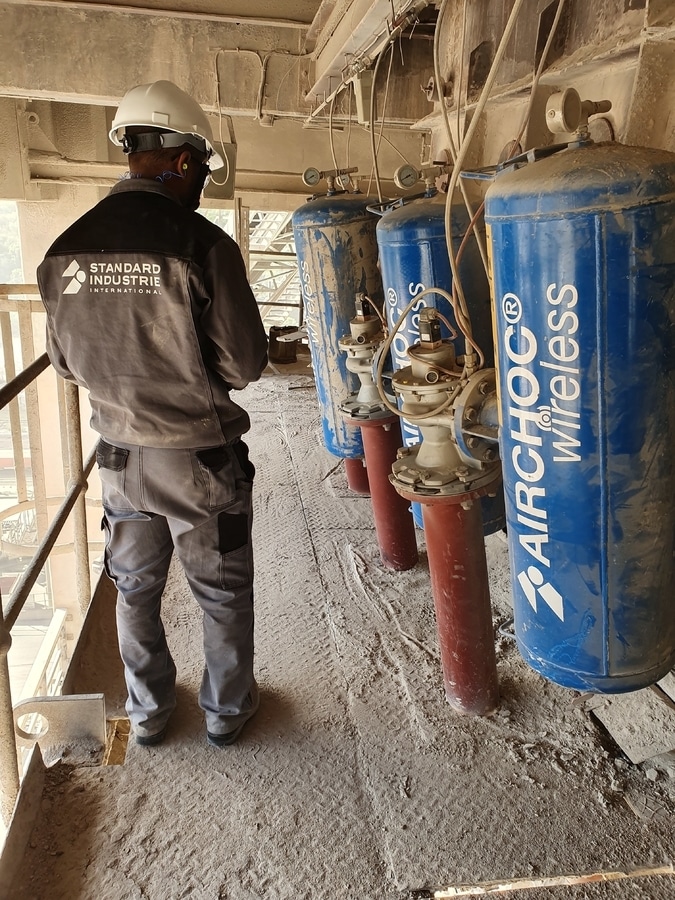
#Industry News
How to guarantee the maintenance of the cement production flow in 5 points?
Cement manufacturers can use several methods to prevent and eliminate material build-up and improve their flow throughout the cement production process.
Standard Industrie International, a specialist in handling and cleaning equipment for the bulk industry, has been working with major cement groups on this issue for many years. The experts of this French company, which has an international presence, explain here how accumulations and blockages can be treated in different areas of the cement plant, thus improving productivity and plant safety.
1- Eliminate accumulations in the preheating tower and the snowman effect in the clinker cooler.
These problems are frequent and must be avoided to guarantee a stable and regular clinker production.
In this context, Standard Industrie International provides its customers with a complete range of AIRCHOC® air cannons. This includes both preheating towers and coolers. The AIRCHOC® head design is made of cast steel with an iridescent zinc coating specially dedicated to resist high temperature environments.
A sequenced air blaster firing schedule will guarantee the elimination of clogging risks and ensure constant production without stoppages.
CUCTOMER CASE : LOMA NEGRA, Zapala plant (part of the Brazilian group INTERCEMENT) in Argentina
This cement plant equipped its tower of preheating with 11 AIRCHOC® air cannons in order to eliminate the concretions and to avoid the manual ringing.
They will be installed in the riser duct during the next kiln shutdown programed in August 2022 in addition to the 18 AIRCHOC® acquired (12 air cannons in July 2018 and 6 air cannons in May 2019) installed in the kiln inlet, smoke chamber and cylcones. This site, which has a 760 t/d 1970 KHD production furnace, uses 80% gas and 20% fuel oil. The AIRCHOC® air cannons are very effective on this type of installation.
2- Avoid the accumulation of material in the smoke box and avoid the slowing down of the gas speed.
This area is key and keeping it free of build-up facilitates gas circulation. Here is an example of an installation of 5 MACSYS® in wireless version.
The MACSYS® is a specific type of air cannon which has several heads connected to the same tank. For this application, all twenty heads are equipped with anti-vibration compensating sleeves. Each sleeve is then connected to the smoke box by a network of tubes. At the end of each fixed tube termination are deflectors, each with its own particularities depending on the cleaning job required.
Jérémie FRELIEZ, Head of the design office at Standard Industrie International, comments on the particularities of this installation:
"The objective is to easily reach the corners to improve cleaning by positioning five MACSYS® on four different levels. The wireless solution has enabled us to make significant savings on the cost of cables and cable trays.
It takes an average of 2 to 3 minutes to fill the two hundred liter tank at six bar, which allows for short firing rates. The direct result is an improvement in the quality of the cement as well as the production rate. Following this installation and its efficiency, the customer also equipped the cooler.
The MACSYS® Wireless is driven by the same control panel which allows to manage up to one hundred and twenty-eight AIRCHOC® air cannons."
