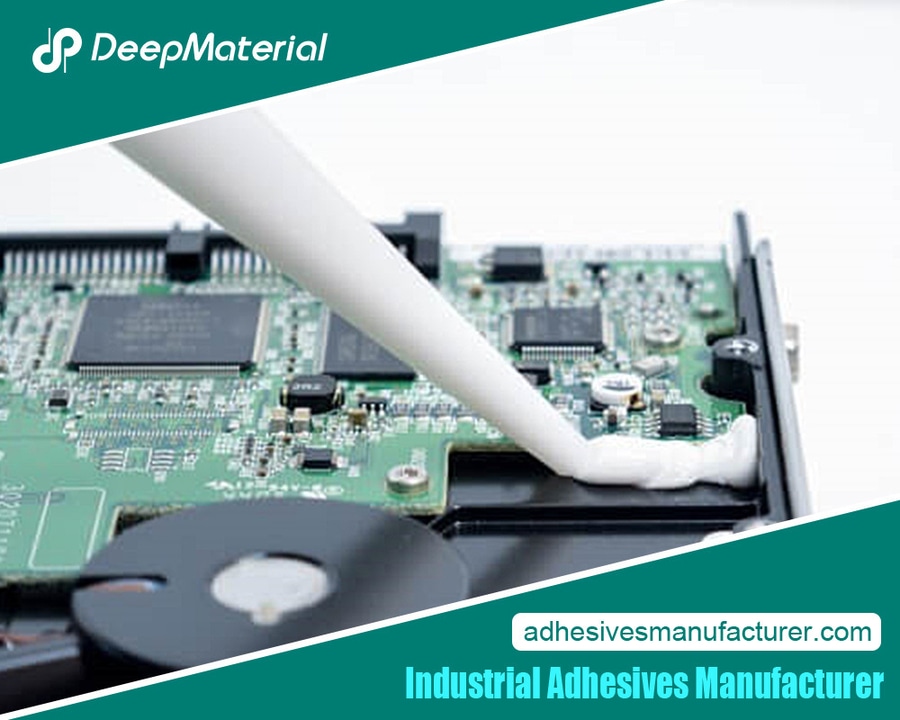
#Industry News
Innovations in Industrial Appliance Adhesive Manufacturing: Pioneering Solutions for Industry Challenges
Best Industrial Adhesive Glue Manufacturer
Industrial appliance adhesive manufacturers play a crucial role in various industries, providing adhesive solutions essential for assembling, bonding, and sealing appliances. In recent years, these manufacturers have been focusing on innovative technologies and sustainable practices to meet the industry’s evolving needs. This article explores the latest industrial appliance adhesive manufacturing trends, challenges, and advancements.
Challenges in Industrial Appliance Adhesive Manufacturing
Adhesives are expected to bond components effectively and withstand the rigors of harsh environments. However, manufacturers need help ensuring these adhesives’ performance, sustainability, and compliance.
Adhesive Performance:
Adhesives used in industrial appliances must meet stringent performance requirements. They are expected to withstand high temperatures, chemical exposure, and mechanical stress. To ensure the longevity and reliability of appliances, manufacturers must develop adhesives that maintain their integrity under such harsh conditions.
Key Points:
Adhesives must be able to bond various materials used in appliance manufacturing, such as metals, plastics, and ceramics.
Resistance to temperature extremes is crucial, as appliances often operate in high-heat or cold environments.
Adhesives must also resist exposure to chemicals commonly found in industrial settings, such as oils, solvents, and cleaning agents.
Environmental Impact:
With increasing concerns about environmental sustainability, manufacturers are under pressure to reduce the environmental footprint of their products, including the adhesives used in industrial appliances. Manufacturers are exploring sustainable materials and processes for adhesive manufacturing to meet these demands.
Key Points:
Sustainable adhesives can be made from renewable or recycled materials, reducing the reliance on non-renewable resources.
Manufacturing processes that reduce energy consumption and emissions are also being adopted to minimize environmental impact.
End-of-life considerations, such as the recyclability or biodegradability of adhesives, are becoming increasingly important in product design.
Regulatory Compliance:
Adhesive manufacturers must navigate a complex regulatory landscape governing the use of chemicals in industrial applications. These regulations are in place to protect human health and the environment. Compliance with these regulations requires manufacturers to select and use chemicals that meet regulatory requirements carefully.
Key Points:
Regulations such as REACH (Registration, Evaluation, Authorization, and Restriction of Chemicals) in the EU and TSCA (Toxic Substances Control Act) in the US govern the use of chemicals in industrial applications.
Adhesive manufacturers must ensure that their products comply with these regulations to avoid penalties and maintain market access.
Compliance with regulatory requirements also contributes to industrial appliances’ overall safety and sustainability.
Latest Trends in Industrial Appliance Adhesive Manufacturing
Several key trends are shaping the industry in the ever-evolving landscape of industrial appliance adhesive manufacturing. From innovative adhesives to bio-based solutions, manufacturers are innovating to meet the demands of modern production processes. Let’s explore the latest trends driving this sector forward.
Smart Adhesives
Manufacturers are developing adhesives with intelligent functionalities, such as self-healing properties and compatibility with sensors for IoT applications.
