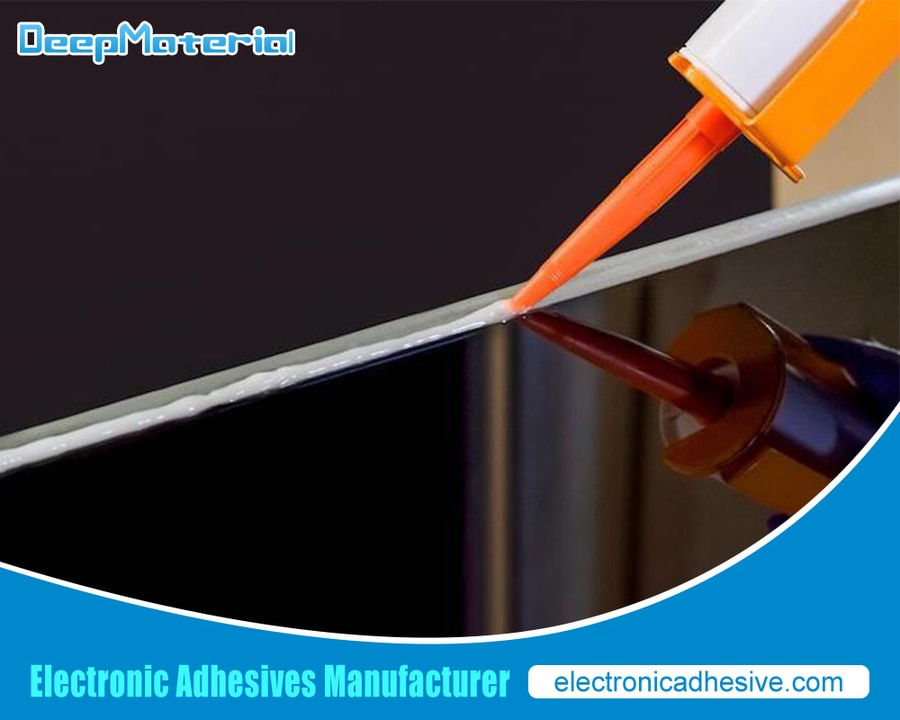
#Industry News
Unlocking the Power of Silicone Potting Compound for Electronics
Best Silicone Potting Compound Adhesive Glue for Electronics Manufacturer
In the intricate world of electronics, where precision and reliability are paramount, the role of encapsulation materials cannot be overstated. Among the diverse available encapsulants, silicone potting compound is a versatile and highly effective option. With its remarkable properties and myriad applications, silicone potting compound has become a cornerstone in electronic manufacturing. This article delves into the nuances of silicone potting compounds, exploring their composition, benefits, applications, and prospects.
Understanding Silicone Potting Compound
The silicone potting compound is a polymer material formulated to encapsulate electronic components, protecting them from environmental factors such as moisture, dust, chemicals, and mechanical stress. Composed primarily of silicone polymers, these compounds are often reinforced with fillers to enhance their mechanical and thermal properties. The resulting material forms a durable, flexible, and chemically inert barrier around sensitive electronic assemblies, safeguarding them from adverse conditions.
Composition and Properties
Silicone potting compounds typically consist of three main components:
Silicone Polymers: Silicone polymers are the backbone of silicone potting compounds. They provide flexibility, thermal stability, and resistance to moisture and chemicals. Silicone polymers are renowned for their high dielectric strength, making them ideal for electrical insulation.
Fillers: Fillers such as silica or alumina are added to reinforce the silicone matrix, improving mechanical properties such as tensile strength, tear resistance, and dimensional stability. Fillers also aid in controlling the coefficient of thermal expansion, reducing the risk of thermal stress on encapsulated components.
Crosslinkers and Catalysts: Crosslinkers and catalysts facilitate the curing process, transforming the liquid silicone mixture into a solid, inert material. These additives determine the potting compound’s cure time, viscosity, and final properties.
