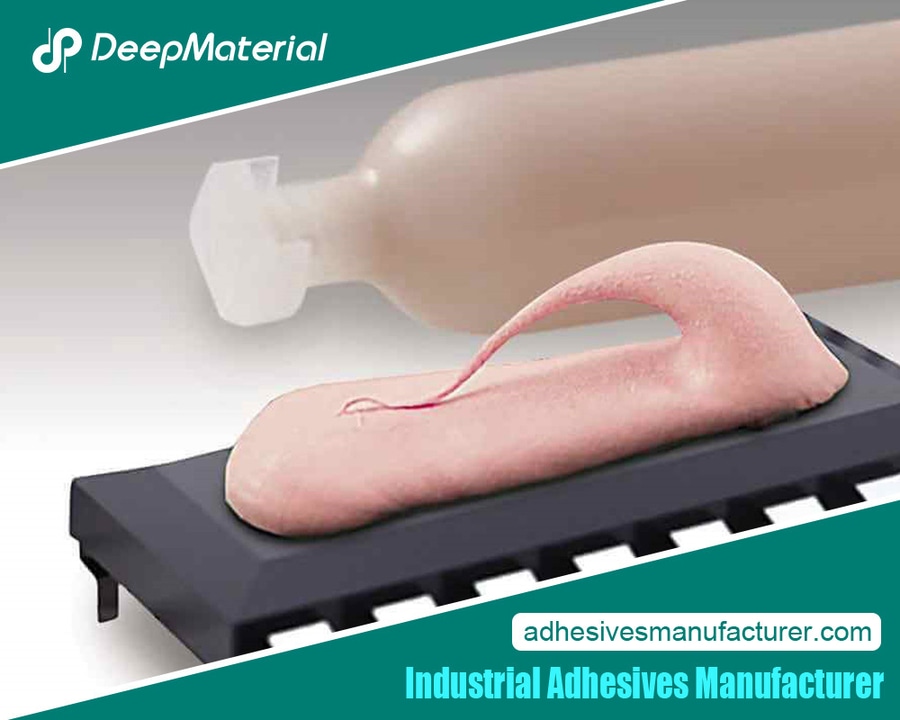
#Industry News
The Ultimate Guide to Electric Appliance Adhesive
Best Electronic Adhesive Glue Manufacturer
Modern technology has made electric appliances indispensable in our daily lives. From kitchen gadgets to sophisticated home entertainment systems, these appliances enhance our convenience and quality of life. However, ensuring their longevity and optimal performance requires meticulous maintenance and sometimes repairs. One critical component in the maintenance of these devices is the use of electric appliance adhesive. This guide delves into the various aspects of electric appliance adhesive, exploring its types, applications, benefits, and best practices.
Understanding Electric Appliance Adhesive
Electric appliance adhesive is a specialized bonding agent designed to join, seal, or repair components of electrical appliances. It is formulated to withstand these devices’ unique challenges, such as heat, electrical conductivity, and durability. Understanding these adhesives’ different types and applications is crucial for effective appliance maintenance.
Types of Electric Appliance Adhesive
Epoxy Adhesives
High strength and durability
Resistant to heat and chemicals
Ideal for bonding metal and plastic parts
Silicone Adhesives
Excellent flexibility and heat resistance
Suitable for sealing and insulating
Commonly used in kitchen appliances and electronics
Acrylic Adhesives
Fast-curing and strong bonding capabilities
Resistant to environmental factors
Great for quick repairs and bonding dissimilar materials
Polyurethane Adhesives
Exceptional toughness and flexibility
Waterproof and heat-resistant
Perfect for heavy-duty applications
Key Properties to Consider
When selecting an electric appliance adhesive, several vital properties must be considered to ensure optimal performance:
Thermal Resistance: The adhesive should withstand high temperatures without degrading, ensuring the longevity and safety of the appliance even under prolonged or intense use.
Electrical Insulation: The adhesive must not conduct electricity for safety. Preventing short circuits and ensuring the appliance operates safely and efficiently is crucial.
Chemical Resistance:Resistance to chemicals like oils and cleaning agents is essential. Appliances often come into contact with various substances during use and cleaning, so the adhesive must maintain its integrity in these environments.
Durability:Long-lasting performance under mechanical stress is crucial. The adhesive should endure the physical strains of daily use, such as vibrations, impacts, and other mechanical stresses, without losing its bonding strength.
Considering these properties helps in choosing an adhesive that meets the specific requirements of electric appliances and enhances their overall reliability and safety.
