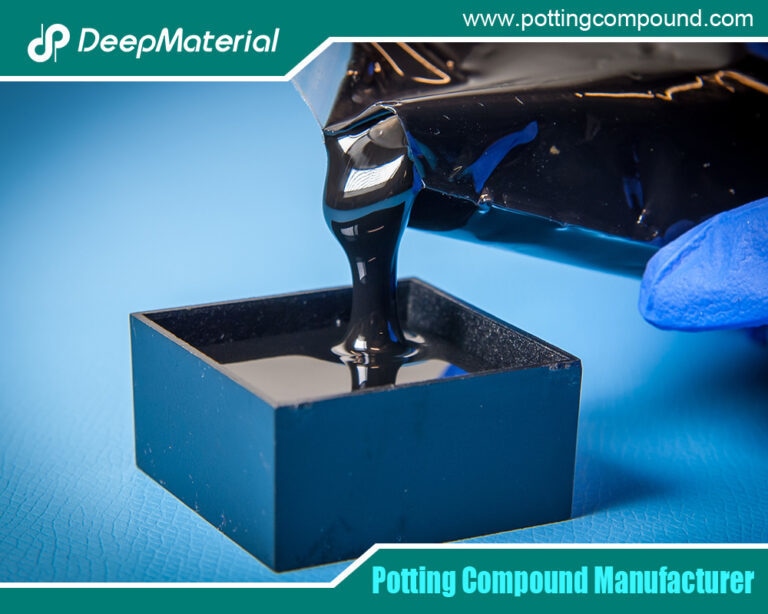
#Industry News
Conformal Coatings for Electronics Applications
Best Conformal Coatings Adhesive Glue for Electronics Manufacturer
As electronic devices’ complexity and functionality have advanced, so too has the need to protect them from various environmental factors. Conformal coatings and thin layers of protective material applied to electronic assemblies provide this essential protection. They offer defense against moisture, dust, chemicals, and temperature extremes, ensuring the reliability and longevity of electronic components. This article explores electronic conformal coatings’ types, applications, benefits, and challenges.
Types of Conformal Coatings
Several types of conformal coatings are commonly used in electronics, each with distinct properties and applications:
Acrylic Coatings (AR)
Properties: Acrylic coatings are easy to apply and remove, providing a clear, glossy finish. They offer good humidity resistance and dielectric strength.
Applications: Used in consumer electronics, automotive electronics, and telecommunications due to their ease of rework and inspection.
Silicone Coatings (SR)
Properties: Silicone coatings are highly flexible, offering excellent thermal stability and moisture resistance. They can withstand wide temperature ranges and have good dielectric properties.
Applications: Ideal for high-temperature environments, such as aerospace, automotive, and industrial electronics.
Urethane Coatings (UR)
Properties: Urethane coatings provide excellent chemical and abrasion resistance. They are also highly resistant to solvents.
Applications: Commonly used in military, aerospace, and automotive applications where chemical exposure is a concern.
Epoxy Coatings (ER)
Properties: Epoxy coatings offer excellent mechanical strength and adhesion. They provide robust protection against moisture and chemicals.
Applications: Suitable for harsh environments in industrial, military, and marine applications.
Paraxylylene Coatings (Parylene)
Properties: Parylene coatings are deposited through a vapor phase process, providing uniform and pinhole-free coverage. They offer superior dielectric properties and chemical resistance.
Applications: Used in medical devices, MEMS, and high-reliability electronics due to their comprehensive protective capabilities.
Applications of Conformal Coatings
Conformal coatings are employed across various industries to protect electronic assemblies from environmental damage. Key applications include:
Consumer Electronics
Devices: Smartphones, tablets, wearable devices, and home appliances.
Purpose: Protection against moisture, dust, and physical damage, enhancing the durability and lifespan of consumer products.
Automotive Electronics
Devices: Engine control units, sensors, infotainment, and battery management systems.
Purpose: Ensuring reliability under harsh conditions, including temperature extremes, Vibration, and exposure to automotive fluids.
Aerospace and Defense
Devices: Avionics, radar systems, and communication equipment.
Purpose: Protecting against extreme temperatures, humidity, and chemical exposure, ensuring the reliability of critical systems.
Medical Electronics
Devices: Implantable devices, diagnostic equipment, and wearable health monitors.
Purpose: Ensuring biocompatibility and protection from bodily fluids, sterilization processes, and other medical environments.
