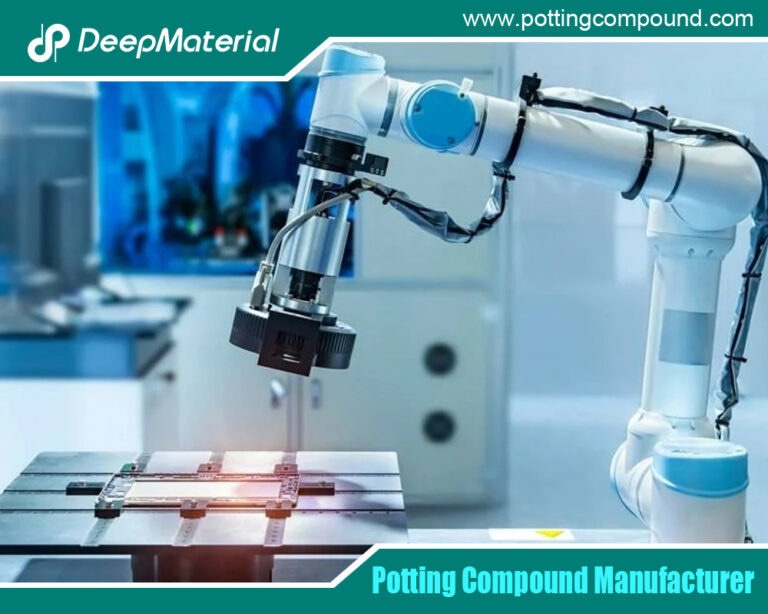
#Industry News
The Electronic Potting Process: A Comprehensive Guide
Best Electronic Potting Adhesive Glue Manufacturer
Electronic potting is a critical process in the electronics manufacturing industry, designed to protect and insulate electronic components from environmental factors and mechanical damage. This method involves encasing electronic assemblies in a protective material, typically a resin, to safeguard them against moisture, dust, chemicals, and physical shock. The primary objective of potting is to enhance the durability, reliability, and longevity of electronic devices, making them suitable for various applications, including automotive, aerospace, marine, and consumer electronics.
In this comprehensive guide, we will explore the electronic potting process, its significance, materials used, methods, benefits, and challenges. We will also discuss advancements in potting technology and its future prospects.
The Significance of Electronic Potting
Protection and Insulation
One primary reason for potting electronic components is to provide protection and insulation. Electronic devices are often exposed to harsh environments where moisture, dust, and chemicals can damage them and affect their performance. Potting creates a sealed barrier around the components, preventing the ingress of contaminants and protecting sensitive parts from corrosion and short circuits.
Mechanical Stability
Potting materials add mechanical stability to electronic assemblies by filling voids and reinforcing the structure. This helps prevent damage from vibrations, shocks, and impacts, which are common in applications such as automotive and aerospace industries. By reducing the risk of mechanical failure, potting enhances the device’s overall reliability.
Thermal Management
Electronic components generate heat during operation, and effective thermal management is crucial to maintain optimal performance and prevent overheating. Potting materials with good thermal conductivity can dissipate heat away from critical components, ensuring they operate within safe temperature limits. This is particularly important for high-power devices and applications where heat dissipation is a concern.
Electrical Insulation
Potting materials provide excellent electrical insulation, preventing short circuits and ensuring the safe operation of electronic devices. This is especially important in high-voltage applications where electrical isolation is critical. By encapsulating the components in an insulating material, potting minimises the risk of electrical failures and enhances the device’s safety.
Materials Used in Electronic Potting
Epoxy Resins
Epoxy resins are among the most commonly used potting materials due to their excellent adhesion, chemical resistance, and mechanical strength. They offer high protection against moisture, dust, and chemicals, making them suitable for various applications. Epoxy resins can be formulated to provide specific properties, such as low viscosity for easy application or high thermal conductivity for heat dissipation.
Polyurethane Resins
Polyurethane resins are known for their flexibility, making them ideal for applications where the potting material needs to absorb vibrations and mechanical stress. They provide reasonable protection against moisture and chemicals, and their flexibility makes them suitable for potting components with varying coefficients of thermal expansion. Polyurethane resins are also available in a range of hardness levels, allowing for customization based on the application’s specific requirements.
Silicone Resins
Silicone resins offer excellent thermal stability and electrical insulation properties, making them suitable for high-temperature applications. They are highly flexible and can withstand extremely high and low temperatures without losing their protective properties. Silicone resins are also resistant to UV radiation and weathering, making them ideal for outdoor applications.
Acrylic Resins
Acrylic resins are known for their fast curing times and excellent clarity, making them suitable for applications where optical clarity is essential. They provide reasonable protection against moisture and chemicals and are often used for LED lighting and optical devices in potting applications. Acrylic resins are also available in UV-curable formulations, allowing rapid curing under UV light.
Thermally Conductive Materials
Thermally conductive potting materials are used for applications requiring efficient heat dissipation. These materials are typically formulated with aluminium oxide, boron nitride, or graphite fillers to enhance their thermal conductivity. Thermally conductive potting materials ensure that heat generated by electronic components is effectively transferred away, preventing overheating and improving the device’s overall performance.
The Potting Process
Preparation
The potting process begins with preparing the electronic assembly and the potting material. The assembly is cleaned to remove any contaminants that could affect adhesion, and the potting material is prepared according to the manufacturer’s instructions. This may involve mixing multiple components, degassing to remove trapped air, and adjusting the viscosity for optimal application.
Application
Once the assembly and potting material are prepared, the material is applied to the electronic assembly. This can be done using various methods, including pouring, dispensing, or injecting the material into the assembly. The choice of application method depends on the assembly’s complexity and the potting material’s properties.