The unique combination of these components results in a material with several fundamental properties:
Flexibility: Silicone potting compounds exhibit excellent flexibility, allowing them to conform to the shape of encapsulated components and accommodate mechanical stresses without cracking or delamination.
Thermal Stability: With a broad operating temperature range, silicone potting compounds can withstand extreme heat and cold, making them suitable for applications in harsh environments.
Chemical Inertness: Silicone is inherently resistant to various chemicals, including solvents, acids, and bases, ensuring long-term protection for encapsulated electronics.
Electrical Insulation: Silicone potting compounds possess high dielectric strength and low electrical conductivity, making them ideal for insulating electrical components and preventing short circuits.
Moisture Resistance: Silicones are hydrophobic, repelling water and providing adequate moisture protection for sensitive electronic circuits.
Applications
The versatility of silicone potting compound lends itself to a myriad of applications across various industries:
Electronics Manufacturing: In electronics manufacturing, silicone potting compounds encapsulate multiple components, including printed circuit boards (PCBs), sensors, connectors, and power supplies. By providing reliable protection against environmental hazards, these compounds enhance the durability and longevity of electronic devices.
Automotive Electronics: With the increasing complexity of automotive electronics systems, the demand for robust encapsulation materials has surged. Silicone potting compounds are used extensively in automotive applications, shielding electronic control units (ECUs), sensors, and wiring harnesses from moisture, vibration, and thermal cycling.
LED Lighting: The transition to LED lighting has created a need for encapsulants to withstand the high temperatures generated by LED modules. Silicone potting compounds offer excellent thermal stability and optical clarity, making them ideal for encapsulating LED drivers and modules in indoor and outdoor lighting fixtures.
Renewable Energy: In the renewable energy sector, silicone potting compounds protect electronic components in solar inverters, wind turbines, and battery management systems. These compounds ensure the reliability and efficiency of renewable energy systems, even in harsh outdoor environments.
Medical Devices: Silicone potting compounds are widely employed in the manufacturing of medical devices, where biocompatibility and reliability are paramount. From implantable electronics to diagnostic equipment, silicone encapsulants provide a safe and durable barrier against bodily fluids and sterilization processes.
Consumer Electronics: In consumer electronics, where compactness and reliability are vital, silicone potting compounds offer an effective solution for encapsulating miniature electronic components such as sensors, microcontrollers, and MEMS devices.
Advantages Of Alternative Encapsulation Materials
While various encapsulation materials exist, silicone potting compounds offer several distinct advantages:
Flexibility: Unlike rigid epoxy resins, silicone potting compounds remain flexible even after curing, reducing the risk of stress-induced failures in encapsulated assemblies.
Thermal Stability: Silicones exhibit superior thermal stability compared to organic polymers, allowing them to withstand a wide range of temperatures without compromising performance.
Moisture Resistance: The hydrophobic nature of silicone provides excellent moisture protection, ensuring long-term reliability in humid or wet environments.
Chemical Inertness: Silicone is resistant to many chemicals, including solvents, oils, and acids, making it suitable for applications where exposure to harsh chemicals is a concern.
Dielectric Properties: Silicone potting compounds possess high dielectric strength and low electrical conductivity, making them ideal for insulating electronic components and preventing electrical failures.
Overcoming Challenges
While silicone potting compounds offer numerous benefits, they have challenges. Addressing these challenges is crucial for maximizing the effectiveness of silicone encapsulation in electronic applications:
Adhesion: Ensuring strong adhesion between the silicone potting compound and the substrate is essential for preventing delamination and maintaining long-term reliability. Surface preparation techniques such as cleaning, priming, and plasma treatment can improve adhesion on various substrates.
Curing Time and Process: The curing time of silicone potting compounds can vary depending on temperature, humidity, and catalyst concentration. Optimizing the curing process is critical for achieving consistent results and minimizing production cycle times.
Cost: Silicone potting compounds offer superior performance but may be more expensive than alternative encapsulation materials such as epoxy resins. Balancing performance requirements with cost considerations is essential for optimizing overall manufacturing costs.
