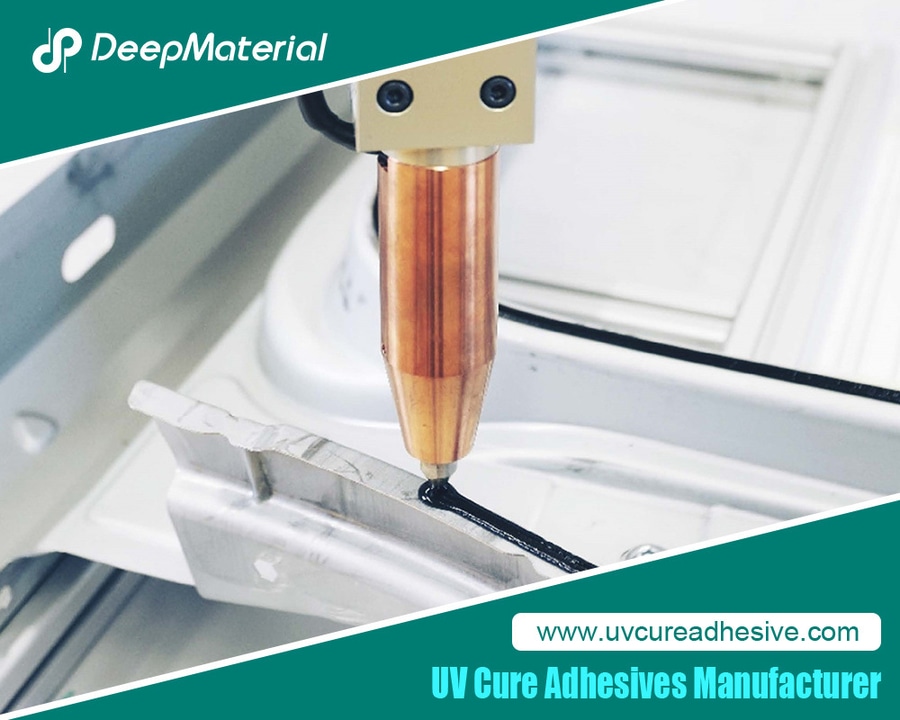
#Industry News
Can Flexible UV-Curing Adhesives Glue Be Used In Electronic Assembly
Best UV Curing Adhesive Glue Manufacturer
Have you ever marveled at how the tiny, intricate components of your electronic gadgets stay put? Imagine a method that could speed up and enhance the assembly process. Well, that’s where flexible UV-curing adhesives step into the spotlight.
These innovative glues are transforming the way electronic components are put together. But what makes them so exceptional, and could they really be the game-changer in electronics manufacturing? Let’s dive into what makes flexible UV-curing adhesives a standout choice in the bustling world of electronics production.
Adhesive Properties for Electronic Applications
Optical clarity and transparency are key for adhesives used in electronics. Devices like displays and sensors need the glue to be clear so it doesn’t mess with visibility or function. Flexible UV-curing adhesives can be specially made to be crystal clear, letting light pass through without distortion.
Dielectric properties and insulation are also vital. Electronic circuits need good insulation to avoid shorts and keep things running smoothly. Flexible UV-curing adhesives can be engineered to offer excellent insulation, making sure they don’t mess with the electronic signals or functionality.
Lastly, resistance to chemicals, moisture, and other environmental nasties is crucial. Electronics often face harsh environments, so the adhesives used need to be tough. Flexible UV-curing adhesives can be formulated to stand up to these challenges, ensuring the electronic assembly stays robust throughout its life.
Curing Mechanisms and Considerations
The curing process of flexible UV-curing adhesives is a key part of their success in electronic assembly. These adhesives start curing when hit with certain wavelengths of ultraviolet (UV) light. This triggers photoinitiators in the adhesive, kicking off chemical reactions that harden the adhesive and form a strong bond.
Several factors impact how well these adhesives cure. The intensity and wavelength of the UV light are crucial—stronger light and specific wavelengths can speed up the curing, while weaker light or the wrong wavelength might lead to uneven or incomplete results.
Exposure time to UV light also matters a lot. Too little light, and the adhesive won’t cure fully; too much, and you might damage the adhesive or cause other problems. Getting the curing conditions just right is vital for optimal adhesive performance and reliability.
