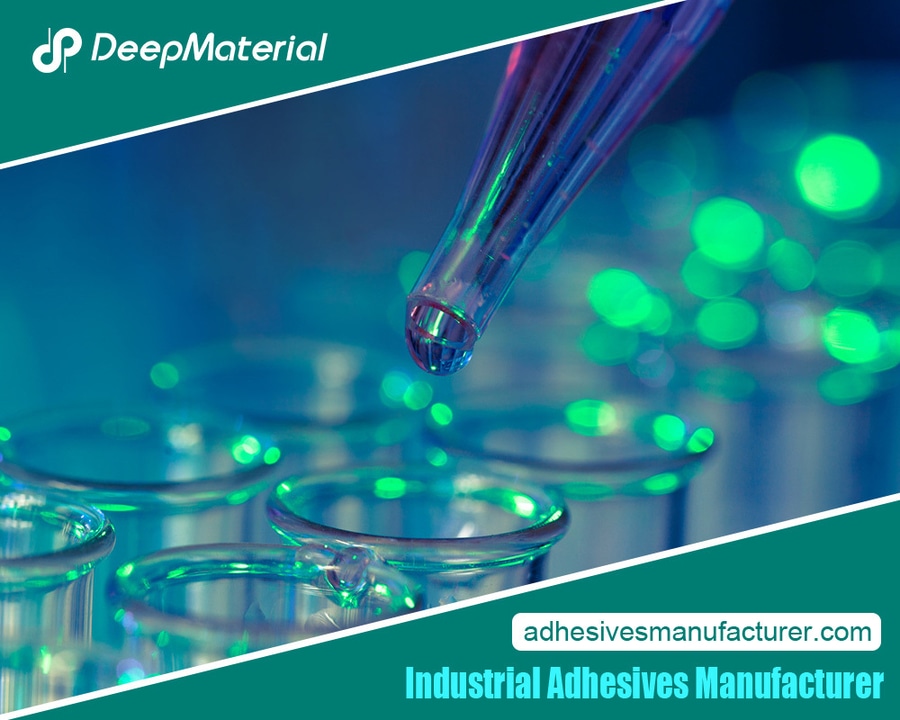
#Industry News
The Impact of Temperature on the Performance of Non-Conductive Epoxy Adhesive Glue in Electronics
Best Non-Conductive Epoxy Adhesive Glue Manufacturer
Non-conductive epoxy adhesive glue isn’t just a sticky substance; it’s a linchpin in the electronics industry. These adhesives are celebrated for creating strong, durable, and insulating bonds between diverse components and materials. They’re a go-to in assembling and fabricating electronic devices, where their unique properties are nothing short of essential for manufacturers.
Epoxy adhesives boast remarkable adhesive strength, chemical resistance, and thermal stability. This makes them a favorite for a multitude of electronic applications—from assembling circuit boards to encapsulating delicate components. These adhesives ensure structural integrity and reliability of electronic devices. Plus, their non-conductive nature is perfect for applications needing electrical isolation, such as in devices that handle high voltages or frequencies.
The Role of Epoxy Adhesives in Electronics
In the realm of electronics, epoxy-based adhesives are critical. They’re used extensively to assemble and fabricate electronic components and devices. These adhesives are key in securing and aligning various parts, ensuring mechanical stability and integrity of the entire assembly. They find their way into numerous applications, like bonding electronic components and encapsulating sensitive circuitry, offering a steadfast and durable attachment method.
The benefits of using epoxy adhesives in electronics are many. They trump other bonding methods like mechanical fasteners or soldering with their superior strength, flexibility, and gap-filling capabilities. This makes them especially valuable in applications where even stress distribution and load-bearing are crucial. Moreover, epoxy adhesives can provide electrical insulation, manage heat, and resist chemicals, making them ideal for tough electronic environments.
Their widespread use in the electronics industry attests to their versatility and efficacy. Epoxy adhesives have become a fundamental part of the manufacturing process, enabling the production of complex and compact electronic devices that meet the evolving demands of the market.
Understanding the Importance of Temperature in Adhesive Performance
Temperature plays a pivotal role in the performance and reliability of epoxy adhesives in electronic applications. The properties and behavior of these adhesives can be significantly influenced by temperature changes, which can crucially affect the integrity and functionality of electronic assemblies.
In the electronics industry, where devices often face a wide range of operating temperatures, from bitter cold to scorching heat, understanding how temperature impacts epoxy adhesives is crucial. Temperature fluctuations can cause thermal expansion, material degradation, and changes in the adhesive’s mechanical properties, all of which could undermine the reliability and durability of the electronic assembly.
Grasping the effects of temperature on epoxy adhesives is key to ensuring the long-term performance and stability of electronic devices. By thoughtfully considering the thermal characteristics of both the adhesive and the materials it bonds, manufacturers can fine-tune their choice and application of epoxy adhesives, significantly boosting the overall reliability and performance of their electronic products.