Industrial Electronics
Devices: Control systems, sensors, and power supplies used in manufacturing and processing plants.
Purpose: Protection from chemicals, moisture, and mechanical wear, ensuring the continuous operation of industrial systems.
Benefits of Conformal Coatings
Conformal coatings offer several key benefits that contribute to the reliability and performance of electronic devices:
Environmental Protection
Moisture and Humidity Resistance: Coatings prevent moisture ingress, reducing the risk of corrosion and electrical shorts.
Chemical Resistance: Protection from corrosive chemicals and solvents ensures the longevity of electronic components.
Temperature Stability: Coatings can withstand wide temperature ranges, making them suitable for various operating environments.
Electrical Insulation
Dielectric Properties: Coatings provide excellent electrical insulation, preventing arcing and short circuits in densely packed circuits.
Mechanical Protection
Shock and Vibration Dampening: Coatings help to absorb mechanical stresses, protecting delicate components from damage due to shock and Vibration.
Abrasion Resistance: Coatings provide a barrier against physical wear and tear, extending the life of electronic assemblies.
Enhanced Reliability
Extended Lifespan: By protecting electronic components from environmental damage, conformal coatings help extend the devices’ operational life.
Improved Performance: Reduced risk of failure and enhanced reliability contribute to the overall performance of electronic systems.
Challenges and Considerations
While conformal coatings offer significant benefits, there are also challenges and considerations to be addressed:
Application Process
Uniformity and Coverage: Achieving uniform coverage, especially on complex geometries, can be challenging. Inadequate coverage can leave areas exposed to environmental damage.
Curing Time: Some coatings require specific conditions, such as UV light or heat, affecting production timelines and costs.
Rework and Repair
Difficulty of Removal: Some coatings, such as epoxies, are difficult to remove, complicating rework and repair processes. Acrylic coatings, while easier to remove, may not offer the same level of protection.
Inspection and Testing: Ensuring the coating is applied correctly and effectively requires specialized inspection and testing techniques.
Material Selection
Compatibility: Choosing the suitable coating material for a specific application requires careful consideration of the environmental conditions and compatibility with other materials used in the assembly.
Cost: High-performance coatings, such as perylene, can be expensive, impacting the overall cost of production.
Regulatory Compliance
Environmental and Health Regulations: Coatings must comply with environmental and health regulations, such as RoHS (Restriction of Hazardous Substances) and REACH (Registration, Evaluation, Authorization, and Restriction of Chemicals). This can limit the use of certain materials and affect formulation choices.
Advances in Conformal Coatings
The field of conformal coatings is continuously evolving, driven by the need for more effective and efficient protection solutions. Recent advances include:
Nano-Coatings
Properties: Nano-coatings offer enhanced protection at a molecular level, providing superior barrier properties while maintaining a thin profile.
Applications: Used in applications where traditional coatings may be too thick or heavy, such as in flexible electronics and miniature devices.
UV-Curable Coatings
Properties: These coatings cure rapidly under UV light, reducing production times and energy consumption.
Applications: Ideal for high-throughput manufacturing processes in consumer electronics and automotive industries.
Environmentally Friendly Coatings
Properties: New formulations focus on reducing environmental impact, using less harmful solvents and materials.
Applications: Compliant with stringent environmental regulations, these coatings are used in various industries aiming for sustainable practices.
Smart Coatings
Properties: By incorporating sensors and self-healing capabilities, innovative coatings can provide real-time monitoring and repair for minor damages.
Applications: Used in high-reliability applications such as aerospace and medical devices, where proactive maintenance and extended lifespan are critical.
Conclusion
Conformal coatings play a vital role in protecting and performing electronic assemblies. By offering environmental, electrical, and mechanical protection, these coatings ensure the reliability and longevity of devices across various industries. Despite challenges in application, rework, and material selection, advances in coating technologies continue to improve their effectiveness and sustainability. As the demand for robust and reliable electronics grows, the importance of conformal coatings in safeguarding these systems becomes increasingly paramount.
The future of conformal coatings looks promising, with ongoing research and development focused on enhancing their protective capabilities while addressing environmental and regulatory concerns. By staying at the forefront of these innovations, manufacturers can ensure their products meet the highest standards of quality and reliability, ultimately benefiting consumers and industries worldwide.
For more about choosing the top conformal coatings for electronics applications , you can pay a visit to DeepMaterial at https://www.pottingcompound.com/ for more info.