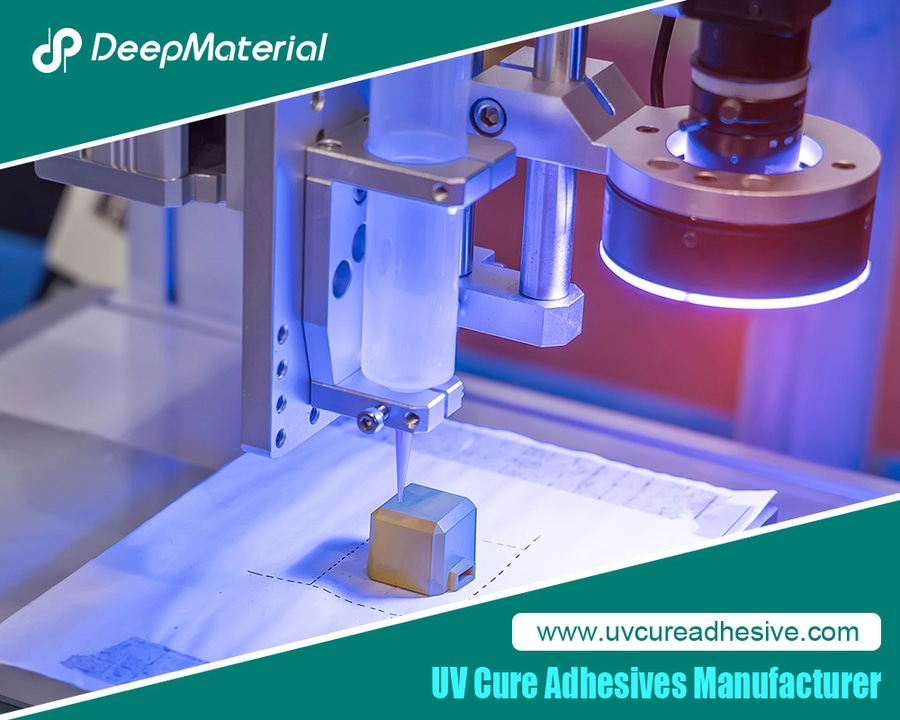
#Industry News
Overcoming Temperature and Humidity Challenges with Structural UV-Curing Adhesives Glue
Best Structural UV Curing Adhesive Glue Manufacturer
Are you wrestling with adhesive failures in extreme environments? Have temperature swings and humidity messed with your product integrity? Step into the world of structural UV-curing adhesives—a revolutionary solution built to endure harsh conditions without dropping the performance ball.
These advanced adhesives forge strong, durable bonds that set quickly under UV light, offering a massive boost in production speed and bond strength. They’re perfect for industries from electronics to automotive manufacturing, delivering reliability where traditional glues just give up.
Dive into how overcoming environmental hurdles with structural UV-curing adhesives can take the quality and durability of your projects to new heights.
Understanding the Challenges of Temperature and Humidity
Temperature fluctuations can throw a real wrench in the works for adhesive performance. Extreme heat or cold can mess with the viscosity, curing rate, and overall properties of adhesives, leading to potential bond failures or compromised product integrity. In places with big temperature swings, it’s crucial for the adhesive to keep its strength and flexibility to ensure the durability of the assembly over time.
Humidity is another curveball—it can disrupt the curing process, resulting in weak or incomplete bonds. Plus, if there’s ongoing exposure to high humidity, it can break down the adhesive over time, weakening the bond.
These environmental factors can create major issues, especially in industries where a failed bond could lead to safety hazards, product malfunctions, or worse. Tackling the challenges posed by temperature and humidity is essential when selecting and applying adhesives.
The Importance of Adhesive Performance in Varying Conditions
It’s vital to maintain strong and reliable bonds in diverse environmental conditions to ensure the integrity and safety of products across various industries. For example, in the automotive industry, structural adhesives are used to bond crucial components like body panels and windshields. These bonds need to withstand everything from blazing hot days to freezing nights. Any failure could raise safety red flags or lead to compliance issues.
In the electronics sector, adhesives secure delicate components and shield them from environmental stress. Fluctuations in temperature and humidity can jeopardize the reliability of electronic devices, making the right adhesive choice critical.
Ensuring product integrity and safety in challenging environments isn’t just about performance—it’s also key to the well-being of end-users. Adhesives that stand up to temperature and humidity changes are crucial in maintaining the reliability and longevity of the products they assemble.
