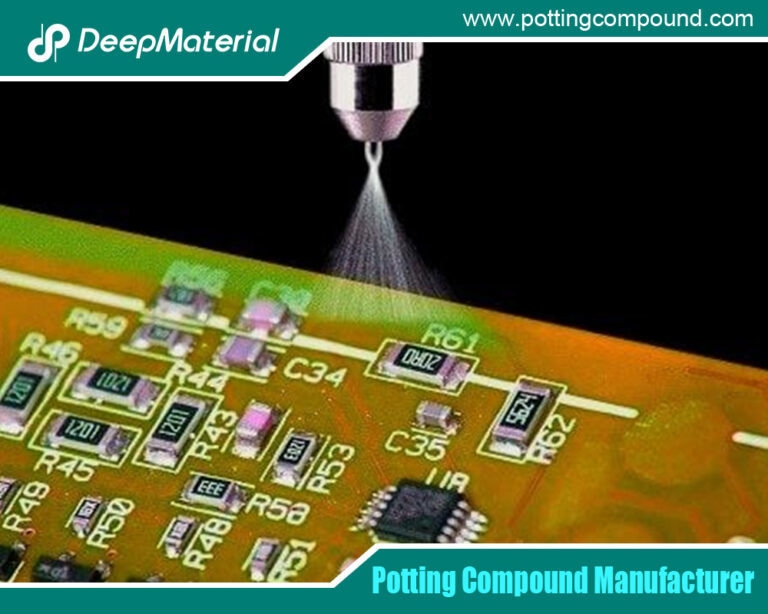
#Industry News
Potting Material for Electronics: An In-Depth Guide
Best Potting Material Adhesive Glue for Electronics Manufacturer
Electronics are at the heart of modern technology, powering everything from household gadgets to industrial machinery. Various protective measures are employed to ensure their longevity and reliability, among which potting is crucial. Potting involves encasing electronic components in a solid or gelatinous compound to protect them from environmental hazards such as moisture, chemicals, and mechanical stress. This article delves into the intricacies of potting materials for electronics, exploring their types, applications, benefits, and selection criteria.
Types of Potting Materials
Potting materials come in various forms, each with specific properties tailored to different applications. The most common types include epoxy resins, polyurethane resins, silicone compounds, and acrylics.
Epoxy Resins:
Properties: Epoxy resins are known for their excellent adhesion, high mechanical strength, and good thermal conductivity. They are also resistant to a wide range of chemicals and environmental conditions.
Applications: Due to their robustness, epoxy resins are widely used in automotive electronics, industrial controls, and consumer electronics where durability is paramount.
Polyurethane Resins:
Properties: Polyurethanes offer flexibility and superior resistance to impact and vibration. They also provide good electrical insulation and are resistant to moisture and chemicals.
Applications: Polyurethanes are ideal for applications that require flexibility and impact resistance, such as wearable electronics, automotive sensors, and marine electronics.
Silicone Compounds:
Properties: Silicone potting materials are prized for their extreme temperature resistance, flexibility, and excellent dielectric properties. They remain stable over a wide temperature range and resist moisture and chemicals.
Applications: Silicones are commonly used in high-temperature environments, such as aerospace electronics, LED lighting, and power supplies.
Acrylics:
Properties: Acrylic potting compounds offer sound clarity, UV stability, and ease of application. They cure quickly and can be used for applications requiring transparency.
Applications: Acrylics are often used in display electronics, LED applications, and situations where visual inspection is necessary.
Applications of Potting Materials
Potting materials serve various applications across various industries, each with unique requirements and challenges.
Automotive Electronics:
Challenges: Automotive electronics face harsh conditions, including temperature extremes, vibrations, and exposure to chemicals and moisture.
Solutions: Potting materials like epoxy and polyurethane resins protect sensors, control units, and connectors, ensuring they function reliably under challenging conditions.
Consumer Electronics:
Challenges: Consumer electronics need protection from everyday wear and tear, including drops, spills, and environmental factors.
Solutions: Potting with materials like silicone and acrylic compounds helps protect circuit boards and delicate components in devices such as smartphones, laptops, and wearable technology.
Industrial Controls:
Challenges: Industrial control systems must withstand exposure to dust, moisture, and varying temperatures in demanding environments.
