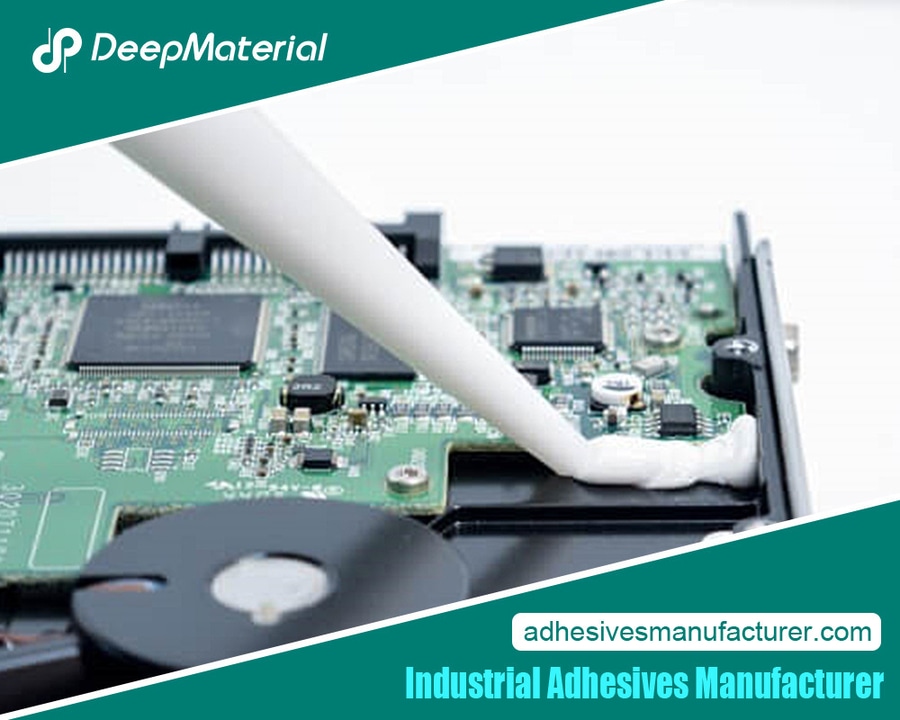
#Industry News
Innovative Solutions for Electrical Insulation with Epoxy Resins
Best Electronic Adhesive Glue Manufacturer
Electrical insulation is a critical component in designing and operating electrical systems. It ensures the safety, efficiency, and longevity of devices ranging from household electronics to industrial machinery and high-voltage power lines. Among the various materials used for electrical insulation, epoxy resins have emerged as a leading solution due to their exceptional insulating properties, mechanical strength, and versatility. In this article, we will explore the various solutions for electrical insulation using epoxy resins, discussing their applications, benefits, and innovative techniques that enhance performance in different environments.
Understanding Epoxy Resins as Insulation Materials
Composition and Properties of Epoxy Resins
Epoxy resins are thermosetting polymers known for their excellent adhesive properties, chemical resistance, and high mechanical strength. These characteristics make them an ideal material for electrical insulation. The primary components of epoxy resins include:
Epoxy Prepolymers: The base component that determines the resin’s properties.
Curing Agents: Chemicals that initiate the polymerization process, transforming the liquid resin into a solid state.
Fillers and Additives:Enhance the epoxy resin’s thermal, mechanical, and electrical properties.
Key Electrical Insulating Properties of Epoxy Resins
The suitability of epoxy resins for electrical insulation stems from several fundamental properties:
Dielectric Strength: Epoxy resins can withstand high electrical stress without breaking down, making them suitable for high-voltage applications.
Low Electrical Conductivity: This prevents electrical leakage and ensures the efficient operation of electronic components.
Thermal Stability: Epoxy resins can operate at high temperatures without losing their insulating properties, which is crucial for applications in harsh environments.
Moisture Resistance: They provide excellent resistance to moisture, preventing short circuits and degradation over time.
Applications of Epoxy Resins in Electrical Insulation
Insulation in Transformers and Motors
Epoxy resins are widely used in transformers and electric motors because they provide robust insulation under extreme conditions.
Transformers: Epoxy resin insulates the windings, core, and other critical components, preventing short circuits and enhancing the transformer’s efficiency.
Motors:The windings in electric motors are often insulated with epoxy resins, which protect against electrical stress, heat, and environmental factors like moisture and dust.
Printed Circuit Boards (PCBs)
PCBs are the backbone of modern electronics, and epoxy resins play a vital role in their insulation.
PCB Coating: Epoxy resins coat PCBs, providing a protective layer that insulates electrical connections, protects against corrosion, and enhances the board’s mechanical strength.
Encapsulation of Components: Critical components on PCBs, such as integrated circuits and capacitors, are often encapsulated with epoxy resin to protect against environmental factors and ensure reliable performance.
Cable Jointing and Termination
In high-voltage cable systems, epoxy resins are essential for jointing and terminating cables, ensuring that connections remain insulated and protected.
Cable Jointing: Epoxy resin encapsulates cable joints, providing mechanical protection and preventing electrical faults due to moisture ingress or mechanical stress.
Cable Termination: The ends of high-voltage cables are terminated with epoxy resin to ensure a reliable and durable connection to other components.
