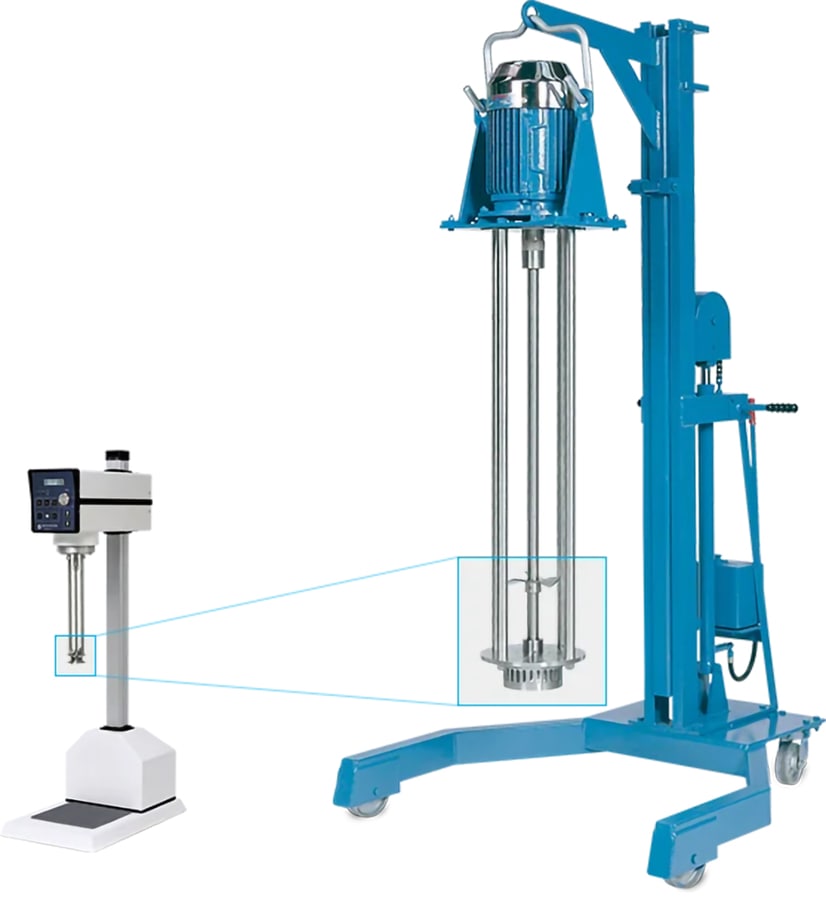
#Product Trends
Scaling up with Silverson Machines
Scale up is a critical stage in any production process, and it is increasingly seen as a vital factor in decision-making when specifying a new mixer.
Silverson Machines has over 75 years’ practical experience in helping clients with some of the most difficult mixing challenges, offering unrivalled expertise when it comes to scaling up.
There are a number of key factors that must be taken into consideration by manufacturers wanting to scale up and expand their production process. It would be ideal to consider these factors before laboratory scale production is underway so that scale up can progress seamlessly, without the need for reformulation or changing the existing mixing process.
As such, at Silverson, we emphasize to our customers that mixing “parameters” – tip speed, stator design, mixing time – need to be considered prior to the beginning of laboratory or pilot scale trials, as anything extreme among these parameters can be difficult to replicate on a larger scale. We advise our customers that these parameters should stay within sensible limits. For example, a laboratory mixer running at 10,000 rpm for over an hour in a 1-litre beaker to get the desired product quality may be impossible to scale up.
Another issue to remember concerning mixer speed is that lab mixers need to be run at a faster rpm than their production counterparts in order to ensure the peripheral tip speed – and therefore the shear rate – is comparable between laboratory and production scale equipment. It’s a common error to run a lab mixer at 3,000 rpm because this is the speed most production models run at, but this won't give you an accurate idea of full-scale results; in fact a lab mixer running at 8,000 rpm has a tip speed that more closely matches the standard 3,000 rpm of most larger in-tank batch mixers.
The stator design or geometric similarity needs to be taken into consideration when wanting to replicate results. At Silverson, the Verso Laboratory-scale In-Line mixer has the same geometric design as full-scale UHS In-Line mixers, meaning the rotor and stator are engineered to the same fine tolerances. This allows us to easily forecast the results of larger batches at smaller scale.
Another thing that manufacturers must consider is the tank turnover rate - the amount of time it takes to recirculate the product. As batch sizes and vessels increase in size, the processing time will do the same. Manufacturers must be prepared to mix for longer as mixer flow rates will decrease as batches become larger. Which leads to another factor that manufacturers must consider, flow rates decreasing may mean that additional equipment, such as feed pumps or scraper/stirrer units in the vessel are needed to maintain flow rates when mixing more viscous products. Consideration must be given to other equipment used in the process elsewhere as well. When mixing at pilot scale what is used to assist the process - moving the beaker by hand? Using a spatula to agitate the product in the vessel? When this is necessary at smaller scale, then manufacturers may need to be prepared to invest in additional agitating equipment when scaling up in order to replicate the process.
Other types of ancillary equipment to be used when scaling up such as vessels, hoses/pipes and pumps is also very important to discuss beforehand. Usually, manufacturers will want to use their existing equipment, which can work but may have its limitations. For example, if a pilot scale processing line was using vessels with 1" outlets and 1" hoses as standard, this set-up would not be able to successfully run any of the production scale powder/liquid mixers from Silverson. So if the intention is to scale up to a much higher capacity machine this must be flagged beforehand and appropriate fittings must be used.
Silverson laboratory mixers are able to provide a good indication of whether or not a process is viable with a high shear mixer, but we also offer dedicated In-Line laboratory scale models which may be more appropriate when a process is going to be carried out with an In-Line mixer at production scale. Silverson Machines are leaders in the design, manufacture and application of high shear mixing equipment. For over 75 years we have been helping clients to solve some of the most difficult mixing challenges and can offer expert advice to ensure you obtain the right mixer for your application. To speak to us about scaling up your mixing process, please contact: sales@silverson.co.uk or for more information visit the Silverson website: www.silverson.com