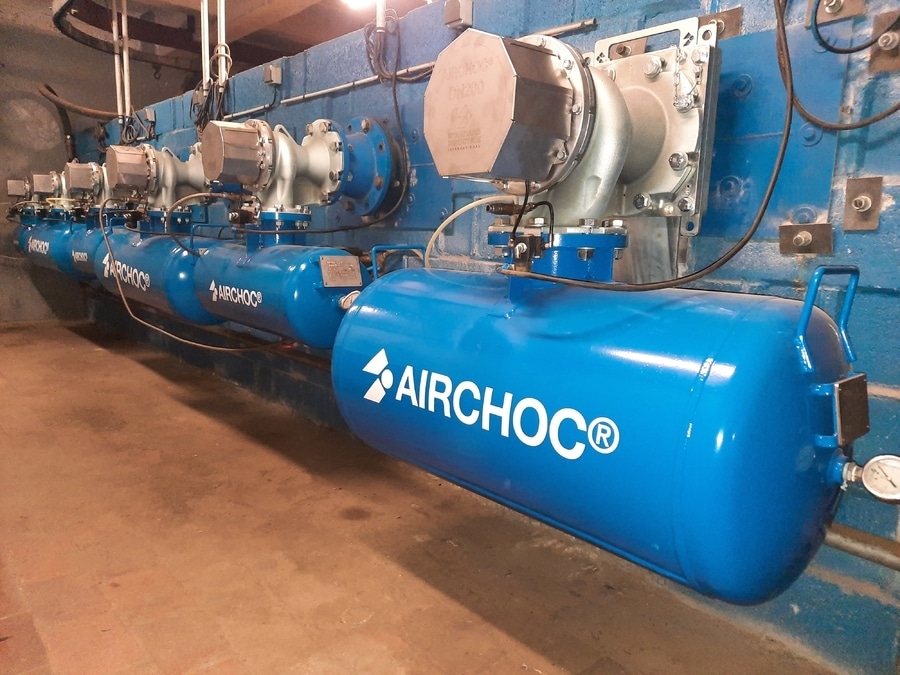
#Product Trends
DECLOGGING INSIDE SILOS :
THE AIRCHOC® 6 SOLUTION SIMPLIFIES MAINTENANCE AND SPARE PARTS COSTS
Created in 1978 by the French company STANDARD INDUSTRIE International, the AIRCHOC® is an air cannon that is placed preventively on raw material storage units. Thanks to regular shots, it allows to avoid production stops due to material accumulation.
It is a cost-effective maintenance solution that uses 6 bar compressed air only when the shots are activated and is adaptable to many bulk areas.
STANDARD INDUSTRIE International's technical teams study an optimal installation recommendation according to the clogging factors and the environment of use (risks, high heat zone, corrosiveness, humidity).
Particularly attentive to its customers' requirements, the design office team spent nearly 3 years testing modifications to its legendary AIRCHOC® air cannon:
- The quick exhaust valve was replaced with a pneumatic valve system that improves impact force.
- The silencers have been replaced by a protective cap which, in addition to protecting the new valve system, absorbs the noise caused by the shots. The main advantage is that there is no risk of clogging in the exhaust system.
- As these 2 wearing parts (Quick exhaust valve + Silencer) are removed from the design, maintenance is simplified and less expensive for the user.
What benefits does the new version of the AIRCHOC® air cannon bring?
The AIRCHOC® has always had the performance, profitability and safety characteristics expected by user customers. The latest innovations of the AIRCHOC® version 6 are focused on :
Compressed air savings, thanks to a better sealing of the piston and thanks to a better impact force on the clogging (10% higher than the old version).
Indeed, the air pressure can be reduced for an equivalent result.
The version 6 of The AIRCHOC® meets the challenges of the global energy saving policy.
Reliability, particularly due to an improvement of the impact force of the shots coming from the cannon. (No quick exhaust valve): No air passes through the piston seal, thus no wear and tear on the seal.
This means that the air cannons are always available for preventive shots and thus maintain the production flow. The tests guarantee 3 years of shooting cycles without replacement of the triggering system.
Spare parts, which have been streamlined and selected for their durability.
The new design of the AIRCHOC® with fewer wearing parts and components ensuring good resistance, allows for reduced and simplified maintenance. This is a considerable advantage when maintenance operations require access at height and important safety precautions.
In this regard, Standard Industrie has also created an AIRCHOC® maintenance kit that avoids operators and foremen from having to perform lengthy and costly interventions.
Here again, Standard Industrie responds to the need to save on maintenance and spare parts for large consumers such as cement plants.
In summary, the AIRCHOC® is the solution for plants that want to reduce maintenance and spare parts replacement on their cleaning system, and reduce their compressed air consumption.