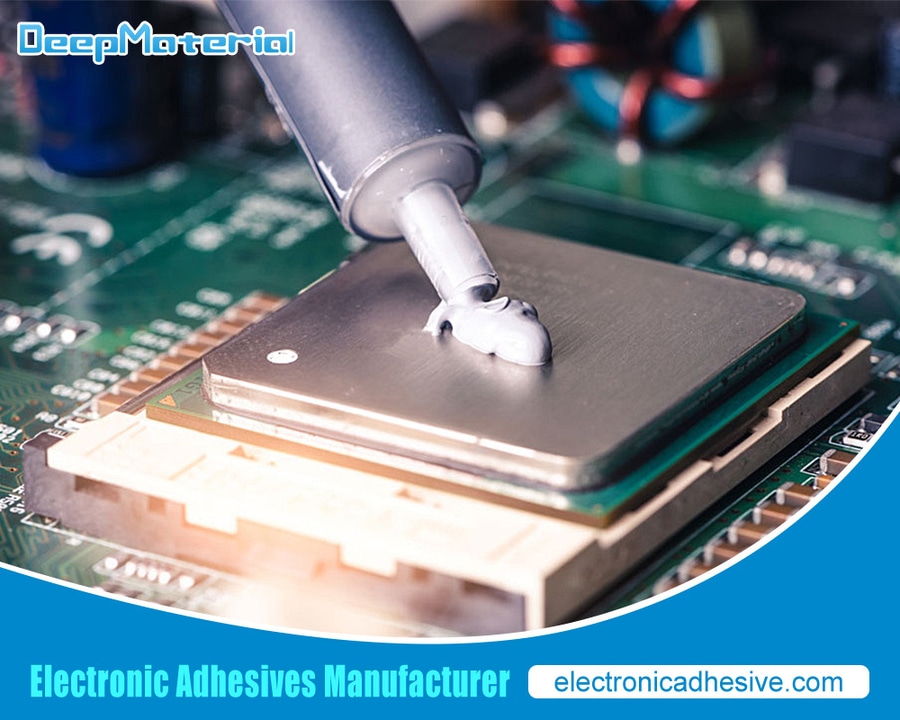
#Industry News
Enhancing Electronic Reliability: The Role of Non Conductive Epoxy
Best Enhancing Electronic Adhesive Glue Manufacturer
Reliability is paramount in electronic manufacturing. Ensuring electronic components remain operational under various conditions requires meticulous attention to detail in assembly and materials. Non conductive epoxy emerges as a vital player in this landscape, offering a blend of insulation, adhesion, and protection. This article delves into the significance of Non conductive epoxy in electronics, exploring its properties, applications, and contributions to the reliability of electronic devices.
Understanding Non Conductive Epoxy
Non conductive epoxy represents a specialized epoxy resin engineered to insulate electronic components while providing strong adhesion properties. Composed of a polymer matrix filled with insulating particles such as ceramics or silica, Non conductive epoxy forms a robust barrier against electrical currents, moisture, and other environmental factors. Its low electrical conductivity ensures that it does not interfere with the performance of sensitive electronic circuits.
Key Features and Benefits
Insulation: Non conductive epoxy creates a protective layer that insulates electronic components, safeguarding them from electrical shorts and other potential damage.
Adhesion: Its strong adhesion properties enable secure bonding between various substrates, including metals, plastics, and ceramics, ensuring stable assembly of electronic devices.
Chemical Resistance: Resistant to a wide range of chemicals, Non conductive epoxy provides long-term protection against corrosive substances, enhancing the durability of electronic assemblies.
Thermal Stability: With excellent thermal stability, it withstands fluctuations in temperature, maintaining its insulating properties even in harsh operating environments.
Versatility:Non conductive epoxy is suitable for diverse applications, including encapsulation, potting, bonding, and sealing in industries ranging from automotive and aerospace to telecommunications and consumer electronics.
Applications
Non conductive epoxy finds extensive use in various electronic applications, including:
Printed Circuit Boards (PCBs): These encapsulate and potts electronic components on PCBs, offering insulation and mechanical support.
Semiconductors: Non conductive epoxy encapsulates delicate semiconductor devices, protecting against moisture and mechanical stress.
Sensors and Instrumentation: It is employed for bonding and sealing sensors and instrumentation devices, ensuring reliable performance in challenging conditions.
LED Lighting:Non conductive epoxy is utilized in LED encapsulation to enhance thermal management and protect LED components from environmental factors.
Selection Considerations:
When choosing Non conductive epoxy for electronic applications, several factors should be considered:
Electrical Properties:Verify the epoxy’s electrical insulation capabilities and dielectric strength to ensure compatibility with specific electronic requirements.
Thermal Conductivity: Assess the epoxy’s thermal conductivity to prevent overheating of enclosed components, especially in high-power applications.
Chemical Compatibility:Confirm compatibility with surrounding materials and environmental conditions to prevent degradation or failure over time.
Cure Time and Process: Consider the curing mechanism and processing requirements to optimize production efficiency and product performance.
