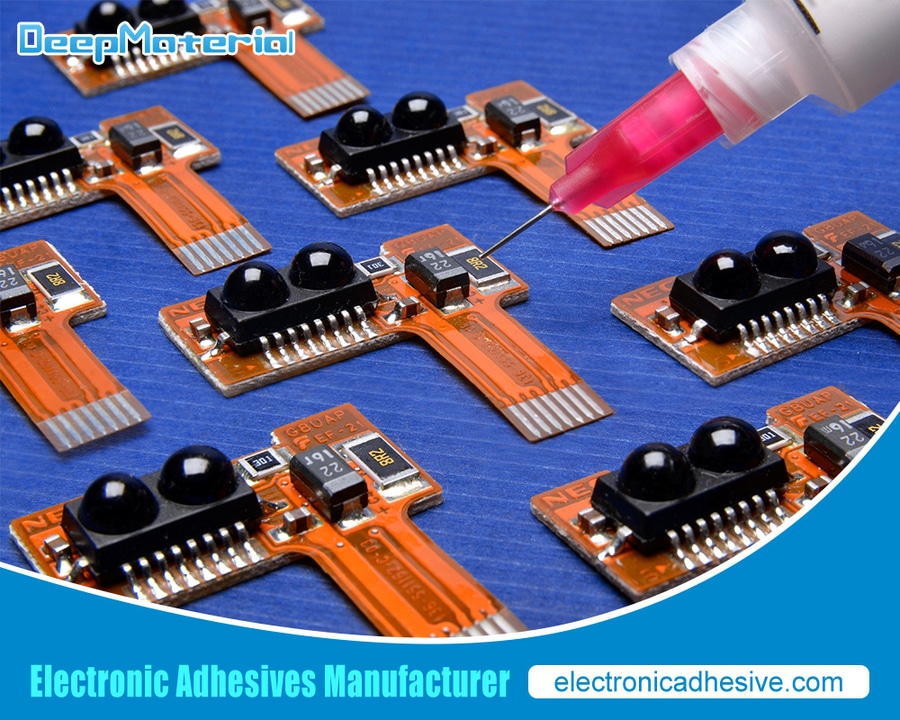
#Industry News
Magnetic Powder Cores Manufacturer: Driving Innovation in Electromagnetic Applications
Best Magnetic Powder Cores Adhesive Glue Manufacturer
Magnetic powder cores are crucial in various electromagnetic applications, ranging from transformers and inductors to advanced power electronics and telecommunications equipment. These cores are valued for their ability to provide efficient magnetic properties while maintaining low energy losses, making them indispensable in modern technology. As the demand for high-performance and energy-efficient electronic devices grows, the role of magnetic powder core manufacturers becomes increasingly significant. This article delves into magnetic powder core manufacturing, exploring the intricacies of production, the importance of material science, and the innovations driving the industry forward.
Understanding Magnetic Powder Cores
Magnetic powder cores are composed of fine magnetic powders, typically made from iron, nickel, cobalt, or their alloys, which are compacted and bonded to form a core. These cores are used to store and transfer magnetic energy in electrical circuits, playing a vital role in ensuring the efficiency and reliability of electronic devices. Their unique properties include high permeability, low coercivity, and minimal energy loss, essential for applications requiring stable and efficient magnetic performance.
Types of Magnetic Powder Cores
Iron Powder Cores: Known for their cost-effectiveness and versatility, iron powder cores are widely used in power electronics, including transformers and inductors. They offer good magnetic properties and can handle high saturation levels.
Sendust Cores: Comprising a mix of iron, silicon, and aluminum, Sendust cores are prized for their low core loss and high permeability. They are ideal for applications requiring minimal energy dissipation and stable performance over a wide frequency range.
MPP (Molybdenum Permalloy Powder) Cores: Featuring a blend of nickel, iron, and molybdenum, MPP cores are known for their superior temperature stability and low core loss. Precision applications commonly use these cores, such as high-quality filters and inductors.
High Flux Cores: Made from nickel and iron, high flux cores offer excellent magnetic properties and high saturation levels, making them suitable for applications demanding high energy storage and minimal core loss.