Advantages of Structural UV-Curing Adhesives
Structural UV-curing adhesives have several advantages that make them ideal for tackling temperature and humidity challenges. One major benefit is their quick-setting nature. Exposed to UV light, these adhesives cure rapidly, forming robust bonds in just seconds or minutes. This speed is invaluable in fast-paced manufacturing settings, where quick assembly progression is key.
Besides their swift curing, structural UV-curing adhesives also excel in resisting temperature and humidity shifts. Thanks to their specialized resin systems and additives, they maintain top performance even under tough environmental conditions. This resilience ensures that bonds remain strong and dependable over time, boosting the durability and lifespan of the assembled products.
Another great feature of these adhesives is their versatility in bonding various materials—metals, plastics, composites, and glass, to name a few. This flexibility allows for innovative bonding solutions, paving the way for more efficient and cost-effective product designs in a range of industries and applications.
Formulation Considerations for Temperature and Humidity Resistance
Creating structural UV-curing adhesives that can stand up to the challenges of temperature and humidity involves some serious chemistry. Selecting the right resin systems and adding special ingredients are key to making an adhesive that performs well under different environmental conditions.
Resin systems like acrylates, epoxies, and urethanes form the backbone of these adhesives. Each type of resin has its own set of properties and quirks, so chemists need to pick carefully to match the specific needs of the application. They have to think about things like bond strength, flexibility, and how well the adhesive can handle environmental stress.
Besides the resins, throwing in some specialized additives can boost the adhesive’s ability to cope with thermal and moisture-related stress. Additives like plasticizers and stabilizers can tweak the formula to make the adhesive more durable and reliable under various conditions. Getting this mix just right is crucial for the adhesive’s long-term success.
The curing process itself also gets a lot of attention. The adhesive needs to be designed to set properly under the right UV light conditions. This means tuning factors like the UV light’s wavelength, intensity, and exposure time to nail the perfect cure.
Application Techniques for Optimal Bonding
Getting the best bond with structural UV-curing adhesives isn’t just about slapping some glue on and calling it a day. It starts with making sure the surface is ready to go. Proper cleaning and preparation are crucial to make sure the adhesive sticks well and forms a strong bond.
Prepping the surface might involve degreasing, roughing it up a bit, or applying special primers or coupling agents. These steps clean off any gunk, roughen up the surface to give the adhesive more to hold onto, and help create a stronger mechanical and chemical bond. The right prep method often depends on what materials you’re sticking together and the conditions they’ll face.
When it’s time to apply the adhesive, you’ve got to be precise. The adhesive’s thickness, how you apply it (like dispensing, spraying, or dipping), and how you hold the parts together while it cures all affect the final bond. Doing this right helps avoid any gaps or bubbles that could weaken the bond.
Curing the adhesive is the final, critical step. You’ve got to make sure it gets the right amount of UV light—with the proper wavelength and intensity—to set it properly. Controlling the UV exposure time and managing other factors like temperature and humidity during curing can also help optimize the adhesive’s performance and ensure it lasts.
By paying attention to these details and techniques, you can maximize the effectiveness of your structural UV-curing adhesives and ensure your projects are built to last, no matter the climate!
Testing and Evaluation of UV-Curing Adhesives
Ensuring that structural UV-curing adhesives perform reliably under temperature and humidity challenges requires rigorous testing and evaluation. Laboratory tests are key for checking how well these adhesives can handle environmental stresses while maintaining their bond strength and integrity.
Common lab tests for assessing temperature and humidity resistance might include thermal cycling, high and low temperature exposures, and tests in high humidity conditions. These tests aim to mimic the real-world scenarios the adhesive will face, helping to evaluate its performance under stress.
Conclusion
Structural UV-curing adhesives have become a go-to solution for tackling the challenges of temperature and humidity across various industries and applications. Thanks to their quick curing, strong initial bond strength, and exceptional resistance to environmental stresses, these adhesives are invaluable for manufacturers and designers aiming to produce reliable, durable, and high-performance products.
The capability of structural UV-curing adhesives to hold up against temperature changes and humidity is a clear sign of progress in adhesive technology. By carefully formulating these adhesives with the right resins and special additives, and using the best application methods, manufacturers can ensure their bonded assemblies are durable and safe for the long haul.
For more about overcoming temperature and humidity challenges with structural UV-curing adhesives glue, you can pay a visit to DeepMaterial at https://www.uvcureadhesive.com/ for more info.