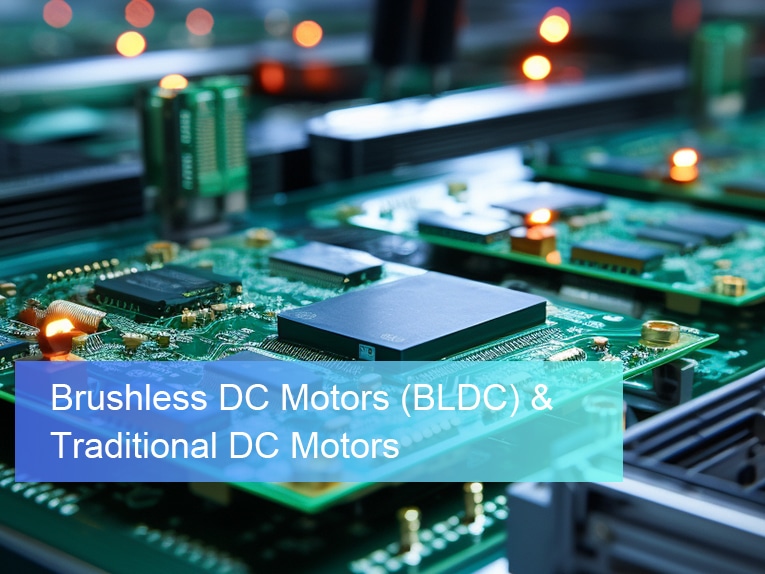
#Product Trends
The Difference Between Brushless DC Motors (BLDC) and Traditional DC Motors
Brushless DC Motors VS Traditional DC Motors
With continuous technological advancements, brushless DC motors (BLDC) have rapidly gained market share due to their efficiency and long lifespan. Compared to traditional DC motors, BLDC motors offer significant improvements in performance and reliability. As a company specializing in the manufacturing of efficient electronic solutions, TecoO is committed to providing motor control systems for the home appliance industry. In this article, we will explore the key differences between BLDC motors and traditional DC motors.
1. Difference in Operating Principles:
Traditional DC Motors: These motors rely on mechanical brushes and a commutator to conduct current and drive the rotor. While this design enables the motor to function, the friction between the brushes and the commutator results in component wear, which reduces efficiency and requires regular replacement and maintenance.
BLDC Motors: Instead of mechanical brushes and a commutator, BLDC motors use electronic commutation. An electronic controller senses the rotor's position and adjusts the current flow without physical contact, eliminating mechanical wear. This design not only extends the motor's lifespan but also enhances its reliability.
2. Performance:
Traditional DC Motors: Traditional DC motors have performance limitations. The frictional losses caused by the brushes affect efficiency, and heat and mechanical wear can further degrade performance. Additionally, these motors struggle with precise speed control and torque at low speeds, making them less suitable for applications that require high performance and flexibility.
BLDC Motors: BLDC motors stand out for their high efficiency and precise control. Without the frictional losses from brushes, they maintain high efficiency, even under heavy loads. Their superior performance is especially noticeable at low speeds, where they outperform traditional DC motors.
3. Maintenance and Lifespan:
Traditional DC Motors: These motors require regular maintenance, particularly the replacement of brushes and commutators. This increases equipment downtime and long-term maintenance costs. In high-load and frequently used applications, maintenance needs can become more frequent, leading to production delays and additional expenses.
BLDC Motors: With fewer parts subject to wear, BLDC motors generally have a longer lifespan and require little maintenance. In applications that demand continuous and reliable operation, such as home appliances and industrial automation, the low maintenance requirements of BLDC motors significantly reduce overall costs.
4. Noise and Heat Management:
Traditional DC Motors: The operation of the brushes and commutator often generates considerable noise. Additionally, traditional DC motors can overheat under heavy loads, requiring additional cooling systems or ventilation to maintain normal operating temperatures. This increases both the complexity and cost of operation and maintenance.
BLDC Motors: BLDC motors are much quieter during operation, as they lack the mechanical friction caused by brushes and a commutator. This is especially beneficial in noise-sensitive applications such as air conditioners, fans, and medical devices. Additionally, BLDC motors generate less heat than traditional DC motors, often eliminating the need for complex cooling systems, which further improves energy efficiency.
5. Applications:
Traditional DC Motors: Due to their relatively simple design and lower initial cost, traditional DC motors are still used in devices with low performance and longevity requirements, such as small tools, toys, and some short-term consumer products. These applications are not sensitive to high efficiency or low maintenance, so traditional DC motors maintain a cost advantage in these areas.
BLDC Motors: As BLDC motor technology continues to evolve, they are being adopted in a wide range of industries. With advantages such as high efficiency, low noise, and long lifespan, BLDC motors are widely used in various applications, ranging from consumer electronics and large equipment to automation systems and industrial devices.
6. Cost:
Traditional DC Motors: The initial cost of traditional DC motors is generally lower, making them suitable for applications with limited budgets or lower performance requirements. However, frequent maintenance and the need for component replacement (such as brushes and commutators) drive up long-term costs, making them less ideal for continuous, high-load operation.
BLDC Motors: While BLDC motors typically have a higher upfront cost, their low maintenance needs, long lifespan, and high efficiency make them more suitable for equipment requiring long-term, efficient operation. For applications requiring continuous and reliable performance, BLDC motors offer a higher return on investment.
In conclusion, BLDC motors are becoming the preferred choice across various industries due to their efficiency, reliability, and low maintenance characteristics. At TecoO, we specialize in the research, development, and manufacturing of high-performance BLDC motor solutions tailored to meet the demands of a wide range of applications. Whether it's home appliances, industrial automation, or other complex scenarios, TecoO is your trusted partner in delivering superior motor control solutions.