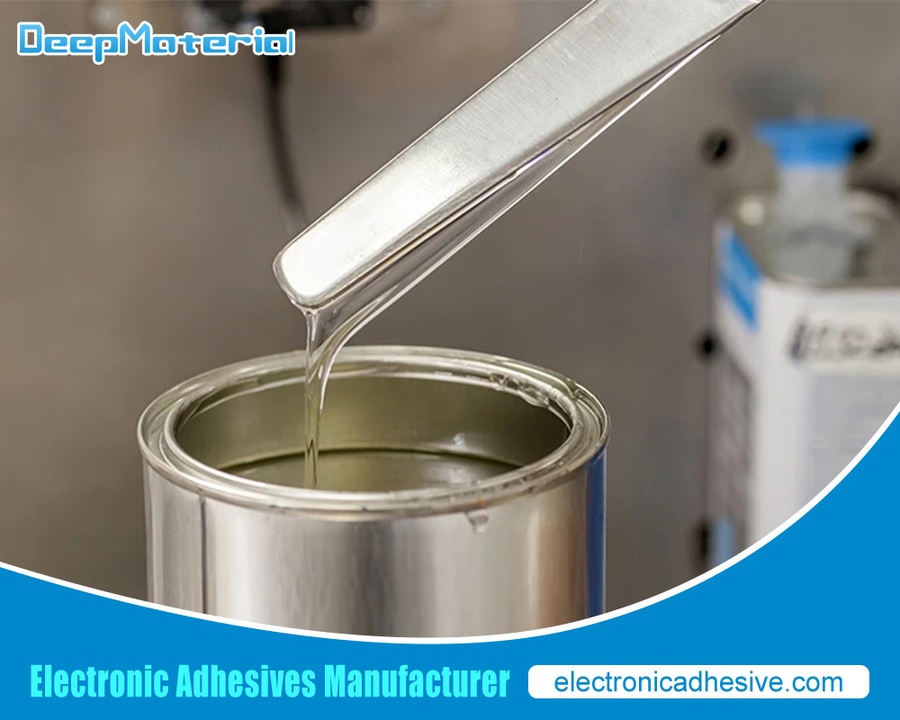
#Industry News
Conformal Coatings for Electronics Applications: Enhancing Durability and Performance
Best Conformal Coatings Adhesive Glue for Electronics Manufacturer
The need to protect these sensitive components from environmental hazards has grown significantly as the world increasingly relies on electronic devices. Conformal coatings are specialized materials applied to electronic assemblies to safeguard them against moisture, dust, chemicals, and temperature extremes. This article delves into the types, applications, benefits, and future trends of conformal coatings in electronics, providing a comprehensive overview of their crucial role in enhancing the durability and performance of electronic devices.
Types of Conformal Coatings
Conformal coatings are categorized based on their chemical composition and curing mechanisms. The primary types include acrylics, polyurethanes, silicones, epoxies, and parylene. Each type offers distinct properties tailored to specific environmental challenges and application requirements.
Acrylic Coatings
Properties:Acrylic coatings are popular due to their ease of application, reworkability, and rapid drying time. They provide excellent moisture and fungus resistance.
Applications:Used in consumer electronics, automotive electronics, and industrial controls where moderate protection is sufficient.
Polyurethane Coatings
Properties:These coatings offer superior chemical and abrasion resistance, making them ideal for harsh environments. They also provide good moisture protection and dielectric properties.
Applications:Commonly used in aerospace, military, and automotive sectors where exposure to solvents and chemicals is prevalent.
Silicone Coatings
Properties:Silicones are known for their exceptional thermal stability and flexibility over a wide temperature range. They offer excellent moisture and corrosion resistance.
Applications:Suitable for high-temperature applications such as engine control units, power supplies, and sensors in automotive and aerospace industries.
Epoxy Coatings
Properties:Epoxy coatings provide a hard, durable finish with excellent chemical and abrasion resistance. They also offer superior adhesion and protection against moisture and contaminants.
Applications:Widely used in industrial electronics and medical devices where robust protection is required.
Parylene Coatings
Properties:Parylene coatings are unique due to their vapor deposition application process, which ensures a uniform, pinhole-free coating. They offer unparalleled barrier properties against moisture, chemicals, and gases.
Applications:Utilized in high-reliability applications such as medical implants, aerospace electronics, and critical military components.
Application Methods
The effectiveness of a conformal coating largely depends on the application method. Standard techniques include brushing, dipping, spraying, and vapor deposition.
Brushing
Advantages:Simple and cost-effective, suitable for small-scale applications or touch-ups.
Limitations:It may result in uneven coating thickness and could be better for complex geometries.
Dipping
Advantages:It provides uniform coating coverage, particularly effective for high-volume production.
