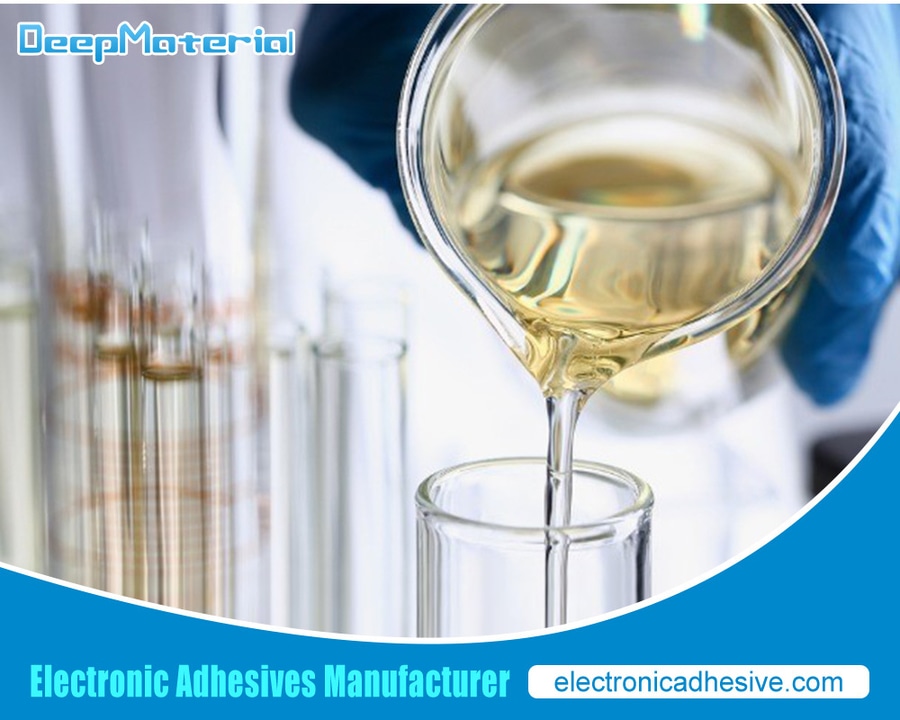
#Industry News
Evaluating the Impact of Filler Type on Flame Retardancy of Electronic Epoxy Encapsulant Potting Compounds
Best Electronic Epoxy Encapsulant Potting Compounds Adhesive Glue Manufacturer
How can we enhance the safety of electronic devices while maintaining their performance and durability? One key is in the development of epoxy encapsulant potting compounds, which serve as armor for sensitive electronic components. The choice of filler material in these compounds plays a huge role in their ability to resist flames—a crucial feature to avoid fiery mishaps.
This article digs into how various filler types affect the flame retardancy of electronic epoxy encapsulants. We’ll explore different mixtures and their fire-resisting powers, aiming to shed light on paths toward safer and more dependable electronic products.
Importance of Flame Retardancy in Electronic Devices
The risk of fire hazards in electronic devices is a significant concern that must be addressed. Electronic components like integrated circuits, power supplies, and batteries can generate heat during operation, and in case of a malfunction or short circuit, this heat can lead to the ignition of surrounding materials. The consequences of a fire in an electronic device can be severe, ranging from property damage to personal injury and even loss of life.
To mitigate these risks, regulatory bodies and industry standards have set stringent requirements for flame retardancy in electronic equipment. For example, the Underwriters Laboratories (UL) standard UL 94 and the International Electrotechnical Commission (IEC) standard IEC 60695-11-10 provide guidelines and test methods for evaluating the flammability of materials used in electronic devices.
These standards ensure that the materials used in the construction of electronic products meet minimum requirements for flame retardancy, reducing the risk of fire hazards and ensuring the safety of end-users.
Overview of Filler Types for Epoxy Encapsulants
Epoxy encapsulant potting compounds are typically formulated with various filler materials to enhance their physical, thermal, and electrical properties. These filler materials significantly impact the overall performance of the encapsulant, including its flame retardancy characteristics.
Common fillers used in epoxy encapsulants include silica (SiO2), alumina (Al2O3), calcium carbonate (CaCO3), and different types of glass fibers. Each filler has unique properties that can influence the performance of the epoxy encapsulant.