These adhesives enable appliances to detect and respond to environmental changes, enhancing functionality and durability.
Bio-Based Adhesives
There is a growing trend towards using renewable and biodegradable materials in adhesive formulations to reduce environmental impact.
Bio-based adhesives offer similar or improved performance to traditional adhesives, making them a sustainable choice for manufacturers.
Customized Solutions
Adhesive manufacturers are offering customized solutions to meet the specific needs of appliance manufacturers.
For example, fast-curing adhesives are being developed for high-volume production, improving efficiency and reducing production time.
Digitalization
Digital tools, such as predictive modeling and simulation software, are being used to optimize adhesive formulations and manufacturing processes.
These tools allow manufacturers to test and refine adhesive formulations virtually, saving time and resources for development.
Advancements in Industrial Appliance Adhesive Manufacturing:
Recent advancements in adhesive manufacturing have led to novel adhesive types that cater to specific industrial needs. These innovations, from nano-adhesives to low-VOC options, revolutionize how industrial appliances are assembled and maintained.
Nano-Adhesives:
Superior Bonding Strength: Nano-adhesives leverage nanotechnology to achieve unparalleled bonding strength, ensuring the integrity and longevity of industrial appliance components.
Enhanced Durability: The use of nanoparticles in nano-adhesives enhances their durability, making them resistant to various environmental factors such as heat, moisture, and corrosion.
Ideal for High-Performance Applications:Nano-adhesives are well-suited for high-performance industrial applications where robust bonding is critical for optimal appliance functionality.
Hybrid Adhesives:
Combining Different Technologies: Hybrid adhesives blend the properties of various adhesive types, such as cyanoacrylate and epoxy adhesives, to create a versatile adhesive solution with enhanced bonding performance.
Optimal Bonding Performance:Hybrid adhesives combine the strengths of different adhesive technologies to offer superior bonding performance tailored to the specific requirements of industrial appliance assembly.
UV-Curable Adhesives:
Rapid Curing Times:UV-curable adhesives cure rapidly when exposed to ultraviolet light, significantly reducing assembly time and increasing production efficiency.
High Bond Strength:Despite their fast curing times, UV-curable adhesives exhibit high bond strength, ensuring reliable and durable bonds in industrial appliances.
Suitable for Fast Assembly: The quick curing nature of UV-curable adhesives makes them ideal for applications where fast assembly is essential, minimizing production downtime.
Low-VOC Adhesives:
Environmental Compliance:Adhesive manufacturers increasingly focus on developing adhesives with low volatile organic compound (VOC) emissions to comply with stringent environmental regulations.
Improved Indoor Air Quality:By reducing VOC emissions, low-VOC adhesives contribute to improved indoor air quality in industrial settings, creating a healthier work environment.
Maintaining Bonding Performance:Despite their low VOC content, these adhesives maintain excellent bonding performance, ensuring the integrity of industrial appliance assemblies.
Specialization and Expertise
Understanding the unique needs of different industries and applications is essential for these manufacturers to deliver effective adhesive solutions. Let’s explore the specialized nature of industrial appliance adhesive manufacturers and the importance of their expertise in catering to diverse bonding needs.
Overview of the specialized nature of industrial appliance adhesive manufacturers:
Tailored Solutions:Industrial appliance adhesive manufacturers specialize in developing adhesives that meet the unique requirements of different industries. They understand that a more than one-size-fits-all approach is needed and focus on creating specialized solutions.
Research and Development:These manufacturers invest heavily in research and development to create innovative adhesive formulations. They continuously refine their products to ensure they meet the evolving needs of various industries.
Customization:Industrial appliance adhesive manufacturers offer customization options to meet specific bonding requirements. They work closely with their clients to understand their needs and develop adhesives that effectively address them.
Quality Control:Specialized manufacturers maintain stringent quality control measures to ensure the consistency and reliability of their adhesives. It is crucial, especially in industries where bonding failures can have serious consequences.
Importance of understanding different bonding requirements for various industries and applications:
Industry Specificity:Different industries have different bonding requirements based on the materials and conditions in which they work. Industrial appliance adhesive manufacturers must understand these specific requirements to provide effective solutions.
Application Expertise:Understanding the application process is crucial for ensuring the proper use of adhesives. Manufacturers need to know how their adhesives will be applied and under what conditions to optimize bonding strength.
Durability and Reliability:Adhesives used in industrial applications must be durable and reliable to withstand harsh conditions. Manufacturers with expertise in different industries can develop adhesives that meet these requirements.
Cost-Effectiveness:By understanding the bonding requirements of various industries, manufacturers can develop adhesives that offer the best value for money. It includes considering factors such as the lifespan of the bond and the cost of application.
Conclusion
Industrial appliance adhesive manufacturers are continuously innovating to address the industry’s challnges while meeting the demands for performance, sustainability, and regulatory compliance. By embracing new technologies and sustainable practices, these manufacturers are paving the way for a more efficient and environmentally friendly future in industrial appliance assembly and manufacturing.
For more about the Innovations in industrial appliance adhesive manufacturing: pioneering solutions for industry challenges, you can pay a visit to Deepmaterial at https://www.adhesivesmanufacturer.com/ for more info.