Thermal Expansion and its Impact on Epoxy Adhesive Bonds
Understanding the effects of temperature on epoxy adhesives in electronics? It’s essential to grasp thermal expansion. As materials are exposed to temperature changes, they expand or contract. This can seriously affect the integrity and performance of epoxy adhesive bonds in electronic assemblies.
When materials bonded by epoxy have different rates of expansion (thanks to differing thermal expansion coefficients), it creates stress within the adhesive bond. With temperature fluctuations, these materials expand and contract at different rates, stressing the adhesive through shear and tensile forces. Over time, this stress can weaken the bond, possibly leading to failure or delamination of the components.
This issue becomes a real headache in environments where electronics face extreme temperature changes—like in automotive, aerospace, or industrial settings. Here, the constant expanding and contracting can degrade the adhesive bond, undermining the reliability and performance of the electronic assembly.
To dodge these thermal mishaps, manufacturers need to pick epoxy adhesives whose thermal expansion coefficients closely match those of the materials being bonded. This careful selection helps the adhesive bond endure temperature-induced stresses, preserving the long-term integrity and reliability of the device.
The Effect of Low Temperatures on Epoxy Adhesive Strength
Cold temperatures bring their own challenges to epoxy adhesives. When it gets chilly, epoxy adhesives can become less flexible and more brittle. This change affects the reliability and durability of electronic assemblies.
As the mercury drops, the molecular structure of the epoxy stiffens, impacting its mechanical properties. The adhesive becomes rigid, less capable of handling movement between bonded materials, and more likely to fail. This brittleness is especially problematic in scenarios where the electronic device faces mechanical stresses like vibrations or impacts since the less-flexible adhesive might not effectively absorb these forces.
The consequences of poor low-temperature performance are significant in the electronics industry. Devices used outdoors, in military equipment, or in aerospace systems, which often operate in cold environments, are particularly at risk. If the adhesive bond fails, components can separate, compromising the structural integrity and functionality of the assembly.
To tackle low-temperature challenges, manufacturers must select epoxy adhesives formulated to maintain their flexibility and strength in the cold. By choosing adhesives tailored for colder conditions, they can ensure the reliable and durable performance of electronic devices across diverse climates.
The Impact of High Temperatures on Epoxy Adhesive Durability
Just as cold temperatures pose risks, high temperatures can also threaten the performance and durability of epoxy adhesives in electronics. When exposed to high heat, epoxy adhesives can soften and potentially degrade, jeopardizing the reliability and longevity of electronic assemblies.
With rising temperatures, the molecular structure of epoxy adhesives changes, weakening their mechanical properties. The adhesive might soften, losing its ability to hold components firmly together. In severe cases, the adhesive could degrade completely, leading to bond failure and separation of the assembled parts.
High-temperature failures are a serious concern in the electronics industry, where devices often operate in hot conditions or environments. If the adhesive bonds fail, critical components could shift or detach, causing device malfunctions, performance issues, or total failures. This is particularly problematic in industrial, automotive, or aerospace systems, where devices are expected to perform reliably over long periods.
To minimize high-temperature risks, manufacturers need to choose epoxy adhesives that can withstand the heat without losing their bonding strength and durability. By selecting adhesives with suitable thermal resistance, they can ensure the long-term reliability and performance of electronic devices, even in the face of high temperatures.
Optimizing Epoxy Adhesive Performance Through Temperature Management
Temperature plays a huge role in the world of non-conductive epoxy adhesive glue used in electronics, and it’s something manufacturers can’t afford to ignore. These adhesives are the unsung heroes in the assembly and fabrication of electronic components, providing much-needed structural integrity and electrical isolation. This keeps everything functioning smoothly within electronic systems.
Yet, the performance and durability of these adhesives are at the mercy of temperature fluctuations. These can stir up a whole host of troubles, from thermal expansion-induced stress (where things get too tight for comfort) to the softening or outright degradation of the adhesive material. Getting a grip on how temperature affects adhesive behavior is key for manufacturers aiming to enhance the reliability and lifespan of their electronic products.
Understanding this tricky temperature-adhesive relationship is critical. It’s all about keeping those electronic devices dependable over the long haul, despite the temperature tantrums they might face in their environments. By mastering this, manufacturers can ensure their products are ready to perform under pressure, staying intact and isolated, just as they need to be.
So, next time you think about electronic adhesives, remember it’s not just about sticking things together—it’s about keeping them cool, or warm, enough to keep sticking around for the long run!
For more about the impact of temperature on the performance of non-conductive epoxy adhesive glue in electronics, you can pay a visit to Deepmaterial at https://www.adhesivesmanufacturer.com/ for more info.