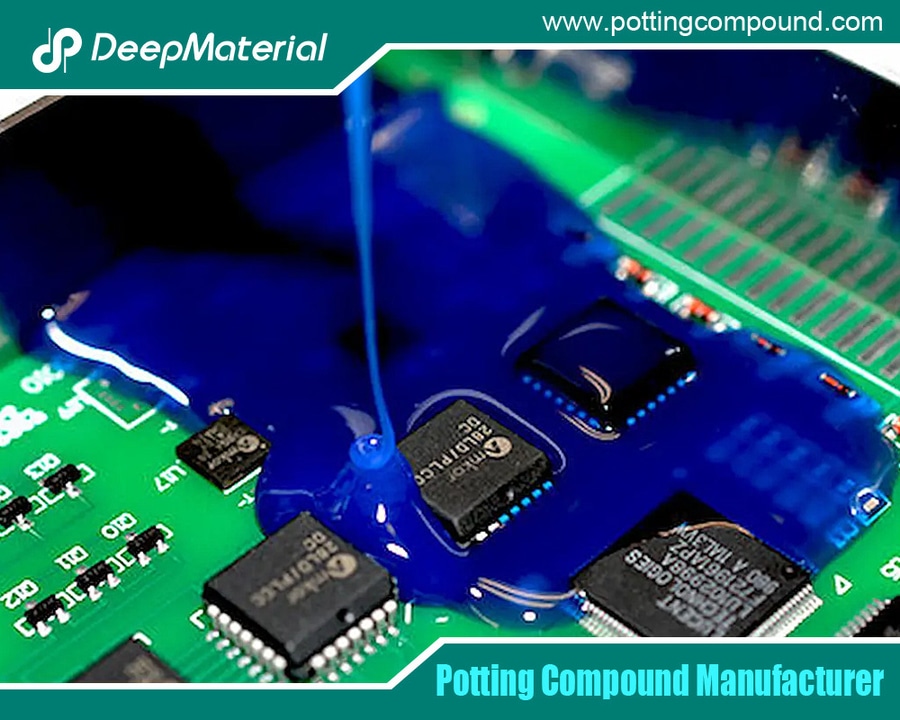
#Industry News
Mastering Non Conductive Epoxy: Essential Applications for Electronic Projects
Best Mastering Non Conductive Epoxy Adhesive Glue Manufacturer
The demand for advanced materials that ensure reliability, performance, and longevity is ever-growing in modern electronics. Among these materials, Non conductive epoxy has become an essential component for various electronic applications. Its unique properties make it an invaluable tool in safeguarding sensitive electronic components, providing thermal stability, mechanical strength, and electrical insulation.
This article delves deep into the significance, benefits, and uses of Non conductive epoxy for electronics, highlighting its critical role in advancing modern devices.
Understanding Non conductive Epoxy
Non conductive epoxy is a two-part adhesive or potting compound primarily used in electronics to bond, seal, encapsulate, or coat components. What sets it apart from conductive epoxy is its ability to provide insulation against electrical currents. This characteristic is crucial when dealing with electronic systems, where components must remain isolated from electrical charges to function optimally.
Key Features of Non conductive Epoxy:
Electrical Insulation: Prevents short circuits and safeguards electronic components from electrical interference.
Thermal Resistance: Maintains stability under extreme temperature conditions, protecting heat-sensitive components.
Mechanical Strength: Provides excellent bonding and sealing, ensuring durability against vibrations, shock, and environmental factors.
Chemical Resistance:It is resistant to corrosive chemicals, moisture, and environmental hazards, preserving the integrity of electronic components.
The Role of Non conductive Epoxy in Electronics
The evolution of electronics, from consumer gadgets to industrial applications, relies heavily on materials that can ensure the longevity and performance of these devices. Non conductive epoxy plays a pivotal role in this ecosystem due to the following reasons:
Component Protection:
Electronic components, especially those in delicate systems such as circuit boards, are vulnerable to external factors like moisture, dust, and physical impact. Non conductive epoxy encapsulates these components, providing a protective layer that prevents damage while maintaining electrical insulation.
Thermal Management:
Many electronic systems generate heat, and maintaining thermal stability is critical for longevity. Non conductive epoxy resists high temperatures and provides a thermal buffer, preventing overheating and damage to components.
Bonding and Adhesion:
In electronics manufacturing, various materials must be bonded securely without interfering with the system’s electrical properties. Non conductive epoxy provides a reliable adhesive solution, ensuring the components stay intact even under strenuous conditions like vibrations or physical stress.
Electrical Insulation:
One key requirement in electronics is the prevention of unwanted electrical current flow between components. Non conductive epoxy acts as an insulator, preventing electrical shorts and ensuring that components operate within their designated circuits.
Miniaturization of Electronics:
As devices become smaller and more compact, the need for materials that can provide high performance in confined spaces becomes increasingly essential. Non conductive epoxy enables the secure placement and protection of tiny, delicate components, ensuring they function correctly without compromising the device’s size or efficiency.