For instance, silica fillers can improve the thermal stability and mechanical properties of the encapsulant while also contributing to flame retardancy. Alumina fillers enhance the electrical insulation properties and thermal conductivity. Calcium carbonate fillers are often used to improve cost-effectiveness, while glass fibers can increase the mechanical strength and dimensional stability of the encapsulant.
Selecting the right filler type and its concentration in the epoxy encapsulant can greatly affect the material’s flame retardancy performance. Some fillers inherently possess flame retardant properties, while others may need specific flame retardant additives to achieve the desired level of fire resistance. Understanding the relationship between the filler type and flame retardancy characteristics is essential in optimizing the performance of epoxy encapsulant potting compounds.
Evaluation of Flame Retardancy Performance
The experimental evaluation of flame retardancy performance in epoxy encapsulant potting compounds showed noticeable differences among various filler types. The results from the UL 94 vertical burning test, a recognized standard for assessing material flammability, clearly demonstrated how filler selection impacts flame retardancy.
Samples with silica and alumina fillers reached the highest levels of flame retardancy, consistently achieving the UL 94 V-0 rating—the most rigorous classification for flame retardancy. These materials effectively prevented the ignition and spread of flames, acting as a strong barrier against fire hazards.
Conversely, epoxy encapsulants that included calcium carbonate and glass fiber fillers showed lower flame retardancy performance; some even failed to meet the UL 94 V-0 standards. The test results indicated that while these fillers provide other benefits, they don’t naturally offer the same level of flame retardancy as silica and alumina.
Influence of Filler Type on Thermal Stability
Alongside flame retardancy performance, the study also explored how different filler types affect the thermal stability of epoxy encapsulant potting compounds. Thermal stability is vital as it determines how well the encapsulant can handle high temperatures and maintain its structure over an electronic device’s lifetime.
Thermal stability assessment involved tests like thermogravimetric analysis (TGA) and differential scanning calorimetry (DSC). These methods helped analyze the materials’ thermal degradation behaviors and the impact of various fillers.
The analysis showed that encapsulants with silica and alumina fillers had superior thermal stability compared to those with calcium carbonate and glass fiber. Silica and alumina enhanced the thermal resistance of the epoxy resin, delaying degradation and improving the encapsulant’s overall thermal stability.
Comparative Analysis of Mechanical Properties
Choosing the right epoxy encapsulant potting compound for electronic devices involves balancing various performance characteristics, including flame retardancy, thermal stability, and mechanical properties. The mechanical properties—tensile strength, impact resistance, and flexural modulus—are crucial for the integrity and reliability of the electronic assembly.
Testing the mechanical properties of the epoxy encapsulant samples showed that the type of filler significantly affects performance. Encapsulants filled with silica and glass fibers had better mechanical properties, showing higher tensile strength, impact resistance, and flexural modulus compared to those with calcium carbonate and alumina fillers.
The superior mechanical performance of silica and glass fiber-filled encapsulants is due to the reinforcing effect of these fillers. They help distribute stresses within the epoxy matrix, enhancing the material’s overall mechanical integrity.
Optimization of Filler Composition for Improved Flame Retardancy
The experimental findings we’ve talked about so far have shed light on how different filler types affect the flame retardancy of epoxy encapsulant potting compounds. To kick things up a notch in fire protection, researchers played around with mixing various fillers like silica, alumina, calcium carbonate, and glass fibers to find the ultimate blend.
They mixed and tested different combos to see which mix would bring out the best in flame retardancy while keeping other properties like thermal stability and mechanical strength in check. Turns out, a tag team of silica and alumina fillers hit the jackpot, consistently nailing the UL 94 V-0 rating, the top-tier flame retardancy class.
Digging deeper, they found the magic mix to be 60% silica and 40% alumina. This blend struck a perfect balance, leveraging silica’s flame-blocking prowess and alumina’s knack for boosting thermal stability, resulting in a top-notch epoxy encapsulant.
Conclusion and Future Considerations
In wrapping up, this research has greatly enriched our understanding of how filler types dictate the performance of epoxy encapsulant potting compounds in terms of flame retardancy. These insights equip engineers and manufacturers to make well-informed choices in selecting and fine-tuning these essential materials, enhancing the safety and reliability of electronic devices for the better.
For more about evaluating the impact of filler type on fme retardancy of electronic epoxy encapsulant potting compounds, you can pay a visit to DeepMaterial at https://www.electronicadhesive.com/ for more info.