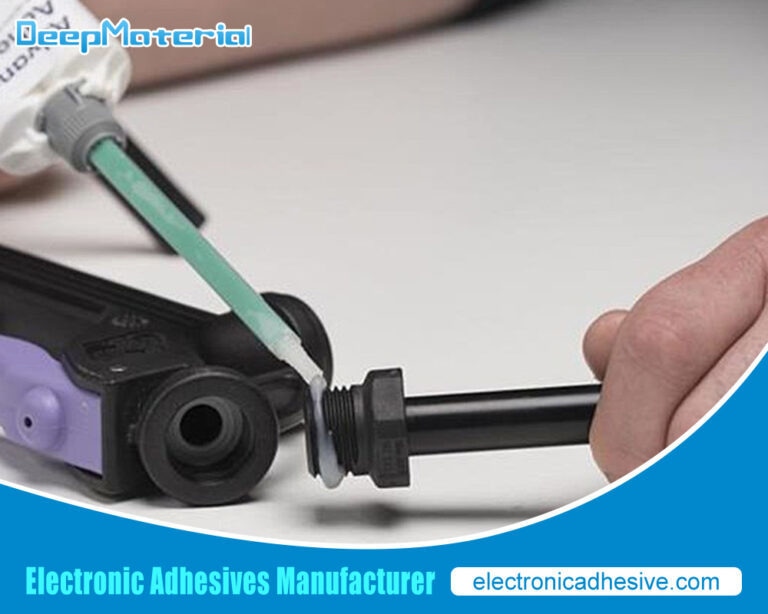
#Industry News
The Roles of Fillers in Enhancing the Properties of Epoxy Adhesive Glue for Metal to Metal Bonding
Best Epoxy Adhesive Glue for Metal to Metal Bonding Manufacturer
Epoxy adhesive glue isn’t just another sticky substance; it’s a powerhouse in the adhesive world, beloved across multiple industries for its serious sticking power. Made up of a resin and a hardener, this dynamic duo becomes a solid, durable bond that can handle just about anything you throw at it, from metals to plastics. Its resistance to chemicals, heat, and sudden impacts makes it a superhero in sectors like aerospace, automotive, construction, and electronics.
Creating Strong Metal-to-Metal Connections
In fields where safety and performance are paramount, the ability to forge strong metal-to-metal bonds is nothing short of essential. Epoxy adhesive glue steps up to this challenge, offering bonds that aren’t just tough but are built to last—even under extreme conditions. Yet, bonding metal isn’t always straightforward due to the smooth nature of metal surfaces, which can sometimes hinder adhesion.
The Role of Fillers in Epoxy Adhesive Glue
This is where fillers come into play, adding a little extra oomph to the already impressive capabilities of epoxy glue, especially for metal-to-metal applications. Whether they’re particles, fibers, or powders, fillers mix into the epoxy to enhance its physical, mechanical, and chemical traits.
Fillers bulk up the epoxy’s resilience, helping it withstand various stresses and strains it might face over a product’s lifetime. They boost everything from tensile and compressive strength to impact resistance, ensuring the bond holds steady no matter what.
But that’s not all—fillers also tweak the thermal and electrical properties of the glue. This tweak is crucial for applications requiring precise temperature control or electrical insulation. Plus, fillers help the glue resist corrosive chemicals, a must-have for products exposed to harsh environments like marine or industrial settings.
Types of Fillers Used in Epoxy Adhesive Glue
Choosing the right filler is key, and the choice depends on what the glue needs to do:
Silica: Great for making the glue thixotropic, which is a fancy way of saying it won’t droop or sag. Perfect for vertical applications, and it also strengthens the glue’s structure.
Alumina: Need to manage heat or keep electrical currents in check? Alumina’s your best bet, enhancing both thermal and electrical conductivity.
Carbon-based Fillers: These are the all-stars, offering a range of benefits from improving UV resistance with carbon black to boosting thermal conductivity with graphite. Carbon fibers? They’re all about enhancing tensile strength and impact resistance.
