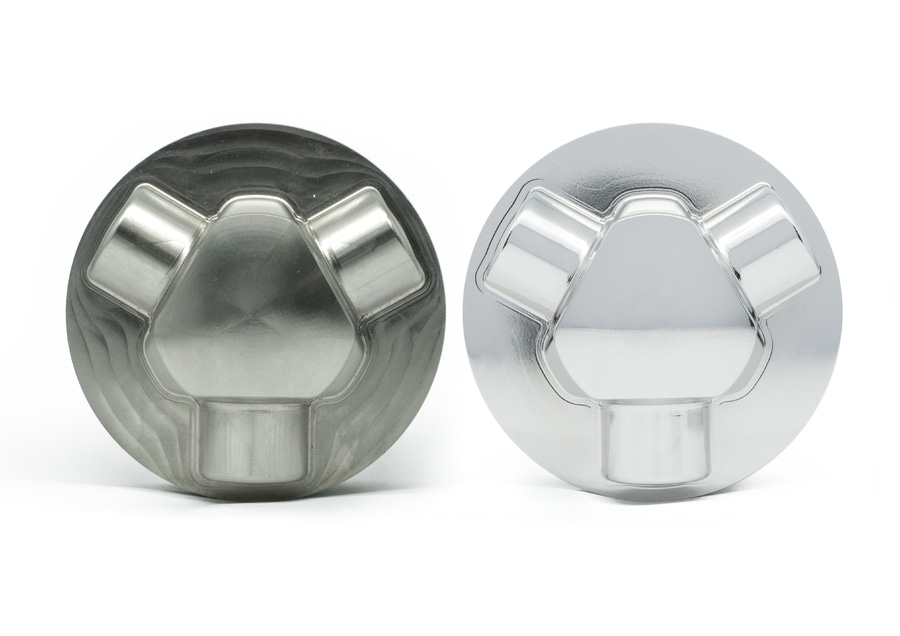
#Product Trends
Innovation in electropolishing:
Greater selectivity and definition with DryLyte dry electropolishing
In recent years, the interest for dry electropolishing has increased due to its excellent finishing quality, ease of use,
biocompatibility, corrosion resistance, fatigue life, and resistance to erosion and premature aging, amongst other
features.
From the first patent for classic electropolishing through the revolutionary new process of dry electropolishing, the
basic chemical process has not changed. Electropolishing is a specific type of electrolysis that involves a direct
electrical current that passes through an electrolyte in an electrolytic cell. The piece of metal to be polished serves
as an anode, connected to a positive terminal of a direct current power supply, with the negative terminal connected
to a cathode. The piece and the cathode are immersed in an electrolytic medium, Fig.1. Activating the power supply
produces an electrical current that goes through the anode to the cathode, which results in oxidation on the metallic
surface. These oxides that are formed are then dissolved, which eliminates the material on the surface and produces a
smooth and polished effect.
With the innovation of the new patented DryLyte process, for the first time in more than 85 years, the electrolytic medium is no longer a dissolution of concentrated acids. Instead, in the DryLyte process, the liquid acids are replaced with a set of tiny solid spheres with the capacity to conduct electricity.
CONVENTIONAL ELECTROPOLISHING
In classic electropolishing, the liquid acid solution contacts with both peaks and valleys of roughness, so it produces an
effect on the entire surface. The smoothing process occurs because 1) the peaks of roughness receive more electricity,
therefore they oxidize more and 2) the dissolution of oxides in the valleys is limited because of a lower diffusion rate.
Both effects are gradual, and do not produce a complete differentiation between roughness peaks and valleys. To
reduce the difference between the peaks and valleys to create a smooth surface, it is necessary to dissolve a quantity
of metal much higher than the theoretical minimum. Since the borders, edges and geometric vertices of the part
receive more electricity, this is where excessive variations in dimensions can occur, especially for applications requiring
precision or sharp edges. This creates a lack of efficiency since part of the energy, current and time is wasted in
extracting material of roughness valleys, without causing a decrease in overall surface roughness.
DRY ELECTROPOLISHING DryLyte
The DryLyte electropolishing process was introduced to overcome the limitations of classic electropolishing, and to
bring improvements to the process. This is a new patented technology based on a set of solid electrolyte particles with
the ability to conduct electricity and to remove the oxides produced during the electropolishing process. Unlike
traditional polishing systems, the DryLyte system obtains a uniform finish avoiding marks on the surface, patterns like
those generated by machining, and is capable of processing complex geometries without generating micro scratches on the surface.
In addition to surface uniformity, the DryLyte process offers a wide range of other benefits over traditional liquid electropolishing. These include increased corrosion resistance, fatigue resistance, resistance to erosion and premature aging, excellent biocompatibility, and improved adherence of subsequent coatings. All of this is achieved in a more environmentally friendly way while reducing the number of processes and therefore the total polishing time.
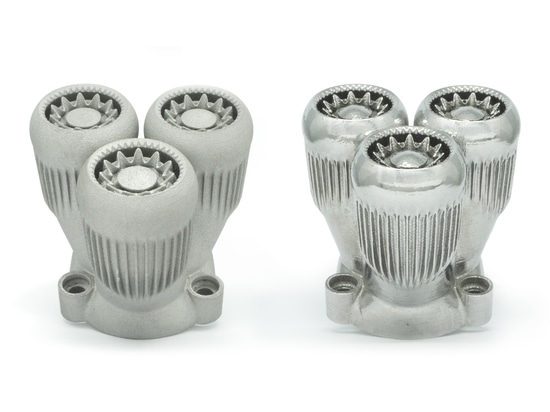