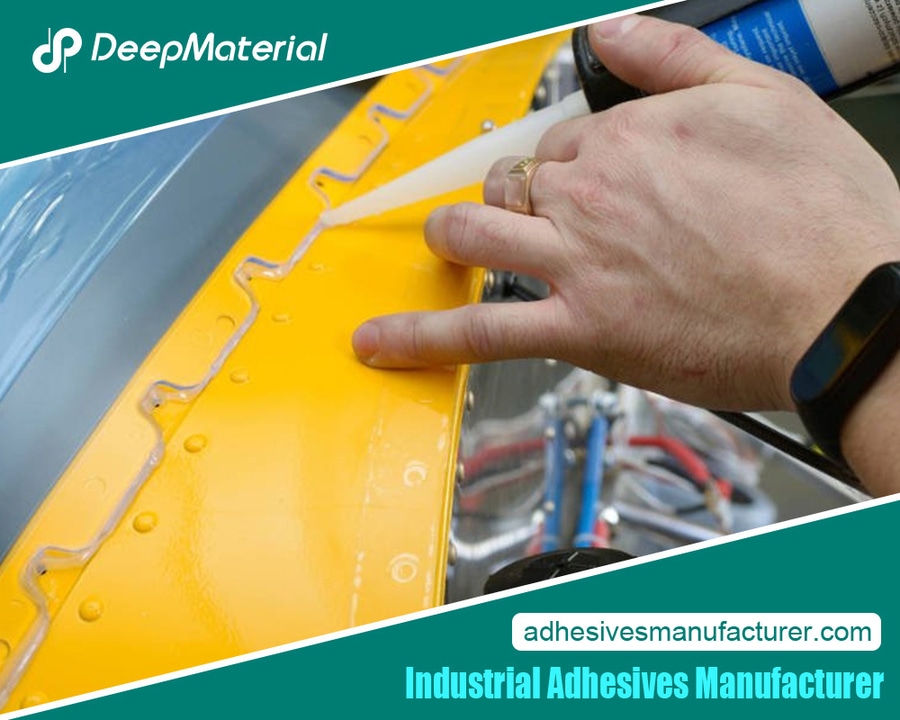
#Industry News
Exploring the Impact of Contamination on Epoxy Conformal Coating Performance
Best Epoxy Conformal Coating Adhesive Glue Manufacturer
Epoxy conformal coatings are like superheroes for electronic components, shielding them from moisture, dust, and chemical sneak attacks. But, just like every superhero has a weakness, these coatings can be undermined by surface contamination during application.
This article dives into how contaminants like oils, dust, and moisture can mess with the effectiveness of epoxy conformal coatings. We’ll explore how these unwanted guests interfere with the adhesion and integrity of the coating and emphasize why top-notch surface prep is a must for the best protection.
Understanding Contamination in Conformal Coating Processes
Contamination in the conformal coating process comes in various forms, each bringing its own headaches. The big three troublemakers for epoxy conformal coatings are particulate, ionic, and organic contaminants.
Particulate contaminants—think dust, dirt, and other floaty nuisances—can embed themselves in the coating while it’s being applied. They act like tiny shields, stopping the coating from sticking properly to the surface underneath. This can lead to delamination, where the coating peels away, poor adhesion, and even total coating failure. After all, if the coating can’t bond solidly, it can’t protect effectively.
These pesky particles can come from anywhere—the manufacturing environment, how the components are handled, or even the quality of the materials used in the coating itself. Sloppy air filtration, shoddy cleaning, and careless handling are all open invitations for particulate gate-crashers.
On the flip side, ionic contaminants are charged particles that can react with the chemical structure of the epoxy, leading to degradation and potential corrosion of what’s underneath. These baddies can sneak in through improper cleaning, using dirty solvents, or leftover residues from soldering.
The Impact of Particulate Contamination on Coating Adhesion
When particulates gatecrash the coating party, they create barriers that prevent the epoxy from forming a tight bond with the base surface. This can cause uneven coverage, poor wetting, and tiny air pockets or voids in the coating.