Applications of Electric Appliance Adhesive
Electric appliance adhesives find applications in various scenarios, from manufacturing to repairs. Here are some common uses:
Manufacturing of Electric Appliances
During the manufacturing process, adhesives are used to bond various components of electric appliances. It includes:
Circuit Boards: Ensuring components stay securely in place.
Housing Assembly: Bonding plastic or metal casings.
Thermal Management: Attaching heat sinks helps to dissipate heat effectively.
Repair and Maintenance
For appliance repair and maintenance, adhesives play a vital role in extending the life of devices:
Fixing Cracks: Repairing cracked plastic or metal parts.
Sealing Gaps: The system is designed to prevent dust and moisture from entering.
Securing Wires:Ensuring electrical connections remain stable.
Enhancing Performance
In some cases, adhesives are used to enhance the performance of appliances:
Vibration Dampening:Reducing noise and wear by securing loose parts.
Heat Insulation: Protecting components from excessive heat.
Benefits of Using Electric Appliance Adhesive
Electric appliance adhesive provides several significant advantages for maintaining and repairing household and industrial appliances. By choosing the suitable adhesive, users can enjoy:
Improved Longevity: Proper application of electric appliance adhesive ensures robust bonding, which can extend the lifespan of appliances by reinforcing critical components and preventing premature wear and tear.
Enhanced Safety: These adhesives are designed to offer excellent electrical insulation, reducing the risk of short circuits and electrical accidents, thereby safeguarding users and appliances.
Cost-Effective: Utilizing adhesive for repairs is often more economical compared to the cost of replacing entire appliances. This approach allows for affordable fixes and can prolong the functional life of appliances.
Versatility: Electric appliance adhesives are formulated to work with various materials and applications, making them suitable for multiple repair and maintenance needs, from securing parts to insulating connections.
Incorporating electric appliance adhesive into maintenance routines can produce more durable, safe, and economical appliance care.
Best Practices for Using Electric Appliance Adhesive
Adhering to best practices is crucial to ensure optimal performance and durability when using electric appliance adhesive. Proper application can significantly enhance the effectiveness of the adhesive and the longevity of repairs. Key practices include:
Surface Preparation:
Clean Surfaces: Always start by ensuring that all surfaces to be bonded are thoroughly clean, dry, and free from grease, dust, or other contaminants. This step prevents weak bonds and potential failures.
Roughen Surfaces: For improved adhesion, lightly roughen the area with sandpaper, particularly on smooth surfaces. It creates a textured surface that allows the adhesive to grip more effectively, leading to more robust and reliable bonds.
By following these best practices, users can maximize the benefits of electric appliance adhesive and achieve better results in repairs and maintenance.
Application Techniques
Use the Right Amount: Apply sufficient adhesive, avoiding excess that could seep out.
Allow Proper Curing Time: Follow the manufacturer’s instructions to ensure strong bonds.
Avoid Stress During Curing: Do not subject the bonded parts to stress during the curing period.
Safety Precautions
Ventilation: Use adhesives in well-ventilated areas to avoid inhaling fumes.
Protective Gear: Wear gloves and safety glasses to protect against skin and eye contact.
Follow Instructions:Adhere strictly to the manufacturer’s guidelines for safe use.
Common Issues and Solutions
Despite best efforts, issues can arise when using electric appliance adhesives. Here are some common problems and their solutions:
Inadequate Bonding
Solution:Ensure surfaces are adequately cleaned and prepped before applying adhesive.
Adhesive Failure
Solution:Check the adhesive’s shelf life and storage conditions. Use fresh adhesive and store it correctly.
Long Curing Time
Solution: Opt for fast-curing adhesives if time is a constraint. Ensure environmental conditions such as temperature and humidity are optimal.
Choosing the Right Adhesive
Selecting the appropriate adhesive depends on the specific requirements of the application. Here’s a guide to help you choose:
For High-Temperature Applications
Recommended Adhesive: Epoxy or silicone adhesives offer high thermal resistance.
For Waterproof Bonding
Recommended Adhesive: Polyurethane adhesives are preferred due to their waterproof properties.
For Fast Repairs
Recommended Adhesive: Acrylic adhesives cure quickly and provide strong bonds.
Conclusion
Electric appliance adhesives are vital for manufacturing and maintaining electric devices. Understanding the different types, applications, and best practices for using these adhesives can significantly enhance the performance and lifespan of your appliances. Selecting suitable adhesives and following proper usage guidelines ensures that your electric appliances remain reliable and efficient for years.
For more about the ultimate guide to electric appliance adhesive, you can pay a visit to Deepmaterial at https://www.adhesivesmanufacturer.com/ for more info.