Regulatory Compliance: Ensure the chosen epoxy complies with relevant industry standards and regulations governing electronic materials and components.
Applications in Electronics Manufacturing
Non conductive epoxy for electronics is a game-changer in modern electronics manufacturing, offering a myriad of benefits across different stages of production. Here’s how it revolutionizes the industry:
Versatile Bonding Agent:
In PCB assembly, Non conductive epoxy is a reliable bonding agent for surface mount components.
It ensures the secure placement of components while providing essential electrical insulation, preventing short circuits, and ensuring optimal performance.
Protective Encapsulation:
Sensitive electronic components like integrated circuits and sensors require robust protection.
Non conductive epoxy acts as a protective barrier, shielding these components from mechanical stress and environmental contaminants, ensuring longevity and reliability.
Thermal Stability:
Heat management is crucial in electronics manufacturing to prevent overheating and ensure optimal performance.
Non conductive epoxy’s thermal stability makes it ideal for potting applications. In these applications, it effectively dissipates heat generated by electronic components, maintaining their efficiency and prolonging their lifespan.
Enhanced Durability:
Electronics face various environmental challenges, from temperature fluctuations to moisture exposure.
Non conductive epoxy enhances durability by providing a resilient barrier against moisture ingress, corrosion, and other environmental factors, ensuring the longevity of electronic devices.
Streamlined Production Processes:
The ease of application and curing properties of Non conductive epoxy streamline manufacturing processes, reducing production time and costs.
Its compatibility with automated dispensing systems further enhances efficiency, allowing for precise application even in high-volume production environments.
Enhancing Reliability
The utilization of Non conductive epoxy significantly enhances the reliability of electronic devices. Preventing electrical shorts and leakage currents minimizes the risk of malfunctions or damage caused by unintended circuit paths.
Preventing Electrical Shorts: Non conductive epoxy acts as a barrier, reducing the risk of unintended circuit paths leading to shorts or malfunction.
Minimizing Leakage Currents: Effectively sealing electronic components eliminates the chances of leakage currents, ensuring stable and consistent performance.
Improved Durability: By applying Non conductive epoxy, electronic devices become resilient against environmental factors such as temperature variations and humidity, prolonging their lifespan.
Enhanced Product Confidence: Manufacturers can deliver electronic products with increased confidence, knowing that the risk of malfunctions or damage due to electrical issues is significantly reduced.
Versatile Applications: Non conductive epoxy is useful in various electronic assemblies, from consumer electronics to industrial equipment, offering a reliable solution across different sectors.
Cost-Effective Solution: Investing in Non conductive epoxy proves cost-effective in the long run by reducing the need for repairs or replacements due to electrical failures.
Advancements and Innovations
Non conductive epoxy for electronics has undergone remarkable advancements and innovations driven by the need for more efficient and reliable electronic devices. As technology progresses, the demand for materials capable of withstanding increasingly stringent requirements intensifies. Here’s a look at how Non conductive epoxy has evolved and the exciting innovations on the horizon:
Key Advancements
Formulation Refinements: Manufacturers continuously refine formulations to enhance properties like thermal conductivity, adhesion strength, and curing time. These refinements ensure that Non conductive epoxy can meet the evolving demands of modern electronics.
Improved Thermal Conductivity: The latest formulations exhibit superior thermal conductivity, dissipating heat more effectively and ensuring optimal performance even in high-temperature environments. This advancement is crucial for maintaining the longevity and reliability of electronic devices.
Enhanced Adhesion Strength: Enhanced adhesion strength ensures that Non conductive epoxy forms robust bonds with various substrates, including metals, plastics, and ceramics. This improvement contributes to the overall durability and stability of electronic assemblies.
Reduced Curing Time: Faster curing times streamline manufacturing processes, reducing production costs and improving efficiency. Recent developments have led to Non conductive epoxy formulations that cure rapidly without compromising performance or reliability.
Innovations on the Horizon:
Nanocomposite Materials: Nanocomposite materials represent a significant leap forward in Non conductive epoxy technology. Incorporating nanoscale reinforcements, these materials offer unparalleled mechanical, thermal, and electrical properties. They hold the potential to revolutionize electronic device design by enabling greater miniaturization and enhanced reliability.
Tailored Properties:Future advancements in Non conductive epoxy aim to tailor material properties to specific application requirements. This customization could involve optimizing formulations for particular operating conditions, such as extreme temperatures or corrosive environments, further expanding the versatility of these materials.
Conclusion
In the dynamic landscape of electronics manufacturing, the role of Non conductive epoxy cannot be overstated. Its unique blend of insulation, adhesion, and protection contributes significantly to the reliability and longevity of electronic devices. From PCB assembly to component encapsulation, Non conductive epoxy is a critical enabler of innovation, ensuring that electronic products meet the demands of today’s increasingly interconnected world. As advancements continue to drive the evolution of materials and processes, Non conductive epoxy remains a steadfast ally in pursuing electronic excellence.
For more about enhancing electronic reliability: the role of non conductive epoxy, you can pay a visit to DeepMaterial at https://www.electronicadhesive.com/ for more info.