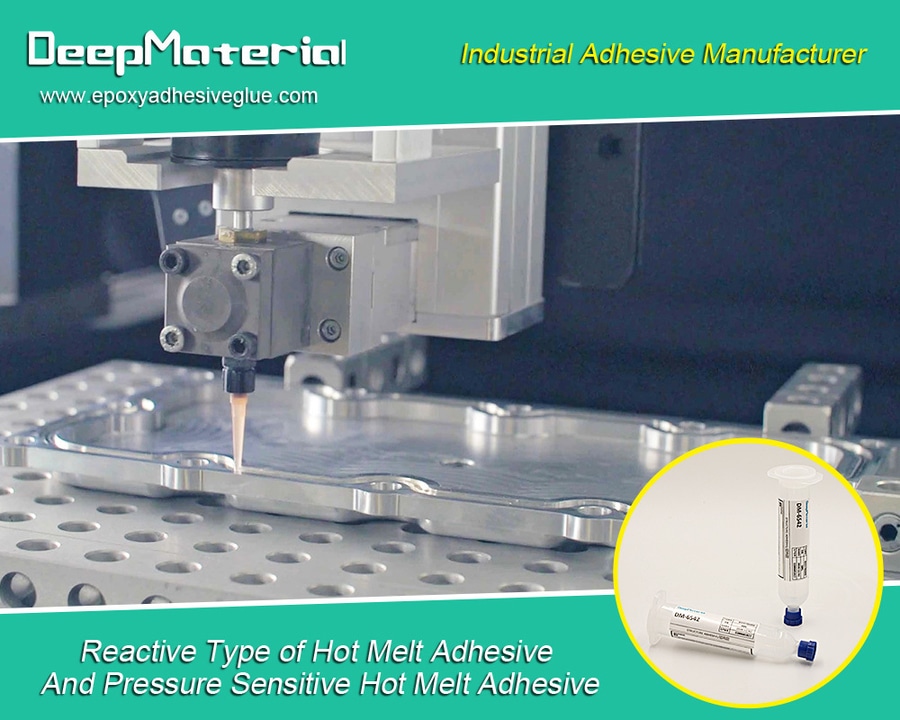
#Industry News
Harnessing Efficiency and Safety: Exploring the Advantages of Epoxy Powder Coating for Electrical Insulation
Best Epoxy Powder Coating Adhesive Glue for Electrical Manufacturer
In electrical engineering and industrial applications, insulation plays a crucial role in ensuring the safety, efficiency, and longevity of electrical components. Epoxy powder coating has emerged as a versatile and reliable solution among the various insulation methods. This article delves into the intricacies of epoxy powder coating for electrical insulation, elucidating its benefits, applications, and the underlying principles that make it an indispensable technique in modern engineering.
Understanding Epoxy Powder Coating:
Epoxy powder coating involves the application of a thermosetting polymer powder onto a substrate, followed by curing to form a durable and protective layer. The process typically consists of three main stages: powder application, melting, and curing. During application, electrostatic attraction is often utilized to ensure uniform coverage and adhesion to the substrate. Subsequently, the coated object is subjected to elevated temperatures to melt the powder, facilitating its flow and formation of a continuous film. Finally, the curing stage involves cross-linking of the epoxy molecules, resulting in a hardened and chemically resistant coating.
Advantages of Epoxy Powder Coating for Electrical Insulation:
Excellent Dielectric Properties: One of the primary reasons for the widespread adoption of epoxy powder coating in electrical insulation is its superior dielectric strength. Epoxy resins inherently possess high dielectric constants, making them effective insulators against electrical currents. This property is essential for preventing short circuits and ensuring the integrity of electrical components, particularly in high-voltage applications.
Corrosion Resistance: Epoxy powder coatings offer exceptional resistance to corrosion, making them ideal for use in harsh and corrosive environments. This attribute enhances the longevity of insulated components, reducing maintenance costs and downtime associated with corrosion-related failures.
Mechanical Durability: The cured epoxy coating forms a tough and resilient barrier that can withstand mechanical stresses such as impact and abrasion. This durability is especially advantageous in industrial settings where electrical equipment may be subjected to rough handling or environmental hazards.
Chemical Resistance: Epoxy resins exhibit remarkable resistance to various chemicals, including acids, alkalis, solvents, and oils. This chemical inertness ensures that the insulation remains unaffected by exposure to corrosive substances, preserving its electrical properties over time.
