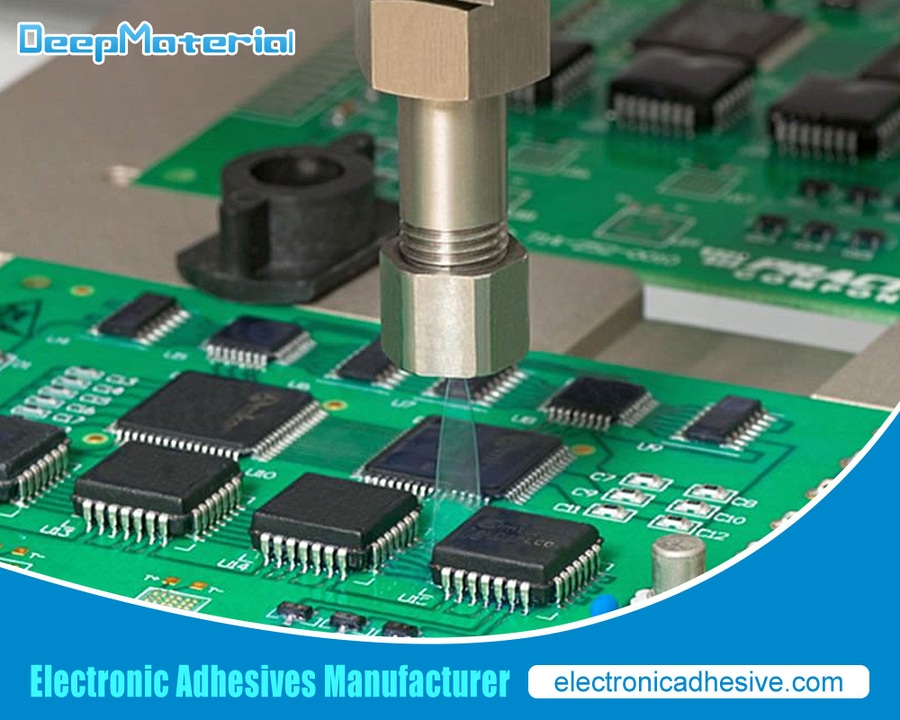
#Industry News
Best Glue for Electronics: A Comprehensive Guide
Best Electronic Adhesive Glue Manufacturer
In electronics, selecting a suitable adhesive is paramount for ensuring the longevity and functionality of electronic components. The choice of glue can significantly impact the performance and durability of electronic devices. This article delves into electronic adhesives, exploring the different types, best practices for their application, and key considerations when selecting the ideal glue for electronic applications.
Understanding Electronics Adhesives
Electronics adhesives come in various types, each with unique properties and applications. Some common types include epoxy, cyanoacrylate (super glue), silicone, and hot melt adhesive. Epoxy is favored for its strength and resistance to heat and chemicals, while cyanoacrylate provides a fast-drying, strong bond. Silicone adhesive offers flexibility and resistance to moisture, and hot melt adhesive is convenient for bonding small electronic components.
Best Practices for Using Electronics Glue
Proper surface preparation is crucial when using glue for electronics. Surfaces should be clean and free of oxidation or corrosion to ensure a strong bond. Different materials require specific preparation techniques; for instance, plastic surfaces may need to be roughened for improved adhesion. Additionally, following the manufacturer’s instructions for glue application is essential to achieve optimal results.
Selecting the Right Glue for Electronics
Several factors must be considered when choosing the best glue for electronics. The key parameters to evaluate are strength, flexibility, temperature resistance, and curing time. Epoxy is known for its excellent stability and versatility, making it suitable for various electronic applications. Although fast-drying and robust, Cyanoacrylate adhesive may not be suitable for all materials. Silicone adhesive offers flexibility and resistance to environmental factors, making it a versatile choice.
Critical Considerations for Electronics Adhesive Selection
When selecting an electronic adhesive, it is crucial to consider the application’s specific requirements. Factors such as operating temperatures, cure times, mechanical stresses, and property changes must be considered. Epoxies are known for their strength and versatility, while urethanes offer flexibility with less resistance to chemicals and high temperatures. Silicones provide good flexibility and resistance to chemicals but come at a higher cost.
Innovations in Electronics Adhesives
The electronics industry is witnessing a shift towards using adhesives for assembly due to their reliability and performance benefits. Adhesives are vital in various electronic components, from bonding magnets to sealing fiber optic cable connections. Recent innovations have led to adhesives offering higher mechanical and thermal properties, gradually replacing traditional soldering systems in electronic assembly.
