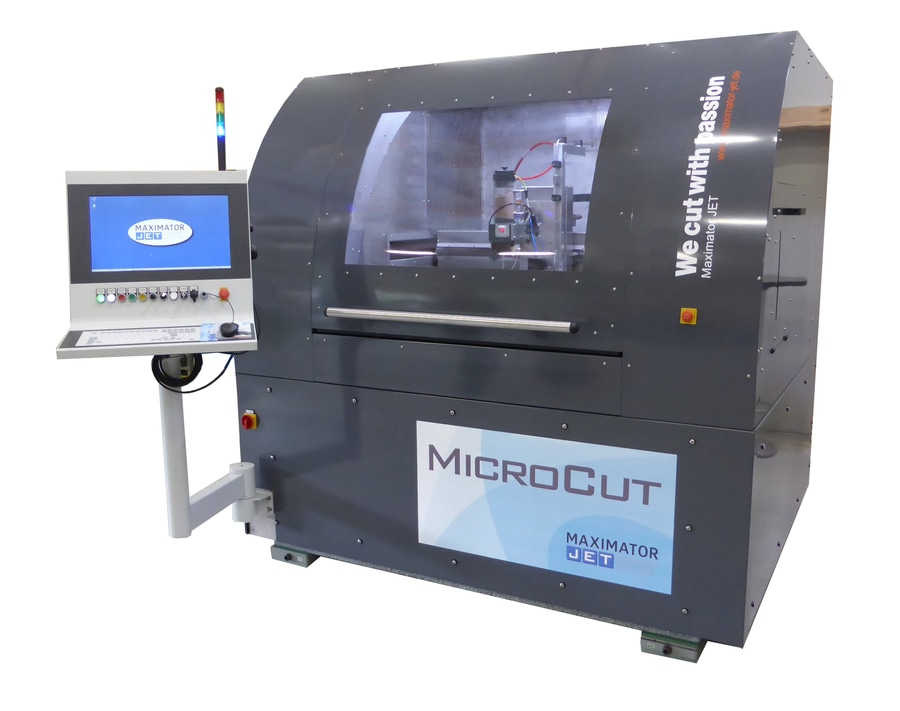
#Product Trends
Micro waterjet cutting more precise and efficient than ever – Maximator JET celebrates its new MicroCut V2
The German pioneer in precision waterjet cutting now offers an efficient solution to address the continuing miniaturization in industrial production
Schweinfurt, Germany. The technological evolution is proceeding ever faster across industries, providing new challenges also for the manufacturing sector. One such challenge includes the increasingly smaller and lighter components, requiring a degree of precision in manufacturing that traditional separation methods are unable to meet. In addition, more and more materials are sensitive to heat, which curbs the use of thermal cutting methods such as laser. But then there is waterjet technology, which in competition to methods like wire EDM, micro milling or punching, has become the shooting star of the miniaturized components sector. This trend is set to intensify with the latest innovation from Maximator JET. With the new “MicroCut V2”, the German waterjet specialists were able to improve their record cutting accuracy even further to an impressive to 0.01 mm, which is half the value of what was achievable before. This is made possible through an innovative design with a low-vibration granite base, high-precision clamping frame and linear motor axes in combination with first-class cutting head technology and the manufacturer's own fully integrated SmartCut software. Unprecedented precision is only one of many advantages of this innovative solution. The “MicroCut V2” also works much more efficiently than conventional systems. The manufacturer has reduced the mechanical wearing parts to a minimum; the integrated control and integrated abrasive system make the usual ancillary equipment redundant; and the software promotes maximum material, staff and time savings. The modular system configuration ensures that every detail can be customized for highly specialized cutting tasks and that the system may be upgraded or converted at any time. Along with the fact that waterjet cutting allows users to cut all kinds of materials without retooling, Maximator JET's “MicroCut V2” offers prime conditions for sustainably competitive production processes in particular in the fields of medical and electrical technologies. This is also recognized by the Physikalisch-Technische Bundesanstalt (PTB) Braunschweig which is putting the first system into operation in April 2016. The “MicroCut V2” was officially launched during the Innovation Days in the waterjet centre Schweinfurt, Germany, on the 17th June 2016. Interested parties can now register for this waterjet trends forum on www.maximator-jet.de.
Waterjet technology is a cold cutting process which cuts intricate, advanced workpieces made of various materials that would bend or melt with other methods. These include ceramics, glass, plastics, non-ferrous metals, electronic components and composites which are processed in form of minute parts in the mechanical engineering, electronics, automotive, chemicals, jewellery, watch, food, medical technology and other sectors. Micro waterjet systems are ten times more accurate than traditional systems. This is particularly true for the new “MicroCut V2” which cuts abrasively with a minimum diameter of 0.3 mm and a positioning accuracy and repeatability of 0.0025 mm, where the abrasive share can be continuously adapted to any surface and cutting task. The surface quality of up to Ra = 0.8 µm resembles grinding. Machining sequencing as well as start and end points can be chosen almost at will. The small tool diameter ensures sharp contours with a high cutting and cutting edge quality and – thanks to the jet diameter of <0.3 mm – extremely high material efficiency. Process forces and thermal loads are minimal, and no toxic gases are emitted. The system is fully enclosed and built on a low-vibration granite base. This is connected to a variable high-precision clamping frame which aligns and securely fastens workpieces with an accuracy of up to 700 mm x 500 mm. Guide units with highly dynamic linear motor drives guarantee first-class performance and precision and eliminate the need for costly wearing components such as couplings, gears and transmissions. The new control panel with the reliable SmartTouch system, the integrated control via intelligent SmartCut CAD/CAM software and special protectors against dirt and noise ensure maximum user-friendliness. The thermally and physically separated stainless steel water tank and the exclusive use of branded components guarantee smooth cutting and high wear resistance. These advantages allow a virtually fully automated production environment with the highest possible degree of precision, minimal labour, material and time investment. In short, the “MicroCut V2” shows imagination and opens up interesting prospects in the processing of materials of the latest generation. The ready-to-use system can now be purchased starting at €180,000 (without high-pressure pump), and all accessories are also available.
Those interested can check out the performance of the Maximator JET fine waterjet systems at any time based on individual test cuts or during a demonstration in the brand new waterjet centre in Schweinfurt. You can also request a free, customized system proposal including cost-benefit analysis to help you to accurately judge the suitability of a “MicroCut V2” waterjet cutting system.
Maximator JET GmbH is a pan-European innovator in the high performance segment of the waterjet cutting industry. The Schweinfurt company has been focussing on developing and implementing highly specialised waterjet cutting systems for all kinds of special applications since 1999. The company stands for future-oriented manufacturing solutions and customisation options without limits. For this purpose and thanks to their exemplary quality and reliability, Maximator JET works exclusively with series systems from STM. The Maximator JET range of products and services includes 2D and 3D cutting systems from its own production facilities as well as standard systems from their Austrian system partner, high-pressure pumps up to 6,200 bar, high-pressure components, operating materials as well as comprehensive support and maintenance services.