Versatility: Epoxy powder coating is a versatile technique that can be applied to various substrates, including metals, plastics, and ceramics. This versatility enables its use in diverse applications ranging from electrical enclosures and transformers to circuit boards and motor windings.
Environmental Friendliness: Unlike solvent-based coatings, epoxy powder coatings emit negligible volatile organic compounds (VOCs) during application, contributing to a healthier and safer work environment. Additionally, the absence of solvents reduces the risk of fire hazards and simplifies waste disposal processes.
Applications of Epoxy Powder Coating in Electrical Insulation:
Transformer Components: Epoxy powder coatings are commonly employed to insulate transformer cores, windings, and housings. These coatings provide electrical insulation, thermal conductivity, and mechanical protection, ensuring the reliable performance of transformers in diverse operating conditions.
Electrical Enclosures: Enclosures for electrical panels, switchgear, and control systems are often coated with epoxy powder to enhance insulation and corrosion resistance. This protects sensitive electronic components from environmental contaminants and moisture ingress, prolonging their service life.
Printed Circuit Boards (PCBs): Epoxy powder coatings are utilized in the manufacturing of PCBs to insulate conductive traces and solder joints. The thin yet durable coating prevents electrical short circuits and ensures reliable operation of electronic devices in various industries, including telecommunications, automotive, and consumer electronics.
Motor Windings: Electric motors use insulated windings to generate magnetic fields and facilitate rotation. Epoxy powder coatings provide an effective insulation layer that withstands the thermal and mechanical stresses encountered during motor operation, contributing to the efficiency and longevity of the equipment.
Busbars and Conductors: Busbars, conductors, and terminals in power distribution systems are subjected to high electrical currents and elevated temperatures. Epoxy powder coatings offer reliable insulation and protection against arcing, corona discharge, and environmental factors, enhancing the safety and performance of electrical installations.
Future Trends and Innovations:
The field of epoxy powder coating for electrical insulation continues to evolve with advancements in material science, process optimization, and application techniques. Future trends include the development of nanocomposite coatings with enhanced thermal conductivity and flame-retardant properties. Additionally, innovations in powder formulations and curing methods may further improve the performance and cost-effectiveness of epoxy insulation systems.
Future research in epoxy powder coating for electrical insulation may also address specific industry needs, such as developing coatings tailored for renewable energy applications. With the increasing demand for sustainable energy solutions, there is a growing emphasis on enhancing the efficiency and reliability of solar panels, wind turbines, and energy storage systems. Epoxy coatings that offer improved weatherability, UV resistance, and adhesion to substrates could play a vital role in enhancing the performance and longevity of renewable energy infrastructure.
Moreover, advancements in digitalization and intelligent technologies influence the evolution of epoxy powder coating processes. Innovations such as digital twin simulations, automated powder application systems, and real-time monitoring of curing parameters are enhancing the efficiency, quality, and consistency of coating operations. These digital tools enable manufacturers to optimize coating formulations, reduce waste, and minimize production downtime, enhancing competitiveness and sustainability.
In addition to technological innovations, regulatory requirements and environmental considerations drive the development of eco-friendly epoxy powder coatings. Manufacturers are increasingly focused on reducing the ecological impact of coating processes by exploring alternatives to traditional epoxy resins, such as bio-based or recycled materials. Furthermore, efforts are underway to optimize energy consumption, minimize waste generation, and implement eco-friendly disposal practices throughout the product lifecycle.
Collaboration between academia, industry, and regulatory agencies is essential for advancing the field of epoxy powder coating for electrical insulation. Multidisciplinary research initiatives can facilitate knowledge exchange, foster innovation, and address emerging challenges in material science, surface chemistry, and coating technology. By leveraging collective expertise and resources, stakeholders can accelerate the development and adoption of next-generation insulation solutions that meet the evolving needs of modern society.
Conclusion:
Epoxy powder coating represents a cornerstone in electrical insulation, offering a combination of superior dielectric properties, mechanical durability, and chemical resistance. Its versatility and reliability make it indispensable in various applications, from transformers and electrical enclosures to PCBs and motor windings. As technology advances and new challenges emerge, epoxy powder coating is poised to remain at the forefront of electrical insulation, driving efficiency, safety, and innovation in diverse industries.
For more about harnessing efficiency and safety: exploring the advantages of epoxy powder coating for electrical insulation, you can pay a visit to DeepMaterial at https://www.epoxyadhesiveglue.com/category/epoxy-adhesives-glue/ for more info.