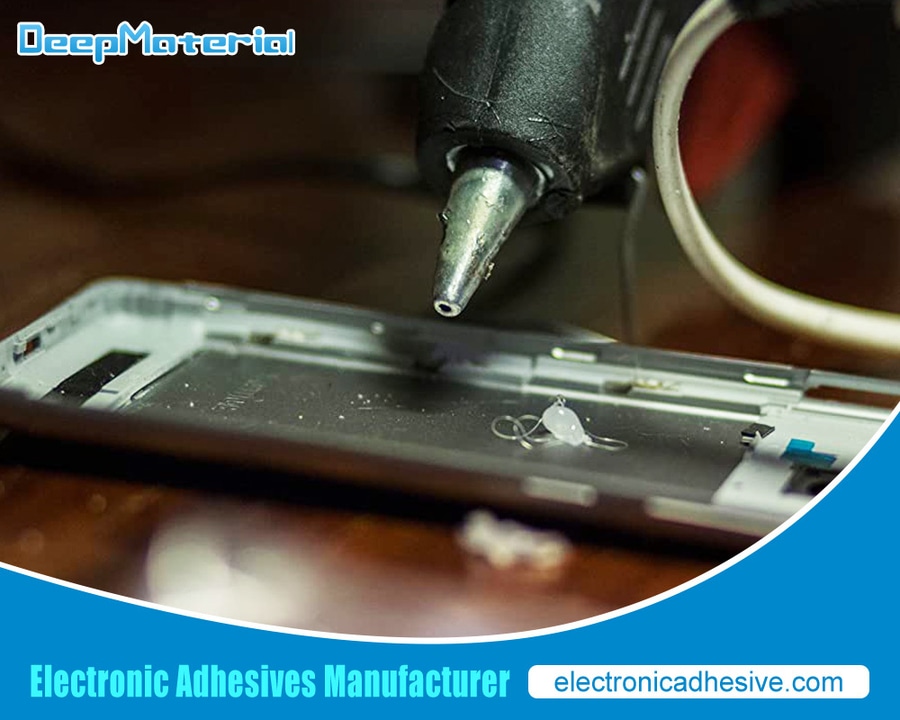
#Industry News
Electronic Encapsulation: An In-Depth Overview
Best Electronic Adhesive Glue Manufacturer
Electronic encapsulation is a critical process in the manufacturing and maintaining electronic devices. It involves enclosing electronic components in protective materials to safeguard them from environmental factors, mechanical damage, and chemical exposure. This process ensures the longevity, reliability, and functionality of electronic devices. As technology advances, so do the methods and materials used in encapsulation. This article overviews electronic encapsulation, exploring its importance, materials used, techniques, applications, and future trends.
1. The Importance of Electronic Encapsulation
Electronic encapsulation is vital for several reasons:
1.1. Protection from Environmental Factors
Electronics are susceptible to damage from environmental elements such as moisture, dust, chemicals, and extreme temperatures. Encapsulation protects sensitive components from these factors, preventing corrosion, short circuits, and degradation. For instance, in outdoor or harsh environments, encapsulation ensures that electronic devices function correctly despite exposure to rain, humidity, and temperature fluctuations.
1.2. Mechanical Protection
Mechanical stress, such as vibrations and impacts, can cause physical damage to electronic components. Encapsulation materials provide a cushioning effect, absorbing shocks and reducing the risk of fractures or other damage. This is particularly important in applications where devices are subjected to constant movement or harsh handling, such as in the automotive or aerospace industries.
1.3. Electrical Insulation
Encapsulation provides electrical insulation, preventing short circuits and unintended interactions between components. It ensures that electrical pathways remain intact and that components operate within their intended parameters. This is crucial for maintaining the reliability and safety of electronic devices.
1.4. Enhanced Reliability and Longevity
By protecting electronic components from external stresses and potential failures, encapsulation enhances electronic devices’ overall reliability and longevity. This is especially important for critical systems where failure could have severe consequences, such as in medical devices, aerospace applications, and industrial control systems.
2. Materials Used in Electronic Encapsulation
Various materials are used in electronic encapsulation, each offering different properties and benefits:
2.1. Epoxy Resins
Epoxy resins are widely used due to their excellent adhesive properties, chemical resistance, and electrical insulation capabilities. They are often used in potting and molding applications, where the resin is cured to form a solid protective layer around the electronic components. Epoxy resins are suitable for various applications, including automotive, consumer, and industrial equipment.
2.2. Silicone Compounds
Silicone compounds offer flexibility, high-temperature stability, and resistance to moisture and chemicals. They are used in applications where components are exposed to extreme temperatures or require flexibility. Silicone encapsulants are commonly used in the automotive, aerospace, and consumer electronics industries.
2.3. Polyurethane Materials
Polyurethane materials provide good mechanical protection and chemical resistance. They are used in applications where impact resistance and durability are essential. Polyurethane encapsulants are often used in electronic devices that require enhanced shock absorption and protection from environmental factors.
