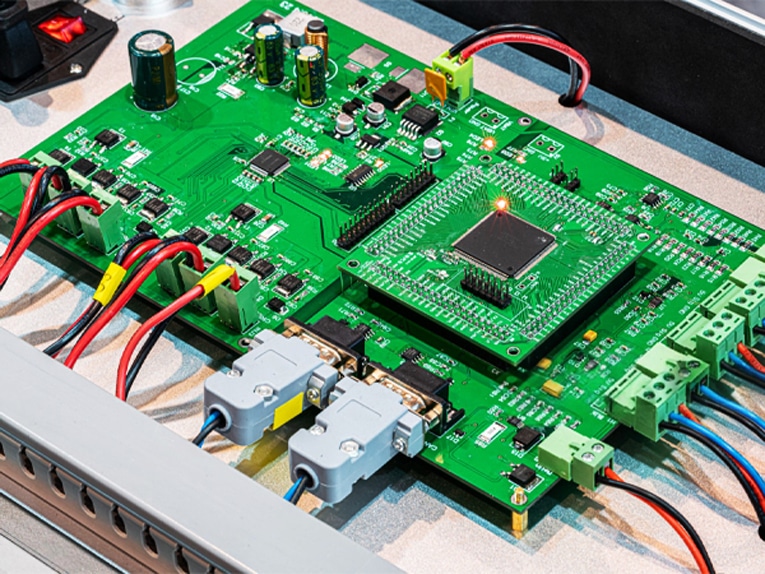
#Industry News
Key Performance Parameters Of Servo Drive Board And Their Impact
Impact of Key Performance Parameters on Servo Drive Board Functionality
Power: The power of the servo driver board determines its ability to drive the motor. The greater the power, the greater the motor power that can be driven, and the greater the load that can be driven. In large industrial equipment, such as heavy CNC machine tools and large automated production lines, since the motor needs to output a large torque to drive a heavy workbench or robotic arm, a high-power servo driver board is required to ensure that the motor can stably output sufficient power during startup, acceleration, operation and braking, and avoid problems such as motor stalling and unstable operation caused by insufficient power.
Voltage: The input voltage is the basis for the normal operation of the servo driver board. Different types of servo driver boards are adapted to different voltage levels, such as the common 220V, 380V, etc. The stability of the voltage directly affects the performance of the driver board. If the input voltage fluctuates too much, it may cause abnormal operation of the electronic components inside the driver board, such as overheating of the power module and malfunction of the control chip. In some areas where the quality of the power grid is unstable, voltage stabilization equipment is required to ensure the stability of the input voltage of the servo driver board. At the same time, appropriate voltage matching can make the driver board run efficiently and reduce energy consumption.
Current: The current parameter reflects the working current provided by the driver board to the motor. During the operation of the motor, the required current will change according to the load. The servo driver board needs to have the ability to adjust the current in real time to meet the needs of the motor under different working conditions. When the motor starts or is overloaded, a larger current is required to provide sufficient torque. If the current output capacity of the driver board is insufficient, the motor will not start normally or will jam during operation. When the motor is running under light load, the driver board should be able to automatically reduce the current output to improve efficiency and energy saving. In application scenarios such as robot joint drive, the motor needs to start and stop frequently and respond quickly, which requires the servo driver board to accurately control the current to ensure the agility and accuracy of the robot's movements.
Speed control accuracy: This parameter reflects the servo driver board's ability to control the motor speed. High-precision speed control can ensure that the motor maintains a stable speed during operation with minimal error. In industries such as textile machinery and printing equipment that have extremely high requirements for speed stability, the high speed control accuracy of the servo driver board is crucial. For example, in the spinning process of a textile machine, if the motor speed is unstable, the yarn thickness will be uneven, affecting product quality.
Torque response time: Torque response time refers to the time interval from when the servo driver board receives the control signal to when the motor outputs the corresponding torque. The shorter the response time, the faster the motor responds to the control command. In some application scenarios that require fast start and stop and frequent acceleration and deceleration, such as automated sorting equipment and high-speed punching machines, short torque response time can enable the equipment to quickly reach the required operating state and improve production efficiency. If the torque response time is too long, the equipment will have obvious delays when starting and braking, affecting the overall operation effect.
Position control accuracy: For applications that require precise control of the motor position, such as coordinate axis positioning of CNC machine tools and operation of automated assembly robots, the position control accuracy of the servo driver board plays a decisive role. High-precision position control can ensure that the motor stops accurately at the specified position, and the error can be controlled within a very small range. In chip manufacturing equipment, the motor position control accuracy is required to reach the micron or even nanometer level. Only in this way can the accuracy of processes such as lithography and etching in the chip manufacturing process be guaranteed.