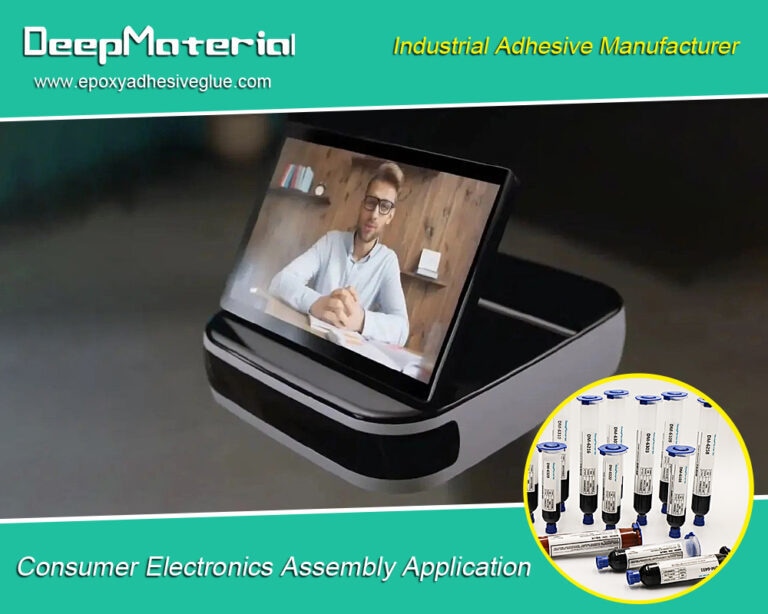
#Industry News
Can Flexible UV-Curing Adhesives Glue Improve A Product’s Durability?
Best UV Curing Adhesive Glue Manufacturer
Ever pondered how the latest leaps in adhesive tech might extend the life of your products? Could the clever use of flexible UV-curing adhesives be the secret to boosting their durability? At a time when lasting power and sustainability are top priorities, grasping the role of these advanced adhesives could totally transform product design and manufacturing.
This article dives into the universe of flexible UV-curing adhesives, exploring their potential to not only beef up product durability but also to offer fresh solutions to age-old challenges across various industries. Let’s find out if these high-tech glues really are the superheroes of product resilience.
Understanding the Advantages of Flexible Adhesives
Flexibility in adhesives is key because it lets them go with the flow, literally—accommodating material movements without breaking a sweat. Where traditional stiff adhesives might crack under pressure, flexible adhesives play it cool, absorbing shocks and staying intact.
What sets flexible apart from rigid adhesives is all in the molecular makeup. Rigid adhesives, made from brittle polymers, tend to give up under stress, but flexible adhesives are like the yoga masters of the adhesive world—elastic and adaptable. This flexibility allows them to stretch and bend without losing their grip, perfect for jobs where materials need to move without breaking apart.
The real magic of flexible UV-curing adhesives is in their tough-as-nails nature, ready to take on impact forces, thermal shifts, and environmental challenges, all while keeping a strong bond across a variety of materials. Engineered to endure harsh conditions, these adhesives ensure whatever they’re holding together stays together.
Improved Shock and Impact Resistance
One of the top perks of flexible UV-curing adhesives is their knack for soaking up and managing impact forces, making them essential for situations where bumps and bangs are the norms.
Take the automotive sector, where flexible UV-curing adhesives are heroes for bonding parts that take a beating—like body panels and interior bits. They handle the rough and tumble of the road, from potholes to fender-benders, keeping everything tight and right.
In electronics, these adhesives are the behind-the-scenes protectors of fragile components. They cushion the blow when gadgets take a tumble, keeping the insides safe so your devices keep ticking.
Case studies show just how awesome these adhesives are under pressure. For example, a sports equipment maker turned to a flexible UV-curing adhesive for their newest gear. Thanks to the adhesive’s shock-absorbing powers, the equipment could take on extreme sports without falling apart, making it safer and longer-lasting for thrill-seekers everywhere.
Enhanced Flexibility for Moving Parts
The give and take of UV-curing adhesives is a huge plus in situations where parts move and flex a lot. Traditional stiff adhesives can give up when things get too bendy, leading to breakages and less-than-stellar product performance.
In the car world, flexible UV-curing adhesives are the go-to for parts like door panels, sunroofs, and convertible tops that really need to move. They’re built to handle the stretching and bending that comes with the territory, making sure everything stays stuck right where it should through countless opens and closes.
