive Glue for Rubber to Plastic Bonding
Best UV Cure Adhesive Glue Manufacturer
UV cure adhesive glue is a game-changer in industries like automotive, electronics, and medical devices, offering a swift and effective way to bond rubber and plastic materials. This ensures not only a strong connection but also a durable one. However, picking the right adhesive is crucial for top-notch results and to dodge future headaches. Let’s dive into what you need to consider before making your choice.
Types of Rubber and Plastic Materials
Rubber and plastic come in all sorts of types, each with distinct properties and characteristics that are vital to understand when choosing the right UV cure adhesive.
Rubber might be natural, synthetic (like neoprene or silicone), or an elastomer, with varying degrees of flexibility, chemical resistance, and temperature tolerance.
Plastics could be thermoplastics (like polyethylene or polypropylene) or thermosetting plastics (like epoxy or phenolic), with choices depending on the required strength, rigidity, transparency, and chemical resistance.
Compatibility of Rubber and Plastic Materials
Achieving a strong bond depends heavily on how well the rubber and plastic materials play together. Compatibility is influenced by factors like surface energy, polarity, and chemical composition.
Surface energy is about how much a material’s surface can attract or repel substances. Rubber usually has higher surface energy compared to plastics, which can make bonding a challenge. Surface treatments or primers can boost the surface energy of plastics, making them more compatible with rubber.
Polarity matters too—polar materials (with uneven charge distribution) bond more readily. Non-polar materials might need extra treatments to improve bonding.
The chemical makeup of the materials also matters, especially if they include additives or fillers that could mess with the bonding process. Make sure your adhesive is up to the task and compatible with both materials.
Surface Preparation for Rubber to Plastic Bonding
Properly prepping the surface is critical for a strong bond. Surfaces need to be clean, free of contaminants, and prepped to enhance adhesion.
Start with a thorough clean—remove any dirt, dust, grease, or oils with the right cleaning agents. This ensures the adhesive has direct contact with the material surfaces.
After cleaning, you might need to roughen up the surfaces mechanically (like sanding) to increase the surface area and improve the bond. Chemical treatments such as primers or adhesion promoters can also be used to better the bonding.
However, be careful not to overdo it. Too much sanding or roughening can weaken the materials or create stress points that could cause the bond to fail. Always stick to the manufacturer’s guidelines for surface preparation to avoid these pitfalls.
Application Methods for UV Cure Adhesive Glue
When it comes to applying UV cure adhesive glue for bonding rubber and plastic, there are a few methods to choose from. The method you pick should match the size and shape of the parts, how much you’re producing, and the bond strength you need.
Manual application is a go-to for many, using tools like brushes or syringes to apply the glue. This method lets you be super precise about where and how much glue you use, though it might not be the fastest for bigger jobs.
Automated dispensing steps it up with robots or special equipment doing the gluing, boosting efficiency and consistency. While it’s great for larger operations, it does come with an upfront cost for all that fancy equipment.
Other techniques like spray coating, roll coating, or screen printing might suit specific needs or production setups better. Each method has its ups and downs, so picking the right one depends on what works best for your situation.
Curing Time and Temperature
Getting the cure right is key to a strong and lasting bond. Curing time is how long the glue takes to fully set and reach peak strength. Curing temperature is the heat level the glue needs during this process.
These factors can vary based on the glue you use, how thick your application is, and the materials you’re joining. Always stick to the manufacturer’s guidelines to nail the perfect cure.
Things like the UV light’s intensity, how close the light is to the glue, and the surrounding temperature can all influence the cure. If these aren’t dialed in right, you might end up with a weaker bond or even a bonding failure.
Common slip-ups include not enough UV light, bad curing conditions, or messing with the parts before the glue has fully set. Avoid these to ensure a strong bond.
Strength and Durability of the Bond
The bond’s strength and durability are crucial, especially if the parts need to handle loads or stress. Here’s what can affect the bond:
Adhesive selection: Make sure the glue you pick can handle the demands of your application.
Surface preparation: This is vital. The surfaces should be clean and well-prepped to improve adhesion and avoid failures. Proper prep can make or break the bond strength.
Curing conditions: Good curing practices ensure the glue sets properly, enhancing the bond’s integrity.
To test how strong and reliable your bond is, you can use methods like tensile, shear, or peel testing. These tests give you hard numbers on the bond’s strength and highlight any potential weaknesses.
Considering environmental factors is also crucial for long-term durability. If your bond will face temperature swings, chemicals, or UV light, choose a glue that can withstand these conditions to extend the life of your bond.
Chemical Resistance of the Bond
When using UV cure adhesive glue to bond rubber and plastic materials, it’s crucial to think about chemical resistance. Depending on where they’re used, the bonded parts might come into contact with different chemicals or solvents that could weaken or degrade the bond.
Different chemicals can impact the bond in various ways. Some might cause the materials to swell or soften, which weakens the bond. Others might react with the adhesive itself, breaking it down or reducing its effectiveness.
To ensure solid chemical resistance, pick an adhesive that can handle the specific chemicals or solvents the bonded parts will face. Running compatibility tests or chatting with the adhesive manufacturers can help you choose the best adhesive for your needs.
Testing the chemical resistance of your bond is also vital to confirm its reliability. Performing immersion tests or exposing the bond to specific chemicals can show how well it holds up under real-world conditions. Make sure to do this testing before you start using the bonded parts in their final application.
If you need better chemical resistance, consider using protective coatings or sealants. These can add an extra layer of defense against chemical damage and boost the bond’s durability.
Environmental Factors to Consider
Besides chemical resistance, other environmental factors can affect your bond’s performance. Temperature changes, humidity, UV radiation, and exposure to the outdoors can all challenge the longevity and reliability of your bond.
When selecting a UV cure adhesive glue for bonding rubber to plastic, remember these environmental factors. Some adhesives are specially formulated to endure extreme temperatures or tough environmental conditions, ensuring they perform well over time.
Testing for environmental resistance is also critical. Accelerated aging tests or exposing the bond to simulated environmental conditions can help you see how the bond might hold up over time.
To further improve environmental resistance, you might need additional protective measures like coatings, sealants, or encapsulation. These can help shield the bond from moisture, UV rays, and other environmental threats that could weaken it.
Final Words
In conclusion, UV cure adhesive glue offers a quick and effective bonding solution for various industries. Choosing the right adhesive is key to achieving strong and durable bonds that can stand up to environmental challenges and chemical exposure.
Understanding UV cure adhesive glue—including factors like bond strength, chemical resistance, environmental factors, safety, and cost—is crucial when picking the right adhesive for your project.
For more about how to choose the right UV cure adhesive glue for rubber to plastic bonding, you can pay a visit to DeepMaterial at https://www.uvcureadhesive.com/ for more info.