3- Prevent concretions in material storage silos.
Clogging of material in silos results in a loss of productivity but also an increased risk for maintenance personnel. In addition, if a blockage breaks loose, it can cause damage by falling out. The production flow can be interrupted.
AIRCHOC® air cannons are installed on silos to stop existing blockages, to prevent new ones from forming and, consequently, to reduce or eliminate cleaning interventions. This is particularly the case for limestone, pozzolan, clay and lime hoppers, and at the end of the process for clinker, cement and ash recovery silos.
4- Limit the risks of fouling related to the use of alternative fuels throughout the cement production process.
Today, the vast majority of cement plants have increased the use of alternative fuels, biomass and various wastes to feed their kilns. The cost of these fuels, which are cheaper than the "raw materials", their abundance on the local market, the reduction of CO2 emissions, the preservation of resources, and the high thermal efficiency of these fuels, have made fossil fuels obsolete.
Today, the use of alternative fuels has pushed Standard Industrie to adapt and offer different air cannon systems to solve these new clogging problems. Standard Industrie provides a technical response adapted to the evolution of technologies. Burning only coal or burning various alternative fuels are very different processes.
Benoît PLUCHON, Export Sales Manager at Standard Industrie International, shares his experience:
"Our experts have observed over the past 15 years that the use of alternative fuels changes the nature of fouling. Indeed, the sulfur content is generally higher than before, when his customers burned 100% fossil fuels. We studied the process stability and operation of the cement kiln, including the build-up of material in the cyclones or other areas of the process, and concluded that the usual clogs are stickier and stronger with the use of alternative fuels."
In order to maintain the efficiency of the air cannon installation and to avoid producing "Christmas tree installations" (a large quantity of cannons installed in the preheating tower), Standard Industrie optimized the efficiency of its air cannon to have more impact on clogging.
David FREGEZ, Product Manager at Standard Industrie International for over 15 years, explains:
"For more than 5 years now, Standard Industrie has been suggesting to its customers to change their mind about the size of mechanical devices. Previously, for a process that burns a very large majority of fossil fuels, the technical study and the offer were proposed with an AIRCHOC® with an outlet diameter of 100mm (4"). In making a comparison, we found that using such a diameter was less effective when our customers were using a mix of fossil and alternative fuels. The impact force generated was not sufficient and the increased firing sequence was not really effective over time. Moreover, it involved additional maintenance with additional costs and loss of valuable time. The gradual switch to 150mm (6") heads are known to be very effective and economical."
5- Clean the cement storage silos
Cement storage in large concrete silos is not immune to clogging. Some plants choose to install cleaning systems such as AIRCHOC® air cannons and others choose to manually clean their silos periodically, when the extractions are blocked and the product is stuck on the walls.
Cyril PARISOT, Manager of the "Cleaning Services" department at Standard Industrie International, explains:
"Different methods exist, such as fluidization nozzles, vibrators, rope access or explosions, but these are not the most effective or safest solutions.
The GIRONET, on the other hand, is the safest cleaning solution on the market to obtain a very satisfactory result. It is a machine that must be positioned on top of the silo. An articulated arm slides inside and the motor, controlled from the outside, drives a series of tools to clean the entire storage unit. Customers who choose this method regain near original storage capacity. Standard Industrie International's intervention team restores the full capacity of the silo without human intervention inside, and what is important is that this eliminates any risk of accident. The GIRONET exists in an ATEX version, but apart from this latest evolution, it is the equipment that has undergone the fewest changes in our company, as it has proven itself after numerous performances. Our teams intervene 10 months of the year for the maintenance of the storage units or to troubleshoot in case of complete blockage".
CUSTOMER CASE : CALCIA Beaucaire in France
Because of humidity, the cement silo clogged and created a bridge, so extraction was no longer possible. Only an intervention of STANDARD INDUSTRIE Team made the silo operational and safe, without operators in the silo.
How does this type of intervention work?
In case the plant faces reduced collection capacity, the use of the pneumatic GIRONET, proposed by Standard Industrie International, will help to clean the silos and allow to get the whole storage capacity back.
The articulated arm of the GIRONET which rotates at 360° eliminates the rat holing problems. This solution meets stringent safety standards: It avoids having any human presence inside silos. The GIRONET intervention will enable to increase the capacity of collection in order to avoid supply disruptions. The GIRONET is effective on any type of blockage, product or storage unit. It can be used without stopping production.
Also, declogging with the POWERNET will solve bridging problems through safe breaking down of the clogged material to help it flow more freely. The POWERNET is used before the GIRONET when the storage unit is completely blocked. Idea of the POWERNET is to create a chimney through which the GIRONET will be use to sag down the build-ups.
The environment, safety and profitability are at the heart of every industry; there are many short- and medium-term alternatives on the market. Standard Industrie International, which is deeply involved in the cement industry, has chosen to offer the largest international groups quality products that combine advanced technology with a response adapted to productivity issues.