Pros and Cons of Using Epoxy Glue for Electronics
Due to its unique properties, epoxy glue is a popular choice for bonding electronic components. Here are the pros and cons of using epoxy glue for electronics based on the provided sources:
Pros:
Strong Bond: Epoxy glue is known for its strong bond, making it ideal for applications that require a permanent hold. It can bond to metal, plastic, wood, and ceramic surfaces.
Durability: Epoxy glue can withstand high stress and strain, making it suitable for applications that require longevity and durability.
Versatility: Epoxy glue can be used for various applications, from filling gaps and cracks to creating a waterproof seal.
Resistance to Chemicals: Epoxy glue is resistant to chemicals such as oil, gasoline, and alcohol, making it ideal for automotive and industrial applications.
Cons:
Long Curing Time: Epoxy glue can take several hours to cure completely, which can disadvantage applications requiring a fast bond.
Messy Application: Epoxy glue is thick and sticky, making it messy to apply and challenging to remove from surfaces and skin.
Potentially Harmful: Epoxy glue can contain harmful chemicals like bisphenol A (BPA) and epichlorohydrin, which can be toxic if ingested or inhaled.
Expensive: Epoxy glue can be more costly than other adhesives, especially for applications requiring large amounts of glue.
Common Mistakes To Avoid When Using Epoxy Glue For Electronics
When using epoxy glue for electronics, it is crucial to avoid common mistakes to ensure a successful bond. Based on the provided sources, here are the common mistakes to avoid when using epoxy glue for electronics:
Using Too Much or Too Little Adhesive:
Applying an incorrect amount of epoxy can compromise the bond. Following the manufacturer’s guidelines on the appropriate quantity is essential to achieve a solid and durable bond.
Applying in the Wrong Place or Direction: Incorrect application of epoxy, such as placing it in the wrong location or direction, can lead to ineffective bonding. Ensuring precise application is crucial for a successful bond.
Not Allowing Enough Drying Time: Epoxy glue requires adequate drying time to cure properly and achieve maximum strength. Rushing the process can result in a weak bond that may fail under stress.
Using the Wrong Type of Adhesive:
Selecting the wrong type of epoxy for the specific electronic application can lead to bonding issues. It is essential to choose an epoxy that suits the materials being bonded and the environmental conditions it will be exposed to
When working with electronics, you can ensure a robust and reliable bond by avoiding these common mistakes and following best practices for using epoxy glue, such as proper surface preparation, precise application, and adherence to curing times.
How To Choose The Right Glue For A Specific Material
To choose the suitable glue for a specific material, consider the following guidelines:
Cyanoacrylate (Super Glue):
It is suitable for fast room-temperature curing with low viscosity and is ideal for small clearances like SMT components.
Industrial grades can withstand soldering temperatures.
Epoxy:
It forms rigid, creep-resistant bonds between various materials, such as metals, plastics, and ceramics. It is also electrically insulating and withstands vibrations.
Silicone:
It is excellent for high-temperature electronics bonding, with flexible bonds that tolerate thermal cycling and provide high-voltage insulation. It is also helpful for potting components and coating PCBs.
UV Cure Adhesives:
Effective for glass bonding on displays and optical components, curing quickly with low stress and shrinkage.
Hot Melt Glue:
They are used for temporary holding during PCB assembly when rapid tacking is needed before soldering. They are not suitable for permanent bonds.
When selecting the best glue for electronics, consider the operating temperature range, materials being bonded, strength requirements, temporary vs. permanent usage, and the application method. Each type of glue has specific characteristics that make it suitable for different applications, components, and operating conditions.
In conclusion, while epoxy glue offers a strong bond, durability, versatility, and chemical resistance, its drawbacks include long curing time, messy application, potential health risks, and higher cost. When considering using epoxy glue for electronics, weighing these pros and cons is essential to determine if it is suitable for the specific application.
In conclusion, selecting the best glue for electronics is a critical decision that can impact the performance and longevity of electronic devices. Manufacturers can ensure strong and durable bonds in electronic components by understanding the different types of adhesives, following best practices for application, and considering key factors when choosing an adhesive. This article provides a comprehensive overview of the importance of selecting a suitable glue for electronics and highlights the best practices and considerations for achieving optimal results in electronic applications.
For more about choosing the best glue for electronics: a comprehensive guide, you can pay a visit to DeepMaterial at https://www.electronicadhesive.com/ for more info.