Types of Non conductive Epoxies for Electronics
Several varieties of Non conductive epoxy exist, each designed to suit specific electronic applications. The choice of epoxy often depends on the project’s particular requirements, such as environmental conditions, thermal resistance, or chemical exposure.
Epoxy Potting Compounds:
Potting compounds are used primarily for encapsulating electronic components. They protect circuits from environmental damage, mechanical stress, and corrosion. These compounds offer excellent electrical insulation and are used in applications ranging from automotive electronics to industrial machinery.
Adhesive Epoxies:
These epoxies are designed for bonding purposes and provide a strong adhesive bond between various materials without compromising their electrical properties. They are often used in assembling circuit boards or attaching delicate components to substrates.
Thermally Conductive, Electrically Insulative Epoxies:
While most Non conductive epoxies are designed purely for electrical insulation, some are engineered to manage heat transfer without conducting electricity. These types of epoxies are essential in applications where efficient heat dissipation is required to maintain the performance of electronic systems.
Low Viscosity Epoxies:
Low-viscosity epoxies provide an easy-to-apply solution for applications requiring precise application or encapsulation of small components. These epoxies can flow into tight spaces, ensuring complete coverage and protection of sensitive electronics.
Applications of Non conductive Epoxy in the Electronics Industry
Non conductive epoxy is widely used across various sectors of the electronics industry, ensuring the performance and longevity of both consumer and industrial electronic devices.
Printed Circuit Boards (PCBs):
PCBs are the backbone of modern electronic devices, requiring protection from environmental factors like moisture, dust, and corrosion. Non conductive epoxy is commonly used to coat PCBs, ensuring they remain insulated from external electrical interference while staying protected from physical damage.
LEDs and Display Panels:
In LED manufacturing, Non conductive epoxy encapsulates the delicate internal components, protecting them from environmental stress and ensuring efficient performance. The same applies to display panels, where the epoxy maintains insulation while safeguarding sensitive electronics.
Semiconductors and Microchips:
As semiconductors and microchips become more complex and powerful, they generate heat that must be managed efficiently. Non conductive epoxy provides a protective, thermally stable layer that ensures these components remain isolated from electrical interference while allowing heat dissipation.
Automotive Electronics:
Modern vehicles rely on many electronic systems, from sensors and infotainment units to engine control modules. Non conductive epoxy protects these systems from extreme temperatures, vibrations, and exposure to chemicals like oils and fuels.
Aerospace and Defense:
Electronics are exposed to some of the harshest environmental conditions in aerospace and defense applications. Non conductive epoxy provides the necessary insulation and mechanical stability to ensure that these systems perform reliably under extreme pressure, temperature, and stress.
Advantages of Using Non conductive Epoxy for Electronics
Non conductive epoxy offers numerous advantages over other materials, making it the preferred choice for a wide range of electronics industry applications.
Improved Durability and Longevity:
By providing a robust barrier against environmental factors and mechanical stress, Non conductive epoxy significantly enhances the durability and lifespan of electronic components.
Cost Efficiency:
Non Conductive epoxy is cost-effective compared to other materials that provide electrical insulation or bonding. Its versatility allows manufacturers to use it across various applications, reducing the need for multiple specialized products.
High Performance in Harsh Environments:
Non conductive epoxy is designed to withstand extreme conditions, from high temperatures to exposure to corrosive chemicals. This makes it ideal for applications in harsh environments, such as automotive or industrial electronics.
Versatility and Adaptability:
Non Conductive epoxy can be used in various applications, from small consumer electronics to large industrial systems. Its ability to bond, insulate, and protect makes it a versatile material that can be adapted to the project’s specific needs.
Future Trends in Non conductive Epoxies for Electronics
As the electronics industry continues to evolve, several emerging trends in Non conductive epoxy technology aim to enhance performance and adaptability.
Environmentally Friendly Formulations:
With increasing attention to sustainability, there is a growing demand for eco-friendly, Non conductive epoxy formulations that use biodegradable or less harmful chemicals without compromising performance.
Higher Thermal Conductivity:
While maintaining electrical insulation, future Non conductive epoxies may focus on improved thermal conductivity to better manage heat dissipation in increasingly powerful electronic systems.
Nanotechnology Integration:
Integrating nanomaterials into Non conductive epoxy formulations can further enhance its electrical insulation, mechanical strength, and chemical resistance, paving the way for more durable and efficient electronic systems.
Conclusion
Non conductive epoxy is a critical material in the electronics industry, offering protection, insulation, and durability to various electronic components. From safeguarding printed circuit boards to ensuring the longevity of automotive and aerospace electronics, its applications are diverse and vital to modern technology. With the growing demand for smaller, more powerful devices, the role of Non conductive epoxy in electronics is expected to expand, driven by advancements in material science and emerging technologies.
For more about choosing the top mastering non conductive epoxy: essential applications for electronic projects, you can pay a visit to DeepMaterial at https://www.pottingcompound.com/ for more info.