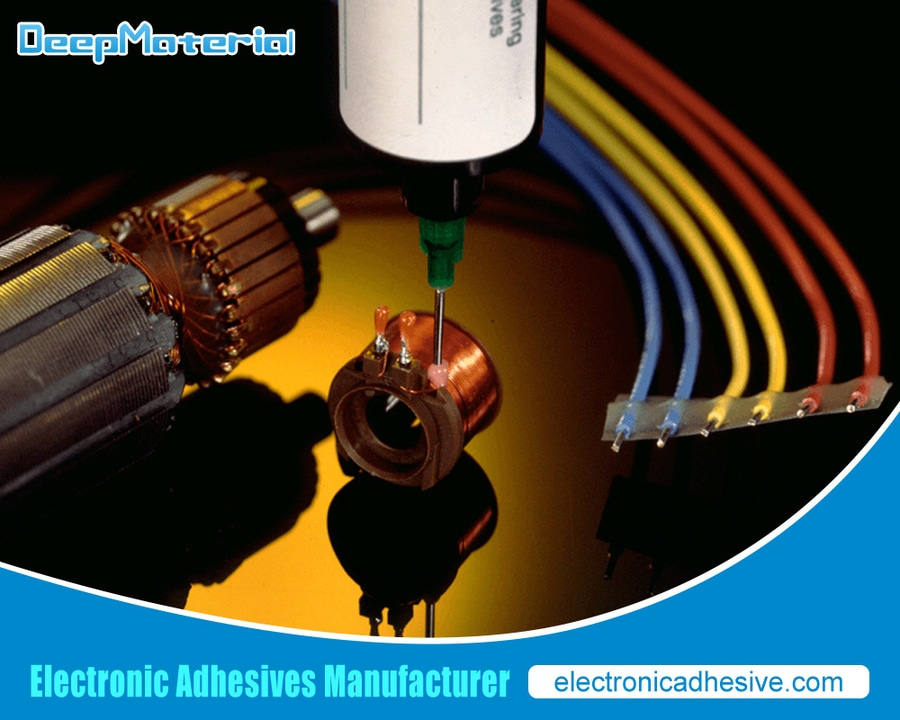
#Industry News
Conformal Coating in the Electronics Market: A Comprehensive Overview
Best Conformal Coating Adhesive Glue Manufacturer
The electronics market has witnessed significant advancements over the past few decades, including the development and widespread adoption of conformal coatings. These specialized coatings protect electronic components from environmental stressors such as moisture, dust, chemicals, and temperature extremes. This article delves into the various aspects of conformal coatings, including their types, applications, benefits, and market trends.
What is Conformal Coating?
Conformal coating is a protective chemical layer applied to printed circuit boards (PCBs) and other electronic components. Its primary purpose is to protect the electronics from external factors that can cause damage or degrade performance over time. Unlike traditional encapsulation methods, conformal coatings are thin and conform to the contours of the PCB, protecting without significantly increasing the size or weight of the component.
Types of Conformal Coatings
There are several types of conformal coatings, each with unique properties and suitable for different applications:
Acrylic Coatings: Known for their ease of application and removal, they provide good humidity resistance and dielectric properties. They are commonly used in environments where rework and repair are frequent.
Silicone Coatings: Silicone coatings offer excellent flexibility and resistance to extreme temperatures, making them ideal for automotive and aerospace applications. They also provide good protection against moisture and chemicals.
Polyurethane Coatings: Polyurethane coatings are known for their toughness and abrasion resistance. They provide excellent protection against chemicals and solvents, making them suitable for harsh industrial environments.
Epoxy Coatings: These coatings offer superior moisture and chemical resistance and are often used in applications where long-term durability is critical. However, they are more challenging to remove compared to other coatings.
Parylene Coatings: Parylene is a unique polymer coating applied via vapor deposition, resulting in an ultra-thin, uniform layer. It offers excellent dielectric properties and protection against moisture and chemicals, but its application process is more complex and costly.
Applications of Conformal Coatings
Conformal coatings are used in a wide range of industries and applications, including:
Consumer Electronics: Conformal coatings benefit smartphones, tablets, and other consumer devices. They protect sensitive components from moisture and dust, enhancing device reliability and longevity.
Automotive Electronics: Modern vehicles rely heavily on electronic systems for engine control, navigation, and safety features. Conformal coatings ensure these systems function reliably under the hood, where they are exposed to heat, vibration, and contaminants.