Limitations:Potential for material wastage and difficulties in controlling coating thickness.
Spraying
Advantages:Offers reasonable control over coating thickness and is suitable for manual and automated processes.
Limitations:Proper ventilation and masking are required to prevent overspray and contamination.
Vapor Deposition (Parylene)
Advantages:Ensures a conformal, pinhole-free coating with excellent barrier properties.
Limitations:High initial setup cost and longer process time than other methods.
Benefits of Conformal Coatings
Conformal coatings offer several key benefits that contribute to electronic devices’ enhanced performance and longevity.
Moisture Protection
Importance:Moisture can lead to corrosion, electrical shorts, and component failure. Conformal coatings act as a barrier, preventing moisture ingress and enhancing reliability.
Chemical Resistance
Importance:Exposure to harsh chemicals and solvents can degrade electronic components. Coatings protect against chemical attacks, ensuring long-term stability.
Thermal Stability
Importance:Electronic devices often operate in environments with extreme temperatures. Conformal coatings provide thermal insulation, maintaining performance across a wide temperature range.
Mechanical Protection
Importance:Coatings protect against physical damage, such as abrasion and vibration, which can occur during operation and handling.
Electrical Insulation
Importance:Conformal coatings improve dielectric strength, preventing electrical shorts and enhancing the performance of high-voltage circuits.
Applications in Various Industries
The versatility of conformal coatings makes them indispensable across a wide range of industries.
Consumer Electronics
Application:Smartphones, tablets, and wearables are protected from moisture and dust, ensuring durability and reliability.
Example:Acrylic and silicone coatings are commonly used to safeguard components in these devices.
Automotive Electronics
Application:Coatings protect engine control units, sensors, and infotainment systems from harsh conditions such as temperature fluctuations, moisture, and chemicals.
Example:Polyurethane and silicone coatings are favored for their robustness in automotive environments.
Aerospace and Defense
Application:Critical systems such as navigation, communication, and control systems are coated to ensure functionality in extreme conditions.
Example:Parylene and epoxy coatings provide the necessary protection for high-reliability applications.
Medical Devices
Application:Coatings protect sensitive medical electronics, including implants and diagnostic equipment, from bodily fluids and harsh sterilization processes.
Example:Parylene coatings are ideal due to their biocompatibility and excellent barrier properties.
Industrial Electronics
Application:Machinery controls, sensors, and power systems are coated to withstand industrial environments exposed to chemicals, moisture, and mechanical stress.
Example:Epoxy and polyurethane coatings offer the durability required for these applications.
Future Trends and Innovations
The field of conformal coatings continues to evolve, driven by advancements in materials science and the increasing demands of modern electronics.
Nanocoatings
Trend:The development of nanotechnology-based coatings offers enhanced protection with minimal thickness, providing high-performance solutions without compromising device size or weight.
Impact:These coatings can offer superior barrier properties and self-healing capabilities, extending the lifespan of electronic components.
Environmental Sustainability
Trend:Growing emphasis on environmentally friendly coatings that reduce volatile organic compound (VOC) emissions and use sustainable materials.
Impact:Advances in water-based and bio-based coatings contribute to reduced environmental impact and regulatory compliance.
Smart Coatings
Trend:Integrating intelligent functionalities such as self-cleaning, self-healing, and sensing capabilities into conformal coatings.
Impact:These innovations can significantly enhance the maintenance and reliability of electronic systems, particularly in critical applications.
Advanced Application Techniques
Trend:Developing more efficient and precise application methods, such as selective conformal coating using automated robotic systems.
Impact:Improved application precision reduces material waste and increases production efficiency, making high-quality protection more cost-effective.
Customized Solutions
Trend:Tailoring coatings to meet specific application requirements and performance criteria through the formulation of hybrid coatings that combine the strengths of different materials.
Impact:Customized coatings can address unique challenges in emerging technologies, such as flexible electronics and wearable devices.
Conclusion
Conformal coatings protect electronic devices from environmental hazards, enhance their performance, and extend their lifespan. The choice of coating type and application method depends on the specific requirements of the device and its operating environment. As technology advances and the demand for reliable electronics grows, the development of innovative coatings and application techniques will continue to evolve, driving the industry towards more efficient, sustainable, and high-performance solutions.
By understanding the benefits and applications of conformal coatings, manufacturers can make informed decisions to ensure the longevity and reliability of their electronic products. This ultimately contributes to the advancement of technology across various sectors. The future of conformal coatings is promising, with ongoing research and development paving the way for next-generation protective solutions that meet the ever-increasing demands of modern electronics.
For more about conformal coatings for electronics applications: enhancing durability and performance, you can pay a visit to DeepMaterial at https://www.electronicadhesive.com/ for more info.