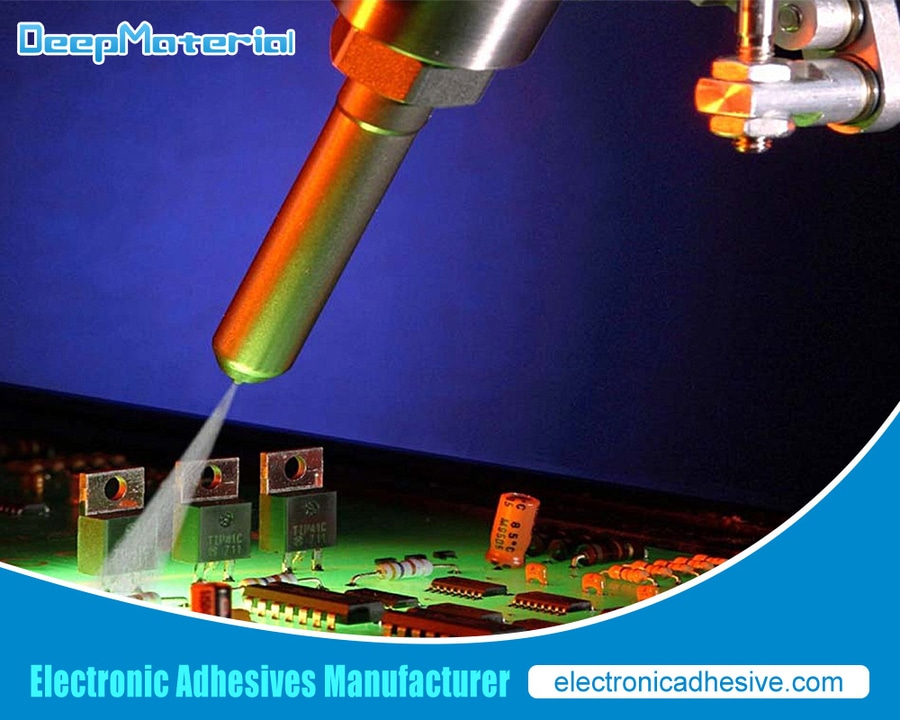
#Industry News
Magnetic Powder Core Material for Inductors: An In-depth Exploration
Best Magnetic Powder Core Material Adhesive Glue Manufacturer
Inductors, often overlooked in electronic components, play a crucial role in managing the flow of electrical energy. The efficiency and performance of these inductors are greatly influenced by the materials used in their cores. Magnetic powder cores have gained significant attention due to their unique properties and advantages. This article explores the intricacies of magnetic powder core materials for inductors, examining their types, properties, applications, and prospects.
What are Magnetic Powder Cores?
Magnetic powder cores, the superheroes of inductor materials, are composite materials made from ferromagnetic powder particles that are insulated and bonded together. These cores are designed to enhance the magnetic properties and performance of inductors, offering a blend of high permeability and low core loss. The powder particles are typically made from iron, silicon steel, permalloy, dust, and ferrites.
Types of Magnetic Powder Core Materials
Iron Powder Cores
Iron powder cores are among the most common types of magnetic powder cores. They are made from pure iron particles and balance cost and performance well. Iron powder cores exhibit high saturation flux density, making them suitable for high-power handling applications.
Silicon Steel Powder Cores
Silicon steel powder cores comprise iron particles with a small percentage of silicon. Adding silicon improves the material’s resistivity, reducing eddy current losses and improving overall efficiency. These cores are widely used in power transformers and inductors operating at lower frequencies.
Permalloy Powder Cores
Permalloy, an alloy of nickel and iron, is known for its high magnetic permeability and low coercivity. Permalloy powder cores, such as audio transformers and magnetic sensors, are crucial in applications with high sensitivity and low signal loss.
Sendust Powder Cores
Sendust is an alloy composed of iron, silicon, and aluminum. Sendust powder cores offer high permeability, low core loss, and excellent temperature stability. These cores are often used in power factor correction circuits and switch-mode power supplies.
Ferrite Powder Cores
Ferrites are ceramic compounds consisting of iron oxide combined with other metal oxides. Ferrite powder cores are characterized by their high electrical resistivity and low eddy current losses. They are suitable for high-frequency applications, such as RF transformers and inductors.
Properties of Magnetic Powder Core Materials
Permeability
Permeability measures how easily a material can support forming a magnetic field. Magnetic powder cores typically have high permeability, which allows for efficient magnetic flux linkage and better inductance for a given number of turns in a coil.
Saturation Flux Density
Saturation flux density indicates the maximum magnetic field that a core material can handle before becoming magnetically saturated. High saturation flux density is desirable in applications where inductors are subjected to high currents, as it prevents core saturation and ensures consistent performance.
Core Loss
Core loss, consisting of hysteresis and eddy current losses, is a critical factor in determining an inductor’s efficiency. Magnetic powder cores are designed to minimize these losses, especially at high frequencies. Hysteresis loss is reduced using materials with low coercivity, while eddy current loss is minimized by ensuring high resistivity through insulation between powder particles.