Curing
After applying the potting material, it must cure to form a solid, protective barrier around the components. The curing process can vary depending on the type of potting material used. Epoxy and polyurethane resins typically cure at room temperature or with heat application, while silicone resins may require longer curing times or higher temperatures. Acrylic resins can cure rapidly under UV light. Proper curing is essential to ensure the potting material achieves its desired properties and provides adequate protection.
Inspection and Testing
Once the potting material has cured, the assembly is inspected and tested to ensure successful potting. This may involve visual inspection, electrical testing, and environmental testing to verify the integrity and performance of the potting material. Any defects or issues identified during this stage can be addressed before the assembly is implemented.
Benefits of Electronic Potting
Enhanced Durability and Reliability
Potting significantly enhances the durability and reliability of electronic devices by protecting them from environmental factors and mechanical stress. This results in longer service life and reduced risk of failure, making potted devices suitable for demanding applications.
Improved Performance
Potting helps maintain electronic components’ optimal performance by providing effective thermal management and electrical insulation. This is particularly important in high-power and high-voltage applications with critical heat dissipation and electrical isolation.
Customization and Versatility
Potting materials can be customised to provide specific properties, such as flexibility, thermal conductivity, or optical clarity, depending on the application’s requirements. This versatility makes potting suitable for a wide range of industries and applications.
Cost-Effective Protection
While potting adds a step to manufacturing, it is cost-effective to protect electronic assemblies and enhance their performance. The long-term benefits of increased durability, reliability, and performance often outweigh the initial cost of the potting process.
Challenges in Electronic Potting
Material Compatibility
One of the challenges in potting is ensuring compatibility between the potting material and the electronic components. Incompatible materials can result in poor adhesion, incomplete curing, or degradation of the potting material over time. It is essential to select a potting material compatible with the application’s specific components and conditions.
Process Control
Achieving consistent and reliable potting results requires careful process control. Material preparation, application method, and curing conditions must be carefully controlled to ensure the potting material achieves its desired properties. Any deviations in the process can result in defects or suboptimal performance.
Thermal Management
While potting can enhance thermal management, it can also create challenges in some applications. Potting materials with low thermal conductivity can trap heat, leading to overheating of the components. To ensure effective heat dissipation, it is important to select a potting material with appropriate thermal properties and consider the thermal design of the assembly.
Inspection and Testing
Due to the encapsulation of the components, inspecting and testing potted assemblies can be challenging. Visual inspection may be limited, and specialised testing methods may be required to assess the integrity and performance of the potting material. This adds complexity to the quality control process and requires specialised equipment and expertise.
Advancements in Potting Technology
UV-Curable Potting Materials
UV-curable potting materials have gained popularity due to their rapid curing times and excellent optical clarity. These materials cure quickly under UV light, reducing production times and improving throughput. UV-curable potting materials, such as LED lighting and optical devices, are beneficial in applications where fast curing and high transparency are essential.
Thermally Conductive Potting Materials
Advancements in thermally conductive potting materials have improved their performance and reliability in high-power applications. These materials are formulated with advanced fillers that enhance thermal conductivity while maintaining good mechanical and electrical properties. Thermally conductive potting materials, such as power electronics and electric vehicles, are essential for applications where efficient heat dissipation is critical.
Nanotechnology in Potting Materials
Nanotechnology has opened up new possibilities in developing potting materials with enhanced properties. Nanoparticles can be incorporated into potting materials to improve their mechanical strength, thermal conductivity, and electrical insulation. Nanotechnology enables the development of potting materials with unique properties tailored to specific applications, pushing the boundaries of what is possible in electronic potting.
Automation and Process Control
Advancements in automation and process control have improved the consistency and reliability of the potting process. Automated dispensing systems and precision application methods ensure accurate and repeatable application of potting materials, reducing the risk of defects and improving overall quality. Advanced process control systems monitor and adjust process parameters in real time, ensuring optimal curing and performance of the potting material.
Future Prospects of Electronic Potting
Integration with Advanced Manufacturing Technologies
The future of electronic potting lies in its integration with advanced manufacturing technologies such as additive manufacturing (3D printing) and Industry 4.0. Additive manufacturing enables the creation of complex geometries and custom components, and potting materials can be tailored to complement these designs. Industry 4.0 technologies, including IoT and data analytics, provide real-time monitoring and control of the potting process, ensuring optimal performance and efficiency.
Sustainable Potting Materials
As sustainability becomes a priority in the electronics industry, developing environmentally friendly and sustainable potting materials is gaining momentum. Researchers are exploring bio-based resins and recyclable materials that offer the same protective properties as traditional potting materials while reducing environmental impact. Adopting sustainable potting materials aligns with the industry’s goals of reducing waste and minimising the carbon footprint.
Advanced Functionalities
Future potting materials may incorporate advanced functionalities, such as self-healing properties, improved thermal management, and enhanced electrical insulation. Self-healing potting materials can repair minor damages autonomously, extending the lifespan of the potted assemblies. Enhanced thermal management properties ensure efficient heat dissipation, even in high-power applications. These advanced functionalities will further improve the performance and reliability of electronic devices.
Conclusion
The electronic potting process plays a crucial role in protecting and enhancing the performance of electronic assemblies. By protecting environmental factors, mechanical stress, and thermal challenges, potting materials ensure the durability and reliability of electronic devices across various industries. Advancements in potting technology, including UV-curable materials, thermally conductive formulations, and nanotechnology, continue to push the boundaries of what is possible in electronic potting. As the industry moves towards sustainability and advanced manufacturing technologies, the future of electronic potting looks promising, with new materials and processes on the horizon to meet the evolving demands of the electronics industry.
For more about choosing the electronic potting process: a comprehensive guide, you can pay a visit to DeepMaterial at https://www.pottingcompound.com/ for more info.