Advantages of Using Epoxy Resins in Electrical Insulation
Exceptional Mechanical Strength
Epoxy resins offer high mechanical strength, which is crucial for applications where insulation, such as motors and transformers, must withstand mechanical stress. This strength ensures the insulation remains intact under mechanical loads, vibrations, and impacts.
Enhanced Chemical and Moisture Resistance
Epoxy resins are highly resistant to chemicals and moisture, making them suitable for harsh environments. This resistance ensures that the epoxy resin’s insulating properties are maintained even in the presence of corrosive substances or high humidity.
Long-Term Durability
Another significant advantage of epoxy resins is their durability. Once cured, epoxy resins form a hard, stable material that can withstand long-term exposure to electrical, thermal, and environmental stresses without degrading. This long-term durability reduces the need for frequent maintenance and replacement of insulating materials.
Versatility in Application
Epoxy resins are versatile and can be formulated for various applications, including potting, encapsulation, and coatings. This versatility allows engineers to tailor the resin to meet specific insulation requirements for different electrical components.
Innovative Techniques in Epoxy Resin Insulation
Nanotechnology in Epoxy Resins
Nanotechnology has introduced new possibilities for enhancing the insulating properties of epoxy resins.
Nanocomposites: Incorporating nanoparticles, such as silica, alumina, or carbon nanotubes, into epoxy resins can significantly improve their dielectric strength, thermal conductivity, and mechanical properties.
Improved Thermal Management: Nanocomposite epoxy resins offer better thermal management, reducing the risk of overheating in high-power electrical systems.
UV-Curable Epoxy Resins
UV-curable epoxy resins are a recent innovation allowing rapid curing under ultraviolet light. This technology offers several benefits:
Faster Production: The quick curing process reduces production time, making it ideal for high-volume manufacturing of electrical components.
Precision Application: UV-curable resins can be precisely applied to small or intricate components, ensuring uniform insulation.
Epoxy-Based Flexible Insulation
Traditional epoxy resins are rigid after curing, but advancements have led to the development of flexible epoxy resins for specific applications.
Flexible Circuit Boards: These resins are used in flexible circuit boards, where insulation must withstand bending and flexing without cracking.
Flexible Coatings: Flexible epoxy coatings are applied to components that require insulation and flexibility, such as in wearable electronics or robotics.
Challenges and Solutions in Using Epoxy Resins for Electrical Insulation
Thermal Management
One of the primary challenges in using epoxy resins is managing heat dissipation in high-power applications.
Solution:Incorporating thermally conductive fillers, such as aluminum oxide or boron nitride, into the epoxy resin can enhance its thermal conductivity, helping to dissipate heat more effectively.
Environmental Degradation
Exposure to UV radiation, moisture, and chemicals can degrade epoxy resin over time.
Solution: Applying protective coatings or using UV-stabilized epoxy formulations can extend the lifespan of the insulation in outdoor or harsh environments.
Processing and Handling Difficulties
Epoxy resins require precise mixing and curing conditions to achieve optimal properties, which can be challenging in large-scale production.
Solution: Automated mixing and dispensing systems and controlled curing environments can ensure consistent quality and performance in the final product.
Future Trends in Epoxy Resin Insulation
Sustainable and Eco-Friendly Epoxy Resins
As environmental concerns grow, the development of sustainable and eco-friendly epoxy resins is gaining momentum.
Bio-Based Epoxy Resins: Derived from renewable sources, these resins offer a greener alternative to traditional petrochemical-based epoxies.
Recyclable and Biodegradable Formulations: Advances in chemistry are leading to epoxy resins that can be recycled or biodegraded, reducing their environmental impact.
Smart Epoxy Resins
The integration of intelligent technologies into epoxy resins is an emerging trend.
Self-Healing Epoxy Resins: These materials can autonomously repair minor cracks or damage, extending the lifespan of the insulation.
Conductive Epoxy Resins: While epoxy resins are typically insulative, conductive variants are being developed for applications requiring selective conductivity, such as in sensors or advanced electronics.
Advanced Manufacturing Techniques
Adopting advanced manufacturing techniques is set to revolutionize using epoxy resins in electrical insulation.
3D Printing with Epoxy Resins: 3D printing technology enables the creation of complex, customized insulating components with epoxy resins, reducing material waste and production time.
Additive Manufacturing: This technique allows for the precise application of epoxy resin in layers, enhancing the performance and reliability of insulated components.
Conclusion
Epoxy resins have proven to be an indispensable material in electrical insulation, offering unmatched properties such as high dielectric strength, thermal stability, and resistance to environmental factors. From traditional applications like transformers and PCB coatings to innovative uses in flexible circuits and nanocomposites, epoxy resins continue to evolve, meeting the demands of modern electrical systems. As advancements in technology and materials science drive the development of new epoxy formulations and applications, the future of electrical insulation looks promising, with epoxy resins playing a central role in ensuring the safety, efficiency, and longevity of electrical systems across various industries. Embracing these innovative solutions will enhance electrical components’ performance and contribute to a more sustainable and reliable electrical infrastructure.
For more about choosing the best innovative solutions for electrical insulation with epoxy resins, you can pay a visit to Deepmaterial at https://www.adhesivesmanufacturer.com/ for more info.