Temperature Stability
Temperature stability refers to the ability of a core material to maintain its magnetic properties across a range of temperatures. Magnetic powder cores with good temperature stability ensure reliable performance in varying environmental conditions, essential for industrial and automotive applications.
Mechanical Strength
The mechanical strength of magnetic powder cores is vital for their durability and reliability, especially in high-stress environments. The bonding agents used in these cores provide structural integrity, ensuring they can withstand mechanical shocks and vibrations.
Applications of Magnetic Powder Core Materials
Power Inductors
Power inductors store energy and filter signals in power supplies, converters, and inverters. Magnetic powder cores are ideal for power inductors due to their high permeability and low core loss, which enhance energy efficiency and performance in these applications.
RF Inductors
RF inductors are crucial in radio-frequency applications, such as communication devices and signal processing. Ferrite powder cores are particularly suitable for RF inductors because of their high resistivity and low eddy current losses at high frequencies.
Transformers
Transformers rely on magnetic cores to efficiently transfer energy between windings. Magnetic powder cores, such as those made from permalloy or silicon steel, offer high magnetic permeability and low losses, making them excellent choices for various transformers, including power, isolation, and audio transformers.
Chokes
Chokes are inductors that block high-frequency AC signals while allowing DC or low-frequency signals to pass. Sendust and iron powder cores are commonly used in chokes because they can handle high currents without saturation and have low core loss properties.
Magnetic Sensors
Magnetic sensors detect changes in magnetic fields and are used in various applications, including automotive systems and industrial controls. Due to their high sensitivity and low signal distortion, permalloy powder cores are preferred in magnetic sensors.
Advantages of Magnetic Powder Core Materials
High Efficiency
The high permeability and low core loss characteristics of magnetic powder cores contribute to the overall efficiency of inductors. This efficiency is crucial in applications where energy conservation and thermal management are priorities.
Wide Frequency Range
Magnetic powder cores can operate efficiently over a broad frequency range, from low frequencies in power inductors to high frequencies in RF applications. This versatility makes them suitable for a wide array of applications.
Customizable Properties
Altering the composition and size of the powder particles and the bonding materials can tailor the properties of magnetic powder cores. This customization allows for optimizing core materials to meet specific application requirements.
Cost-Effectiveness
Magnetic powder cores can offer a cost-effective solution with comparable or superior performance compared to other magnetic core materials, such as solid ferrites or laminated silicon steel. This is particularly beneficial in high-volume manufacturing.
Reduced Electromagnetic Interference (EMI)
Magnetic powder cores can help mitigate electromagnetic interference by providing effective magnetic shielding. This is important in applications where minimizing EMI is critical, such as communication and computing devices.
Challenges and Limitations
Material Degradation
Over time, magnetic powder cores can degrade due to environmental factors, such as humidity and temperature fluctuations. This degradation can impact their performance and longevity, necessitating protective coatings or encapsulation.
Manufacturing Complexity
The manufacturing process of magnetic powder cores involves precise control over particle size, distribution, and bonding. This complexity can make maintaining consistent quality and performance across different production batches challenging.
Limited High-Temperature Performance
While magnetic powder cores offer good temperature stability, their performance can degrade at very high temperatures. This limitation must be considered in applications involving extreme thermal conditions.
Innovations and Future Trends
Advanced Material Compositions
Ongoing research in material science is leading to the development of advanced magnetic powder core compositions. New alloys and composite materials are being explored to enhance these cores’ magnetic properties, efficiency, and temperature stability further.
Nanocrystalline and Amorphous Powder Cores
Nanocrystalline and amorphous magnetic powders are emerging as promising materials for high-performance inductors. These materials offer shallow core losses and high permeability, making them suitable for demanding applications in power electronics and renewable energy systems.
Improved Manufacturing Techniques
Advancements in manufacturing techniques, such as additive manufacturing and precision casting, enable more precise control over the microstructure of magnetic powder cores. These techniques are expected to improve the cores’ performance consistency and reliability.
Integration with Other Components
The trend towards miniaturization and integration in electronics is driving the development of integrated magnetic components. Magnetic powder cores are integrated with other electronic components to create compact, multifunctional modules that save space and enhance performance.
Sustainable Materials
A growing emphasis is on developing sustainable and environmentally friendly magnetic powder core materials. Researchers are exploring using recyclable and biodegradable materials to reduce the environmental impact of electronic components.
Conclusion
Magnetic powder core materials have revolutionized the design and performance of inductors in modern electronic systems. Their unique properties, including high permeability, low core loss, and customizable characteristics, make them indispensable in various applications, from power electronics to communication systems. Despite challenges such as material degradation and manufacturing complexity, ongoing innovations in material science and manufacturing techniques hold promise for further enhancing the capabilities and applications of magnetic powder cores. As technology advances, magnetic powder core materials are poised to play an increasingly critical role in developing efficient, high-performance electronic components.
For more about choosing the Top Magnetic Powder Core Material for Inductors: An In-depth Exploration, you can pay a visit to DeepMaterial at https://www.electronicadhesive.com/ for more info.