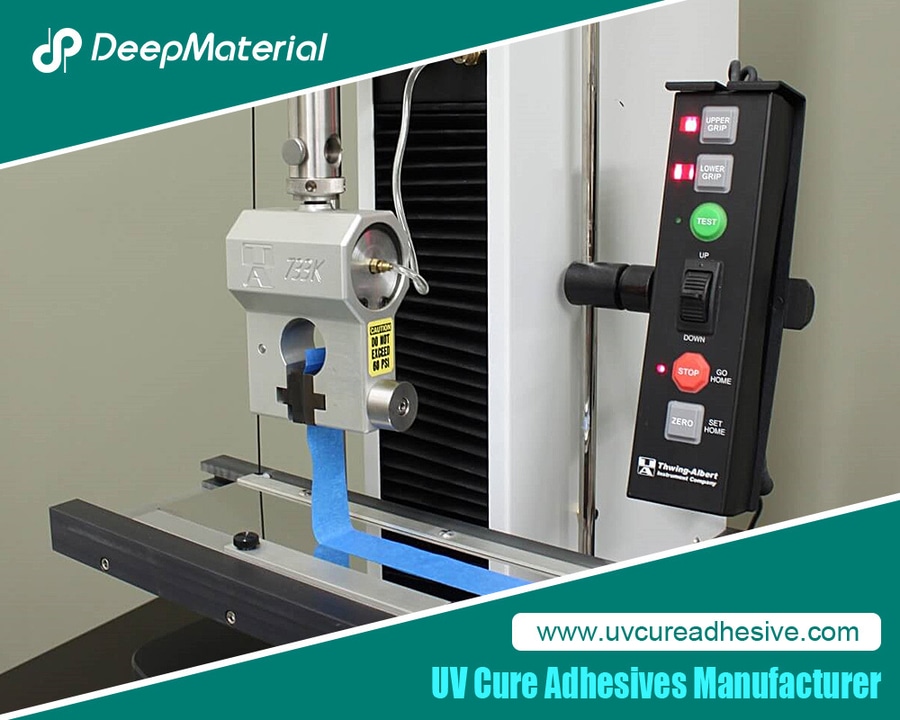
#Industry News
PCB Encapsulation: Protecting Electronic Components for Enhanced Reliability
Best Electronic Adhesive Glue Manufacturer
Printed Circuit Boards (PCBs) are integral components of modern electronic devices, serving as the foundation upon which electronic circuits are built. These boards host a variety of electronic components, including resistors, capacitors, and integrated circuits, interconnected through conductive pathways. Given their critical role, the protection and reliability of PCBs are paramount. One of the essential techniques employed to safeguard these boards is PCB encapsulation.
PCB encapsulation involves enclosing the entire PCB or specific components within a protective material. This material shields the board from environmental factors such as moisture, dust, chemicals, and mechanical stress, enhancing its longevity and performance. This article delves into the various aspects of PCB encapsulation, including its importance, methods, materials, and applications.
Importance of PCB Encapsulation
The encapsulation of PCBs is crucial for several reasons:
Environmental Protection: Electronic devices are often exposed to harsh environmental conditions. Moisture, dust, and corrosive chemicals can lead to short circuits, corrosion, and other forms of damage. Encapsulation creates a barrier that prevents these elements from reaching the sensitive components of the PCB.
Mechanical Stress Resistance: PCBs can be subject to mechanical stress due to vibrations, shocks, and impacts during their operational life. Encapsulation materials provide a cushioning effect, absorbing and distributing these stresses to prevent damage.
Thermal Management: Some encapsulation materials have good thermal conductivity, helping to dissipate heat generated by the components on the PCB. This can be critical in high-power applications where overheating could lead to failure.
Electrical Insulation: Encapsulation ensures that components are electrically insulated from each other, preventing unintended electrical connections that could cause malfunctions.
Chemical Resistance: In industrial or automotive applications, PCBs may be exposed to chemicals such as oils, fuels, and solvents. Encapsulation materials are often chemically inert, protecting against such substances.
Methods of PCB Encapsulation
There are several methods for encapsulating PCBs, each with its advantages and suitable applications:
Conformal Coating:
Description: Conformal coating involves applying a thin, protective film over the surface of the PCB. This coating conforms to the contours of the board and its components.
Materials: Common conformal coating materials include acrylics, polyurethanes, silicones, and epoxies.
Application Methods: Coatings can be applied using methods such as brushing, spraying, dipping, or selective coating.
Advantages: Conformal coatings are lightweight, do not add significant bulk to the PCB, and allow for easy inspection and rework if necessary.
Potting:
Description: Potting involves placing the PCB in a mold or enclosure and then filling it with a liquid encapsulant that hardens over time.
Materials: Epoxies, polyurethanes, and silicones are commonly used for potting.
Application Methods: The liquid encapsulant is poured or injected into the mold, filling all voids.
Advantages: Potting protects against environmental factors, mechanical stress, and tampering.
Encapsulation with Resin:
Description: This method covers the PCB with a resin material similar to potting. The resin is usually applied in a thicker layer than conformal coatings.
Materials: Epoxy resins are commonly used for this purpose.
Application Methods: Resins can be applied manually or using automated dispensing systems.
Advantages: Resin encapsulation offers robust protection and is suitable for harsh environments.
Overmolding:
Description: Overmolding is when the PCB is placed into a mold, and a thermoplastic material is injected around it to form a protective layer.