With a weak bond, the coating is more likely to delaminate, exposing the delicate electronics beneath to the very elements it’s supposed to guard against. This increases the risk of corrosion, short circuits, and other electronic nightmares.
Moreover, a bad adhesion job can lead to cracks or flakes in the coating, which just invites more contaminants inside, setting off a domino effect of degradation and potential failure in the electronic assembly.
So, keeping things clean before coating isn’t just about being neat; it’s crucial for keeping your electronics safe from the environmental big bads.
The Role of Ionic Contamination in Coating Degradation
Ionic contaminants can really mess with the performance and integrity of epoxy conformal coatings. They bring about issues that threaten the long-term reliability of electronic assemblies.
These charged particles, including salts and acids, mingle with the epoxy’s chemical makeup, causing it to break down. This can lead to corrosion, insulation failures, and even create conductive paths that could cause short circuits and electrical failures.
Ionic contaminants can also lead to the growth of dendrites—those pesky, tree-like metallic structures that grow across the coating. These dendrites act like bridges for electricity, potentially leading to more short circuits and electrical issues.
Beyond just messing with the coating, these contaminants can corrode metal traces, solder joints, and other critical parts of an electronic assembly. This can trigger a domino effect of failures, jeopardizing the device’s performance and reliability.
Examining the Effects of Organic Contaminants on Coating Integrity
Organic contaminants, like oils, greases, and solvents, also pose significant risks to the integrity of epoxy conformal coatings. They can prevent the coating from properly adhering to the substrate, causing poor coverage, blistering, and delamination.
These contaminants can alter the epoxy’s properties, reducing its ability to resist moisture, chemicals, and temperature changes. Sources of organic contamination vary but often come from handling, storage, using improper cleaning agents, or leftover manufacturing oils on the substrate.
If surface preparation is sloppy and doesn’t remove these contaminants, they can sneak into the coating process. Once there, they act like barriers between the coating and the substrate, preventing a strong bond. This can lead to air pockets and voids within the coating, which then become gateways for environmental elements to seep in and weaken the coating’s protective power.
Strategies for Mitigating Contamination in Conformal Coating Application
Keeping a clean and controlled environment is absolutely essential when it comes to ensuring the best performance and reliability of epoxy conformal coatings. Let’s face it, contamination—whether from particulates, ions, or organic material—can really mess with a coating’s ability to stick to the substrate, safeguard the electronics beneath, and hold up against environmental challenges.
To fight the effects of contamination, manufacturers and engineers need to adopt a thorough approach that tackles various contamination sources throughout the entire coating process. This includes using top-notch air filtration systems, enforcing strict cleaning and surface preparation rules, and choosing raw materials and equipment that keep contamination to a minimum.
A major move for keeping things clean in the conformal coating process is to create clean, controlled environments. This might mean setting up special coating rooms or enclosures where everything from air quality to temperature and humidity is meticulously controlled. Employing high-efficiency particulate air (HEPA) filters and other sophisticated air filtration systems can play a big part in removing airborne particles, ensuring the coating environment is as pristine as possible.
Wrapping Up
In wrapping things up, our deep dive into how contamination affects epoxy conformal coating performance has unearthed some important insights. It turns out, usual suspects like dust, oils, and moisture can seriously undermine the adhesion and integrity of epoxy coatings. This leads to less effective protection and might even cause electronic components to fail. Our findings highlight just how critical thorough surface preparation is—making sure all those nasty contaminants are gone before you even start coating.
Moreover, this study shows how crucial it is to pick the right cleaning methods that are specifically suited to tackle particular contaminants, ensuring optimal coating performance. Looking ahead, future research should focus on coming up with advanced coating formulas and application methods that are tougher on common contaminants. This could really boost the reliability and lifespan of coated electronic devices, making them more resilient in the face of contamination challenges.
For more about exploring the impact of contamination on epoxy conformal coating performance, you can pay a visit to Deepmaterial at https://www.adhesivesmanufacturer.com/ for more info.