Solutions: Epoxy and polyurethane potting materials encapsulate control modules, sensors, and other critical components, ensuring they remain operational and safe.
Aerospace and Defense:
Challenges: Aerospace and defence electronics must operate reliably in extreme conditions, including high altitudes, temperature variations, and mechanical stress.
Solutions: Silicone compounds are often used for their stability and performance in extreme environments, protecting avionics, communication systems, and navigation equipment.
Benefits of Potting Materials
Potting materials offer numerous benefits in electronics, enhancing the performance, durability, and safety of electronic devices and systems.
Environmental Protection:
Potting materials shield electronic components from moisture, dust, and corrosive substances, which can otherwise lead to malfunctions and failures.
Mechanical Protection:
Encapsulation provides a barrier against physical impacts, vibrations, and mechanical stress, which is crucial for maintaining the integrity of electronic assemblies in rugged environments.
Thermal Management:
Many potting compounds, especially those with high thermal conductivity, help dissipate heat from sensitive components, preventing overheating and enhancing reliability.
Electrical Insulation:
Potting materials offer excellent dielectric properties, reducing the risk of short circuits and electrical failures, which is vital for the safety and performance of electronic systems.
Chemical Resistance:
Potting compounds protect against chemical exposure, including solvents, oils, and other industrial chemicals, ensuring the longevity of electronic devices.
Improved Aesthetics:
Transparent potting materials, such as acrylics, allow for visual inspection of components and can enhance the overall appearance of electronic products.
Selection Criteria for Potting Materials
Choosing the suitable potting material for a specific application involves considering several factors to ensure optimal performance and protection.
Environmental Conditions:
Evaluate the conditions the electronic device will be exposed to, including temperature extremes, humidity, and chemical exposure. Select a potting material that can withstand these conditions without degrading.
Mechanical Requirements:
Consider the mechanical stresses the device will encounter, such as vibrations, impacts, and thermal expansion. Choose a potting material with appropriate flexibility and mechanical strength.
Thermal Management:
For applications where heat dissipation is critical, select potting compounds with high thermal conductivity to ensure efficient heat transfer away from components.
Electrical Properties:
Ensure the potting material provides adequate electrical insulation to prevent short circuits and electrical failures, especially in high-voltage applications.
Curing Time and Process:
Consider the curing time and process of the potting material. Some applications may require quick curing, while others may benefit from materials with longer working times.
Compatibility with Components:
Verify that the potting material is compatible with the electronic components and substrates it will contact, avoiding any adverse chemical reactions or bonding issues.
Cost and Availability:
Assess the cost-effectiveness of the potting material about the application’s requirements and budget constraints. Ensure the material is readily available for consistent supply.
Future Trends in Potting Materials
As technology advances, the development of potting materials continues to evolve, driven by the need for more efficient, reliable, and environmentally friendly solutions.
Sustainable Potting Materials:
There is a growing trend towards developing potting materials that are environmentally friendly and sustainable. This includes using bio-based resins and reducing the environmental impact of production processes.
Advanced Thermal Management:
With the increasing power density of electronic devices, advanced potting materials with superior thermal management properties are being developed to enhance heat dissipation and maintain optimal operating temperatures.
Enhanced Electrical Properties:
Innovations in potting materials are focused on improving dielectric properties to support the growing complexity and miniaturisation of electronic components, ensuring reliable electrical insulation and performance.
Smart Potting Materials:
Integrating intelligent materials that can adapt to changing conditions or provide additional functionalities, such as self-healing properties or embedded sensors, is an emerging trend in potting materials.
Customizable Formulations:
The demand for customised potting solutions tailored to specific applications drives the development of formulations that can be easily modified to meet unique requirements, offering greater flexibility and performance.
Conclusion
Potting materials safeguard electronic components from environmental hazards, mechanical stress, and electrical failures. By understanding the different types of potting compounds, their applications, benefits, and selection criteria, engineers and manufacturers can make informed decisions to enhance the reliability and durability of electronic devices. As technology continues to evolve, developing innovative and sustainable potting materials will further advance the protection and performance of electronics across various industries.
For more about the potting material for electronics: an in-depth guide, you can pay a visit to DeepMaterial at https://www.pottingcompound.com/ for more info.