Compatibility with Electronic Components
Flexible UV-curing adhesives are made to work well with many materials used in electronic assembly, such as metals, plastics, ceramics, and other substrates. It’s important that these adhesives don’t mess with the electronic components’ function. Some adhesives might have conductive or magnetic materials that could interfere with electronic circuits or sensors. UV-curing adhesives are formulated to avoid these issues, so they’re safe to use with sensitive electronics.
Making sure the adhesive bonds well with the specific materials in your project without damaging them is crucial. Selecting and testing the right adhesive ensures it will perform well in your electronic assembly setup.
Advantages Over Traditional Adhesives
One big plus of flexible UV-curing adhesives over traditional ones is how quickly they set, which boosts productivity. Traditional adhesives, like epoxies or cyanoacrylates, often need a long time or added heat to fully bond. UV-curing adhesives, however, set almost instantly under UV light, slashing assembly time and upping efficiency.
Also, these adhesives don’t need heat or solvents to cure, which is great for electronic assembly. Heat and solvents can harm sensitive components and raise safety and environmental concerns. UV-curing adhesives skip these risks, making the assembly process safer and cleaner.
On top of speeding up assembly, flexible UV-curing adhesives are safer and more environmentally friendly. Traditional adhesives often contain volatile organic compounds (VOCs) or other harsh chemicals that can pose health risks and harm the environment. UV-curing adhesives can be made with fewer or no harmful substances, offering a greener, safer option for electronic manufacturing.
Application Techniques in Electronic Assembly
Getting flexible UV-curing adhesives right in electronic assembly calls for a keen eye on the different dispensing and coating methods available. Depending on what you’re sticking together and how thick the adhesive is, you might go with needle dispensing, bead or dot dispensing, or even dive into automated coating processes.
Preparing the surface and how you apply the adhesive are big deals too. Properly cleaning and treating the surface, maybe with plasma or corona treatment, can really boost the bond strength. Plus, the way you apply the adhesive—like controlling the flow rate and pressure with some fancy equipment—can make or break the quality and consistency of your bond.
Fitting UV-curing equipment into your electronic assembly line is another piece of the puzzle. Picking and placing the right UV light sources, like LED or mercury-vapor lamps, really matters. Planning this step well helps crank up productivity and ensures that the UV-cured bonds are consistently strong and reliable.
Reliability and Durability of UV-Cured Bonds
For UV-cured adhesive bonds in electronics, playing the long game—meaning how they hold up over time and under stress—is key. These adhesives are champs at sticking things together even when faced with temperature swings, humidity, and other fun stuff like mechanical stresses.
It’s crucial to test that these bonds can hang tight for the expected life of your electronic gizmo. Manufacturers often run the gamut of tests—think accelerated aging, thermal cycling, and shaking things up with vibration testing. These tests spot any weaknesses and help you make smart choices about using the adhesive for your particular needs.
Keeping the bond strong and intact over time is essential for your electronic devices to work like a charm, every time. By picking the right adhesive and making sure it’s up to snuff, electronics manufacturers can rest easy knowing their products are reliable.
Considerations for Implementing Flexible UV-Curing Adhesives
When you’re bringing flexible UV-curing adhesives into your electronic assembly, it’s crucial to think through what your manufacturing process and final product really need. Every electronic gadget and assembly line has its quirks, and these need specific adhesives to handle them.
Choosing the right adhesive is step one. You’ve got to consider how flexible and strong it needs to be, its optical qualities, and whether it plays nice with the materials you’re using. Chatting with adhesive manufacturers and running thorough tests helps make sure the adhesive you pick fits like a glove.
Getting the UV-curing gear and process dialed in is just as important. This might mean picking out UV light sources, tweaking curing times and settings, and setting up quality checks to keep things on track. And don’t forget about training your team—everyone needs to be on board and in the know to keep the assembly line running smoothly.
By carefully assessing what you need, choosing the right adhesive, and getting your equipment and team lined up, you can tap into the full potential of flexible UV-curing adhesives. This strategic approach not only boosts product reliability and cranks up productivity but also pushes forward environmental sustainability in the cutthroat world of electronics.
For more about flexible UV-curing adhesives glue be used in electronic assembly, you can pay a visit to DeepMaterial at https://www.uvcureadhesive.com/ for more info.