Over in electronics, these adhesives keep things together in gadgets that twist, bend, or fold. They stick with it, maintaining their hold and keeping tech functioning smoothly, no matter how much you flex them.
A great example of this in action is in the production of flexible displays. These need to roll with the punches—literally—so they need an adhesive that can bend without breaking. Flexible UV-curing adhesives are perfect here, ensuring these nifty displays can handle daily wear and tear without coming unstuck.
Increased Thermal Stability and Weathering Resistance
Adhesives can get a little touchy under extreme environmental conditions like wild temperature swings or harsh weather. Standard glues might not hold up, which can lead to your bond—and your day—falling apart.
However, flexible UV-curing adhesives are made tough. They’re mixed with special polymers and additives that help them resist the trials of temperature changes, UV rays, and other environmental challenges.
In autos, these adhesives are used everywhere from hot engine compartments to ice-cold exteriors. They keep their cool (or heat) even when the mercury jumps or drops, ensuring things stay glued together.
And it’s not just cars. In construction and outdoor gear, these adhesives face down rain, snow, and sun without blinking, helping everything from buildings to bikes last longer and perform better, no matter the weather.
Bonding Dissimilar Materials with Ease
Gluing different materials together is often a sticky situation for regular adhesives, thanks to varying surface textures and reactions to temperature changes. But flexible UV-curing adhesives are up for the challenge, sticking just about anything to anything with ease.
These adhesives are packed with clever chemistry that lets them grab onto diverse materials, whether it’s metal, plastic, composite, or glass. Their flexibility helps them handle the different ways these materials behave, keeping bonds strong even when things heat up or cool down.
In electronics, for example, these adhesives hold together components like metal heat sinks and plastic casings, ensuring devices work reliably without coming apart at the seams.
And in cars, they’re a critical part of the assembly process, allowing manufacturers to use the best material for the job without worrying about whether things will stick. This flexibility opens up a world of design possibilities, making cars not just stronger and safer but also more innovative.
Faster Curing Times for Improved Productivity
The speed at which adhesives cure is crucial because it can really make or break the pace and cost-effectiveness of manufacturing. Traditional adhesives often take their sweet time to set, which can slow down the whole production line and bump up costs.
Enter flexible UV-curing adhesives. These speed demons set much quicker than other adhesives thanks to some clever chemistry involving photoinitiators and a blast of UV light. This quick action turns the glue from liquid to a solid bond in no time.
This rapid curing is a big plus for manufacturers. It slashes the waiting time for adhesives to dry, boosts the number of products you can push through the production line, and cuts costs by needing less time and fewer hands. It’s also handy for getting products out the door faster, particularly in fast-moving industries like consumer electronics and car manufacturing.
There are plenty of success stories out there. For example, a consumer electronics manufacturer used a flexible UV-curing adhesive in their latest gadgets. The fast cure time sped up their assembly line, chopping down production time and helping them get their products to eager consumers quicker.
Evaluating the Durability of UV-Cured Adhesive Bonds
When it comes to adhesives, it’s not just about sticking things together—it’s about keeping them stuck. To make sure flexible UV-curing adhesives can handle the heat (and the cold, and the stress, and the strain), they undergo a battery of tests. These tests measure how well the adhesives can hold up against pulling, bending, smacking, heating, cooling, and getting rained on.
Manufacturers put their adhesives through these tough trials to understand how they’ll perform in the real world. They compare the results against established standards to ensure each batch of glue is up to snuff, offering the strength, flexibility, and weather resistance needed for the job.
Understanding these test results is key for manufacturers to make smart choices about which adhesives to use. It helps them ensure that the products will hold up under pressure and over time, which is crucial for customer satisfaction and safety.
Final Thoughts
To wrap it up, flexible UV-curing adhesives bring a lot to the table. They’re not just fast; they form strong, durable bonds that stand up to a lot of abuse, making them ideal for applications where reliability is key. They’re also neat and efficient, reducing waste and making them a greener choice for sticking things together.
As adhesive technology gets even better, the potential uses for flexible UV-curing adhesives are set to grow, promising to boost product durability and performance in many more industries. Whether you’re in electronics, automotive, or any other field, these adhesives could be what you need to stick it to the competition.
For more about flexible UV-curing adhesives glue can improve a product’s durability, you can pay a visit to DeepMaterial at https://www.epoxyadhesiveglue.com/category/epoxy-adhesives-glue/ for more info.