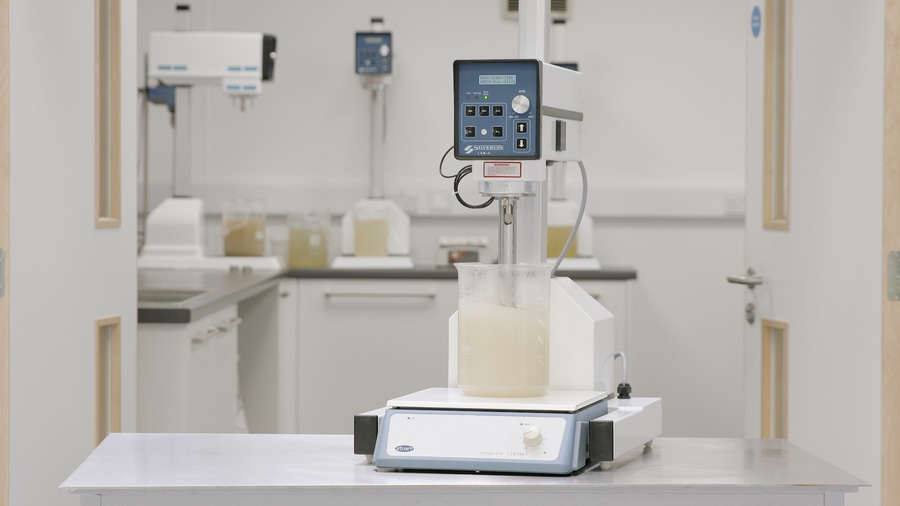
#Industry News
How have Silverson helped their customers? Find out in their new case study library
Silverson Machines has helped thousands of customers worldwide improve their mixing processes and product quality with the use of High Shear Mixing.
In the recently added Case Studies library on the Silverson website, users can read about ‘real world’ instances in which Silverson high shear mixers have helped customers to reduce mixing and process times, increase yield of raw materials, save money and improve the manufacturing process.
Below is a summary of some of the results achieved in a few of the applications featured in the library. Five case studies are already available to read in full on the Silverson website, with more to be added regularly.
Manufacturer cuts 20% Pectin from their formulation by switching to a High Shear Mixer
A food manufacturer got in touch with Silverson for help revitalising their mixing process after their previous mixing set-up became too expensive to sustain due to the high percentage of pectin in their formulation.
Since switching from a conventional agitator to a Silverson Flashmix powder/liquid mixer this manufacturer has reduced the amount of pectin in their formulation by 20%.
In the trials carried out with Silverson Machines, using the Flashmix 5% of pectin was quickly incorporated via the powder hopper into the liquid stream. After a short recirculation period, hydration was complete and the customer got the results they wanted with no need to add excess amounts of powder.
Incorporating 5% pectin quickly and effectively meant a 20% reduction in pectin compared to their previous process. The cost implications of this were huge, so much so that the mixer would pay for itself many times over with the savings made on the raw material. In addition, further money would be saved due to the shorter processing time, and because it eliminated the problems with partially hydrated pectin in the vessel, greatly improved process hygiene.
In this case, achieving the full yield of the pectin was only possible once high shear was introduced into the process. Compared to the agitator, the Silverson mixer produced a higher quality product with greater consistency between batches, whilst saving the manufacturer money.
Silverson powder/liquid mixer reduces mixing times by over 23 hours
Another company mixing gums and thickeners, this time Xanthan Gum, CMC, Carbomers as well pigments for different products, contacted Silverson for help improving their process. They had been using a fast impeller to incorporate these ingredients but this process was anything but fast, in some cases, the impeller was left to run for an entire day to complete the mix!
Despite these very long mixing times, the resulting mix was of poor quality with lumps of un-hydrated, undispersed powder still present. This meant further lengthening process times with a filtration stage to remove the agglomerates.
After coming across the Silverson YouTube channel, and watching our ‘How to’ video on dispersing Xanthan Gum the company got in touch with their nearest sales office – Silverson France. Our mixing experts knew from prior experience that dispersing these powders should not be this difficult or be taking such a long time for a poor-quality product. After discussing with the company what they wanted to achieve, a Flashmix Powder/Liquid mixer from the Silverson demonstration fleet was sent to their facility so that they could carry out trials on-site.
The first trial involved dispersing 17kg of Xanthan Gum into 3500 litres of Vinegar. With the FMX50 all of the Xanthan Gum was introduced into the mix within 50 seconds. The mixture was then left to recirculate for 35 minutes. After this time the mixture was to the exact standard required, with no agglomerates so there was no filtration stage needed. This reduced the mixing time by over 23 hours compared to the fast impeller!
How Silverson helped a bakery company reduce waste and save millions of pounds
One baked goods manufacturer reached out to Silverson team for guidance in helping address their huge amounts of waste. One production line was producing 2 tonnes of unsellable product per day which combined with additional waste from their other product lines, quickly became a massive problem and accounted for millions of pounds of rejected material annually.
Silverson suggested reprocessing the rejected material to form a percentage of the ingredients for new products. By reducing the rejected product down into a slurry, 10–15% of the formulation of each new batch can be made up of reclaimed material. A trial was run using a pilot-scale Disintegrator Plant incorporating a Bottom Entry mixer and a High Viscosity In-Line mixer. The waste product was incorporated into water to see if a usable slurry could be produced. The Bottom Entry mixer was started and immediately disintegrated the product down into a porridge-like consistency. The mixture was then passed through the In‑Line mixer producing a smooth, agglomerate-free slurry, with the whole process taking less than 15 minutes.
It was predicted that using this slurry in subsequent batches of product would increase the quality of the product and result in savings of £2.5 million pounds.
Read these success stories in full and other additional case studies on the Silverson website: www.silverson.co.uk