Materials: Thermoplastics such as polyamide and polyethylene are commonly used.
Application Methods: The process involves injection molding, where the thermoplastic is melted and injected into the mold.
Advantages: Overmolding provides excellent mechanical protection and can be used to create custom shapes and enclosures.
Materials Used in PCB Encapsulation
The choice of encapsulation material depends on the application’s specific requirements, including environmental conditions, mechanical stresses, and electrical properties. Here are some commonly used materials:
Acrylics:
Properties: Acrylic coatings are known for their ease of application, good dielectric properties, and moisture resistance.
Applications: Suitable for applications requiring quick curing and reworkability, such as consumer electronics.
Polyurethanes:
Properties: Polyurethane coatings offer excellent flexibility, abrasion resistance, and protection against moisture and chemicals.
Applications: Commonly used in automotive and industrial electronics where mechanical stress and chemical exposure are concerns.
Silicones:
Properties: Silicone coatings provide high flexibility, thermal stability, and resistance to moisture and chemicals.
Applications: Ideal for high-temperature environments and applications requiring high flexibility, such as aerospace and medical devices.
Epoxies:
Properties: Epoxy encapsulants offer high mechanical strength, excellent adhesion, and resistance to chemicals and moisture.
Applications: Widely used in industrial, automotive, and military applications where robust protection is needed.
Thermoplastics:
Properties: Thermoplastics used in over-molding provide good mechanical protection and can be molded into various shapes.
Applications: Suitable for creating custom enclosures and providing mechanical support in rugged applications.
Applications of PCB Encapsulation
PCB encapsulation is employed across various industries to ensure the reliability and longevity of electronic devices. Some notable applications include:
Consumer Electronics:
Devices: Smartphones, tablets, laptops, and wearable devices.
Encapsulation Benefits: Protects against moisture, dust, and everyday wear and tear, enhancing the durability of these devices.
Automotive:
Components: Engine control units, sensors, infotainment, and battery management systems.
Encapsulation Benefits: Protects against harsh environmental conditions, such as temperature extremes, vibrations, and chemical exposure.
Industrial:
Equipment: Control panels, sensors, and communication devices used in manufacturing and process control.
Encapsulation Benefits: Ensures reliable operation in demanding environments, including exposure to dust, moisture, and chemicals.
Aerospace:
Systems: Avionics, navigation systems, and communication equipment.
Encapsulation Benefits: Offers protection against extreme temperatures, vibrations, and moisture, ensuring the reliability of critical systems.
Medical Devices:
Instruments: Diagnostic equipment, implantable devices, and patient monitoring systems.
Encapsulation Benefits: Provides biocompatibility, chemical resistance, and protection against sterilisation processes.
Telecommunications:
Infrastructure: Network routers, switches, and base stations.
Encapsulation Benefits: Ensures reliable operation in outdoor and indoor environments, protecting against moisture, dust, and temperature variations.
Challenges and Considerations in PCB Encapsulation
While PCB encapsulation offers numerous benefits, it also presents specific challenges and considerations:
Material Selection: Choosing a suitable encapsulation material is critical. The material must meet the application’s requirements, including thermal conductivity, flexibility, and chemical resistance.
Application Process: The method of applying the encapsulation material must be carefully controlled to ensure complete coverage and avoid voids or air bubbles that could compromise protection.
Inspection and Rework: Encapsulated PCBs can be challenging to inspect and rework. Techniques such as X-ray inspection may be required to detect defects, and rework may involve removing and reapplying the encapsulation material.
Thermal Management: While encapsulation can aid in thermal management, it can trap heat if not adequately designed. Ensuring adequate heat dissipation is essential to prevent overheating.
Cost: The cost of materials and the encapsulation process can be significant. It is necessary to balance the benefits of encapsulation with the associated costs to ensure a cost-effective solution.
Future Trends in PCB Encapsulation
As technology advances, the PCB encapsulation field also evolves. Some future trends to watch for include:
Advanced Materials: The development of new encapsulation materials with improved properties, such as higher thermal conductivity, better flexibility, and enhanced chemical resistance, will continue to drive innovation in this field.
Nanotechnology: Using nanomaterials in encapsulation can offer improved performance characteristics, such as enhanced thermal management and mechanical strength.
Brilliant Encapsulation: Incorporating sensors and intelligent materials into encapsulation can enable real-time monitoring of the PCB’s condition, providing valuable data for predictive maintenance and improving reliability.
Environmental Considerations: As sustainability becomes increasingly essential, developing eco-friendly encapsulation materials and processes will be a crucial focus. This includes materials that are biodegradable or recyclable.
Miniaturisation: As electronic devices continue to shrink, encapsulation techniques must adapt to provide adequate protection for smaller and more densely packed PCBs.
Conclusion
PCB encapsulation is vital in the electronics industry, offering protection and reliability for various applications. Encapsulation ensures the longevity and performance of electronic devices by safeguarding PCBs from environmental factors, mechanical stress, and electrical issues. As technology advances and new materials and techniques are developed, the field of PCB encapsulation will continue to evolve, providing even more significant benefits and addressing emerging challenges. PCB encapsulation remains a cornerstone of reliable and durable electronic design, whether in consumer electronics, automotive, industrial, aerospace, medical, or telecommunications applications.
For more about choosing a PCB encapsulation: protecting electronic components for enhanced reliability, you can pay a visit to DeepMaterial at https://www.uvcureadhesive.com/ for more info.