When it comes to creating the perfect epoxy glue, it’s all about the right mix of fillers. Manufacturers must think about what the adhesive needs to tackle—be it mechanical stress, environmental pressures, or thermal extremes—and choose their fillers accordingly.
Epoxy adhesive glue, with the right fillers, becomes not just a bonding agent but a crucial component in ensuring the integrity and reliability of everything from cars to gadgets. It’s not just about sticking things together; it’s about creating bonds that last, perform, and contribute to the safety and functionality of essential industries. So, next time you see a glue, remember—it’s not just sticky; it’s pretty epic!
Enhancing Mechanical Properties with Fillers
Incorporating fillers into epoxy adhesive glue significantly enhances its mechanical properties, vital for metal-to-metal bonding. Carefully selected fillers improve tensile strength, compressive strength, and impact resistance, ensuring the durability and reliability of metal bonds. Tensile strength is crucial for enduring the pulling forces on bonded components. Using fillers like silica and alumina can boost this property, allowing the adhesive to maintain the integrity of metal-to-metal bonds under stress.
Compressive strength is also enhanced by fillers like alumina, important for applications involving heavy machinery or structural components. For dealing with sudden shocks or impacts, adding fillers like carbon fibers or toughened resins increases the adhesive’s impact resistance.
Improving Thermal and Electrical Conductivity with Fillers
Fillers also play a crucial role in optimizing the thermal and electrical conductivity of epoxy adhesives, making them suitable for metal-to-metal bonding applications that encounter high temperatures or require electrical insulation. Alumina and graphite fillers, for instance, improve thermal conductivity, allowing better heat management within bonded assemblies.
This is beneficial in industries like electronics and automotive, where managing heat is critical. For electrical insulation, non-conductive fillers such as silica or ceramic particles ensure that metal components remain isolated from electrical currents, enhancing safety in electrical applications.
Increasing Chemical Resistance with Fillers
Fillers enhance the chemical resistance of epoxy adhesives, protecting metal surfaces from corrosion and chemical attacks—crucial in harsh environments like marine or industrial settings. Fillers like silica, alumina, and specific types of ceramic fillers create formulations that resist a broad range of chemicals, including acids and solvents. This protection is vital for ensuring the long-term performance and reliability of metal-to-metal bonds.
Optimizing Curing and Adhesion with Fillers
Beyond enhancing physical properties, fillers improve the curing process and adhesion quality of epoxy adhesives. They can accelerate the curing process, critical in industries requiring rapid assembly like automotive and aerospace. Fillers also improve the adhesion between the epoxy glue and metal surfaces by enhancing the wetting and spreading of the adhesive, which is vital for achieving strong and durable bonds. Silane-treated silica or alumina can chemically bond to metal surfaces, improving the interface and preventing bond failure under load.
By carefully selecting and using fillers, manufacturers can tailor epoxy adhesives to meet specific metal-to-metal bonding needs, ensuring optimal performance and durability across various applications.
The Versatility of Fillers in Epoxy Adhesive Glue
In wrapping this up, it’s clear that throwing fillers into the mix of epoxy adhesive glue really spices up its game, especially when it’s about sticking metal to metal. These little enhancers are game-changers. They amp up the mechanical strength, heat resistance, electrical insulation, and chemical defiance of the glue. This means whatever metal parts you’re bonding are in for a long, sturdy relationship.
Choosing the right type and amount of fillers lets manufacturers craft an epoxy adhesive that’s perfect for whatever metals you’re trying to buddy up. Whether it’s for planes, cars, gadgets, or gears, getting the filler blend right means these bonds hold tight under any conditions.
The magic of fillers in epoxy glue isn’t just a bunch of hype; it’s a major league move in adhesive tech. With industries constantly on the hunt for better and more dependable ways to glue stuff together, fillers are sure to stick around in the strategy playbook. They push epoxy glues to new heights, making sure metal bonds in all sorts of fields stay strong and reliable. So yeah, fillers in epoxy? Absolutely clutch for keeping things together.
For more about the roles of fillers in enhancing the properties of epoxy adhesive glue for metal to metal bonding, you can pay a visit to DeepMaterial at https://www.electronicadhesive.com/ for more info.