Amorphous and Nanocrystalline Cores: These advanced cores are produced from amorphous or nanocrystalline materials. They provide exceptional magnetic properties, including high permeability and low core loss. They are increasingly used in high-performance applications like high-frequency transformers and advanced power electronics.
The Manufacturing Process
Producing magnetic powder cores involves several critical steps, each requiring precision and expertise to ensure the final product meets stringent quality standards.
Material Selection
The first step in manufacturing magnetic powder cores is selecting the appropriate magnetic material. The choice of material depends on the intended application and desired properties, such as permeability, saturation magnetization, and core loss. Manufacturers often source high-purity raw materials to ensure consistent quality and performance.
Powder Preparation
Once the raw materials are selected, they are processed into fine powders. This involves mechanical grinding, atomization, or chemical reduction, depending on the type of material. The resulting powders are then sieved to achieve the desired particle size distribution, crucial for attaining uniform magnetic properties in the final core.
Compaction
The prepared powders are then compacted into the desired core shape using high-pressure presses. This process involves placing the powder into a mold and applying pressure to form a dense, cohesive core. The compaction process must be carefully controlled to ensure uniform density and minimize air gaps, adversely affecting the core’s magnetic properties.
Heat Treatment
After compaction, the cores undergo heat treatment to enhance their magnetic properties and mechanical strength. This step typically involves annealing the cores at high temperatures in a controlled atmosphere to relieve internal stresses and promote grain growth. The heat treatment parameters, such as temperature and duration, are carefully optimized to achieve the desired magnetic characteristics.
Coating and Insulation
Magnetic powder cores are often coated with an insulating layer to prevent electrical short circuits and reduce eddy current losses. This can be achieved through various methods, including dip, spray, or electroplating. The choice of coating material depends on the application and required insulation properties.
Testing and Quality Control
The final step in the manufacturing process is rigorous testing and quality control. Each core is subjected to a series of tests to ensure it meets the specified magnetic and mechanical properties. This includes measuring permeability, coercivity, core loss, and saturation magnetization. Only cores that meet the stringent quality standards are accepted or reprocessed.
Innovations in Magnetic Powder Core Manufacturing
The magnetic powder core manufacturing field is continuously evolving, driven by advancements in material science, manufacturing techniques, and application demands. Several vital innovations are shaping the industry, enhancing the performance and versatility of magnetic powder cores.
Advanced Material Development
Research into new magnetic materials is at the forefront of innovation in this industry. Scientists are exploring novel alloys and composites that offer superior magnetic properties and thermal stability. For example, the development of nanocrystalline and amorphous materials has led to cores with exceptionally high permeability and low core loss, making them ideal for high-frequency applications.
Additive Manufacturing
Additive manufacturing, or 3D printing, is revolutionizing the production of magnetic powder cores. This technology allows for creating complex core geometries that were previously impossible to achieve using traditional manufacturing methods. Additive manufacturing also enables precise control over material composition and density, enhancing magnetic performance and reducing waste.
Improved Compaction Techniques
Advancements in compaction techniques are improving the uniformity and density of magnetic powder cores. High-pressure compaction methods, such as isostatic pressing, ensure that the cores have minimal air gaps and consistent magnetic properties. Additionally, using advanced binders and lubricants during compaction reduces friction and wear on the tooling, extending the equipment’s lifespan and improving the cores’ quality.
Enhanced Coating Technologies
Innovations in coating technologies are enhancing the insulation and thermal properties of magnetic powder cores. New coating materials, such as advanced polymers and ceramics, provide superior insulation and thermal stability, reducing eddy current losses and improving overall efficiency. Additionally, advanced coating techniques, such as plasma spraying and chemical vapor deposition, offer precise control over the coating thickness and uniformity.
Applications of Magnetic Powder Cores
Magnetic powder cores find applications in various industries requiring specific magnetic properties and performance characteristics.