Compatibility: Compatibility issues may arise when encapsulating specific components or substrates with silicone potting compounds. To avoid adverse interactions, it is essential to ensure compatibility with sensitive materials such as plastics, elastomers, and adhesives.
Thermal Management: While silicone potting compounds exhibit excellent thermal stability, managing heat dissipation within encapsulated assemblies remains challenging, particularly in high-power applications. Thermal design considerations such as incorporating heat sinks, thermal vias, and conductive fillers can help mitigate thermal issues.
Future Trends and Innovations
As technology continues to evolve, so will the demand for advanced encapsulation materials. In the realm of silicone potting compounds, ongoing research and development efforts aim to enhance further performance and address emerging industry needs:
Advanced Formulations: Researchers are exploring novel silicone formulations with tailored properties, such as improved thermal conductivity, flame resistance, and biocompatibility, to meet the demands of specific applications.
Additive Manufacturing: The advent of additive manufacturing techniques, such as 3D printing, opens up new possibilities for customized encapsulation solutions. Silicone-based 3D printable materials offer flexibility in design and rapid prototyping capabilities.
Green Technologies: With growing environmental awareness, there is a push towards developing eco-friendly silicone formulations derived from renewable sources or recyclable materials, reducing the ecological footprint of electronic manufacturing processes.
Nanotechnology: Integrating nanomaterials into silicone matrices holds promise for enhancing mechanical, thermal, and electrical properties. Nanocomposite silicone potting compounds with improved strength, conductivity, and barrier properties are under investigation.
Brilliant Encapsulation: Smart encapsulation involves incorporating sensors or indicators within the potting material to monitor environmental conditions, detect faults, or provide real-time feedback on the health of encapsulated electronics.
Case Study: Silicone Encapsulation in Automotive Electronics
One industry that extensively utilizes silicone potting compounds is automotive electronics. The modern automobile relies heavily on electronic control units (ECUs) and sensors for various functions, including engine management, safety systems, and infotainment. Ensuring the reliability of these electronics in the harsh automotive environment is paramount to vehicle performance and safety.
Silicone potting compounds are vital in protecting automotive electronics from moisture, vibration, thermal cycling, and exposure to automotive fluids such as oil, fuel, and coolant. By encapsulating ECUs, sensors, and wiring harnesses, silicone potting compounds help extend the lifespan of critical components and reduce the risk of electrical failures.
In addition to environmental protection, silicone potting compounds offer other benefits in automotive applications:
Shock and Vibration Resistance: The flexibility of silicone potting compounds allows them to absorb shock and vibration, minimizing the risk of damage to encapsulated electronics in rugged automotive environments.
Thermal Management: Automotive electronics are subjected to fluctuating temperatures, ranging from extreme heat under the hood to sub-zero conditions in cold climates. Silicone potting compounds provide effective thermal management, dissipating heat generated by electronic components and ensuring optimal performance across a wide temperature range.
Chemical Resistance: Exposure to automotive fluids such as oil, fuel, and coolant can compromise the integrity of electronic assemblies. Silicone potting compounds offer excellent chemical resistance, protecting encapsulated electronics from corrosive fluids and preventing degradation over time.
Conclusion
The silicone potting compound is a cornerstone in electronic encapsulation, offering a unique combination of flexibility, thermal stability, moisture resistance, and chemical inertness. Its versatility, from automotive electronics to medical devices, makes it indispensable in various applications. As research and innovation propel the field forward, silicone potting compounds will continue to play a vital role in safeguarding electronic systems against the rigors of the environment, ensuring reliability and longevity in an ever-changing technological landscape.
As technology advances and new challenges emerge, ongoing research and innovation will drive the development of next-generation silicone potting compounds with enhanced performance and functionality. By addressing key challenges such as adhesion, curing time, and thermal management, silicone encapsulation will remain at the forefront of electronic manufacturing, safeguarding critical components and advancing technology in diverse industries.
For more about unlocking the power of silicone potting compound for electronics, you can pay a visit to DeepMaterial at https://www.electronicadhesive.com/ for more info.