Aerospace and Defense: The harsh environments encountered in aerospace and military applications require robust protection for electronic systems. Conformal coatings provide resilience against temperature extremes, moisture, and chemical exposure.
Medical Devices: Electronic components in medical devices, such as pacemakers and diagnostic equipment, must remain reliable and contamination-free. Conformal coatings help achieve the high standards required for medical applications.
Industrial Electronics: In manufacturing and processing industries, electronics are often exposed to harsh chemicals, dust, and varying temperatures. Conformal coatings help protect control systems, sensors, and other critical electronics.
Benefits of Conformal Coatings
The adoption of conformal coatings in the electronics market offers several key benefits:
Environmental Protection: Conformal coatings enhance the durability and reliability of electronic devices by shielding components from moisture, dust, and chemical contaminants.
Improved Performance: Conformal coatings help maintain circuits’ electrical performance by preventing corrosion and other forms of environmental damage.
Extended Lifespan: Devices protected with conformal coatings tend to have a longer operational life, reducing the need for repairs and replacements.
Cost Savings: Although the initial application of conformal coatings adds to manufacturing costs, the extended lifespan and improved reliability of coated devices can lead to significant cost savings over time.
Enhanced Safety: In critical applications, such as aerospace and medical devices, the reliability provided by conformal coatings can improve overall safety and performance.
Market Trends and Growth Drivers
The conformal coatings market has experienced significant growth in recent years, driven by several factors:
Increased Demand for Consumer Electronics: The proliferation of smartphones, wearable devices, and other consumer electronics has boosted the demand for reliable and durable components, driving the adoption of conformal coatings.
Advancements in Automotive Technology: The automotive industry’s shift towards electric vehicles and advanced driver-assistance systems (ADAS) has increased the need for robust electronic components, fueling the growth of the conformal coatings market.
Expansion of IoT Applications: The growing Internet of Things (IoT) ecosystem requires durable and reliable electronics to function in diverse environments, further driving the demand for conformal coatings.
Stringent Environmental Regulations: Increasing regulations aimed at improving the reliability and safety of electronic devices, especially in critical applications, have led manufacturers to adopt conformal coatings more widely.
Technological Innovations: Continuous advancements in coating materials and application techniques have improved the performance and cost-effectiveness of conformal coatings, making them more accessible to a broader range of industries.
Challenges and Opportunities
While the conformal coatings market presents significant opportunities, it also faces several challenges:
Application Complexity: Applying conformal coatings, particularly perylene, can require specialized equipment, increasing the initial investment and operational costs.
Material Costs: Some high-performance coatings, such as perylene and certain epoxies, can be expensive, limiting their adoption in cost-sensitive applications.
Repair and Rework: Removing and reapplying conformal coatings for repairs or modifications can be challenging, especially for coatings that are not readily soluble.
Environmental Concerns: Using solvents and chemicals in some coating processes raises ecological and health concerns, prompting the industry to develop more eco-friendly alternatives.
Despite these challenges, the market for conformal coatings continues to grow, driven by ongoing innovations and the increasing need for reliable electronic components. Emerging trends and opportunities include:
Nano-Coatings: Advances in nanotechnology have led to the development of ultra-thin, high-performance coatings that offer enhanced protection without adding significant weight or bulk to electronic components.
Eco-Friendly Coatings: As environmental concerns become more prominent, a growing demand for solvent-free and biodegradable conformal coatings is driving research and development.
Innovative Coatings: Integrating intelligent functionalities, such as self-healing and responsive coatings, represents a promising development area, offering additional layers of protection and performance.
Customization and Flexibility: Manufacturers are increasingly seeking customizable coatings tailored to specific application requirements, providing opportunities for specialized coating solutions.
Conclusion
Conformal coatings have become an integral part of the electronics industry, providing essential protection to various devices and components. The market for these coatings continues to expand, driven by the increasing complexity and miniaturization of electronic devices, technological advancements, and growing environmental awareness. As manufacturers continue to innovate and develop new materials and application techniques, the future of conformal coatings looks promising, with the potential to further enhance electronic components’ reliability, performance, and lifespan across various industries.
For more about choosing the conformal coating in the electronics market: a comprehensive overview, you can pay a visit to DeepMaterial at https://www.electronicadhesive.com/ for more info.