Power Electronics
Magnetic powder cores are used in power electronics such as transformers, inductors, and chokes. These components are essential for converting and regulating electrical energy in power supplies, inverters, and motor drives. The high permeability and low core loss of magnetic powder cores ensure efficient energy transfer and minimal heat generation, improving power electronic systems’ overall efficiency and reliability.
Telecommunications
The telecommunications industry relies on magnetic powder cores for signal processing and filtering. These cores are used in filters, baluns, and inductors to ensure precise and reliable signal transmission. Their stable magnetic properties and low core loss are critical for maintaining signal integrity and minimizing interference in high-frequency applications.
Automotive
In the automotive industry, magnetic powder cores are used in electric vehicle (EV) powertrains, charging systems, and advanced driver-assistance systems (ADAS). These cores’ high efficiency and thermal stability are essential for managing the high power levels and thermal loads in EV applications. Additionally, their compact size and lightweight nature contribute to the overall weight reduction and efficiency of automotive systems.
Renewable Energy
Renewable energy systems, such as wind turbines and solar inverters, utilize magnetic powder cores for efficient energy conversion and storage. These cores are used in transformers, inductors, and filters to manage the variable power levels and high frequencies associated with renewable energy sources. The superior magnetic properties and low core loss of magnetic powder cores enhance the efficiency and reliability of renewable energy systems, contributing to a sustainable energy future.
Industrial Automation
Industrial automation systems rely on magnetic powder cores for precise control and energy management. These cores are used in motor drives, power supplies, and control systems to ensure accurate and efficient operation. The high permeability and low core loss of magnetic powder cores enable precise control of electromagnetic fields, improving the performance and reliability of industrial automation systems.
Challenges and Future Trends
While the magnetic powder core industry has made significant strides, several challenges remain. Addressing these challenges will be crucial for its continued growth and advancement.
Material Availability and Cost
The availability and cost of high-purity raw materials are ongoing concerns for manufacturers. The prices of essential materials, such as nickel and cobalt, can be volatile, impacting the overall cost of production. Manufacturers are exploring alternative materials and recycling methods to mitigate these challenges and ensure a stable supply of raw materials.
Environmental Impact
Another critical issue is the environmental impact of magnetic powder core production. The manufacturing process involves energy-intensive steps, such as powder preparation and heat treatment, contributing to greenhouse gas emissions. Additionally, using certain raw materials, such as cobalt, raises ethical sourcing and environmental sustainability concerns. Manufacturers invest in research and development to develop more environmentally friendly production methods and materials.
Miniaturization and Integration
The trend towards miniaturization and integration in electronic devices presents opportunities and challenges for magnetic powder core manufacturers. As devices become smaller and more integrated, there is a growing demand for compact, high-performance magnetic components. Manufacturers are exploring new materials and manufacturing techniques to meet these demands while maintaining or improving performance.
Advancements in Simulation and Modeling
Advancements in simulation and modeling are crucial in developing magnetic powder cores. These tools enable manufacturers to predict the magnetic properties and performance of new materials and core designs, reducing the need for costly and time-consuming physical prototyping. Enhanced simulation and modeling capabilities are accelerating the development of next-generation magnetic powder cores, driving innovation and improving efficiency.
Conclusion
The magnetic powder core industry is dynamic and evolving, driven by advancements in material science, manufacturing techniques, and application demands. As the demand for high-performance and energy-efficient electronic devices continues to grow, the role of magnetic powder core manufacturers becomes increasingly significant. By embracing innovation and addressing the challenges of material availability, environmental impact, and miniaturization, manufacturers are poised to drive the future of electromagnetic applications.
The continuous development of new materials, manufacturing techniques, and advanced simulation tools will ensure that magnetic powder cores remain at the forefront of technology, enabling the efficient and reliable operation of a wide range of electronic devices. As the industry evolves, magnetic powder core manufacturers will continue to play a critical role in shaping the future of power electronics, telecommunications, automotive, renewable energy, and industrial automation, contributing to a more efficient and sustainable world.
For more about choosing the Top Magnetic Powder Cores Manufacturer: Driving Innovation in Electromagnetic Applications, you can pay a visit to DeepMaterial at https://www.electronicadhesive.com/ for more info.