2.4. Ceramic Materials
Ceramic materials like ceramic-filled epoxies offer excellent thermal conductivity and electrical insulation. They are used in high-performance applications where heat dissipation and electrical isolation are critical. Ceramic encapsulants are commonly found in power electronics, high-frequency devices, and LED lighting applications.
2.5. Thermoplastic Materials
Thermoplastic materials, such as polycarbonate and ABS, are used in molding applications where ease of processing and impact resistance are essential. These materials can be melted and reformed, making them suitable for applications that require high durability and flexibility.
3. Encapsulation Techniques
Several techniques are employed in electronic encapsulation, each suited to different types of electronic components and applications:
3.1. Potting
Potting involves filling a cavity or enclosure with a liquid encapsulant that cures to form a solid protective layer. This technique is commonly used for encapsulating small electronic components, such as circuit boards and sensors. Potting provides excellent protection against environmental factors and mechanical stresses.
3.2. Molding
Molding involves shaping an encapsulant material around electronic components using a mold. This technique is suitable for encapsulating more significant components or assemblies. Molding provides a precise and uniform protective layer, ensuring consistent protection across the entire component.
3.3. Coating
Coating involves applying a thin layer of encapsulant material to the surface of electronic components. This technique is often used for surface-mounted devices and protects against moisture, dust, and chemical exposure. Coatings can be applied using various methods, including spraying, dipping, and brushing.
3.4. Encapsulation with Overmolding
Overmolding involves adding a second layer of encapsulant material over an already encapsulated component. This technique provides additional protection and can create complex geometries or integrate multiple components into a package. Overmolding is commonly used in applications requiring extra protection or enhanced mechanical properties.
4. Applications of Electronic Encapsulation
Electronic encapsulation is used across various industries and applications, including:
4.1. Consumer Electronics
Encapsulation protects consumer electronics devices such as smartphones, tablets, and wearables from environmental factors and mechanical damage. It ensures that these devices remain functional and reliable throughout their lifespan despite daily use and exposure to various conditions.
4.2. Automotive Industry
The automotive industry relies on electronic encapsulation to protect vehicle components, including engine control units, sensors, and infotainment systems. Encapsulation ensures that these components withstand extreme temperatures, vibrations, and chemical exposure, contributing to vehicle safety and performance.
4.3. Aerospace Industry
In aerospace applications, encapsulation is crucial for protecting electronic systems in aircraft and spacecraft. Encapsulation materials must withstand high temperatures, radiation, and mechanical stresses during flight and space missions. This ensures the reliability and functionality of critical systems in these demanding environments.
4.4. Medical Devices
Medical devices, such as pacemakers, diagnostic equipment, and implants, require reliable electronic encapsulation to ensure their safety and effectiveness. Encapsulation protects sensitive electronics from bodily fluids, chemicals, and mechanical stresses, contributing to medical devices’ overall performance and longevity.
4.5. Industrial Equipment
Industrial equipment often operates in harsh environments with dust, moisture, and chemical exposure. Encapsulation protects electronic components in industrial machinery, control systems, and automation equipment, ensuring reliable operation and reducing maintenance requirements.
5. Future Trends in Electronic Encapsulation
As technology advances, several trends are shaping the future of electronic encapsulation:
5.1. Advanced Materials
The development of advanced encapsulation materials, such as nanocomposites and self-healing polymers, is enhancing the performance and reliability of electronic encapsulation. These materials offer improved protection, flexibility, and durability, addressing the evolving demands of modern electronics.
5.2. Miniaturization
The trend toward miniaturization in electronics drives the need for encapsulation solutions that accommodate smaller components and intricate designs. Innovations in encapsulation techniques and materials enable the development of compact and efficient encapsulation solutions for miniature electronic devices.
5.3. Sustainability
Sustainability is becoming a key focus in electronic encapsulation. The industry is exploring eco-friendly encapsulation materials and processes to reduce environmental impact. This includes using biodegradable materials, recycling initiatives, and reducing the reliance on hazardous chemicals.
5.4. Integration with Smart Technologies
Integrating intelligent technologies, such as sensors and IoT devices, drives the need for advanced encapsulation solutions supporting connectivity and data transmission. Encapsulation materials and techniques are being developed to accommodate the unique requirements of intelligent electronics, including wireless communication and energy harvesting.
Conclusion
Electronic encapsulation ensures electronic devices’ performance, reliability, and longevity. By protecting components from environmental factors, mechanical stresses, and electrical interference, encapsulation enhances the functionality and durability of electronic systems across various industries. As technology advances, innovations in materials, techniques, and applications will shape the future of electronic encapsulation, addressing new challenges and opportunities in the evolving electronics landscape.
For more about choosing the Top Electronic Encapsulation: An In-Depth Overview, you can pay a visit to DeepMaterial at https://www.electronicadhesive.com/ for more info.