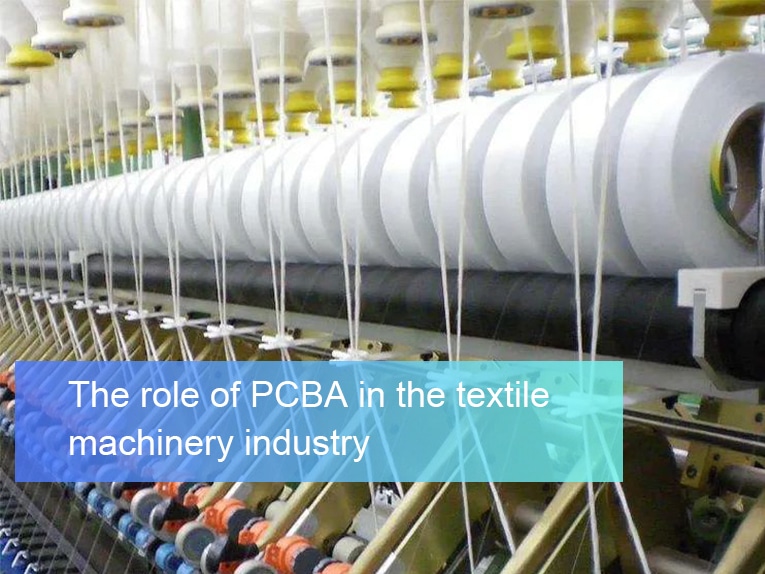
#Industry News
The role of PCBA in the textile machinery industry
The role of printed circuit board assembly in the textile machinery industry
The application of PCBA (Printed Circuit Board Assembly) in the textile machinery industry is mainly reflected in improving the intelligence and automation level of equipment and enhancing the stability and reliability of equipment.
Application of PCBA in the textile machinery industry
1. Improving equipment intelligence:
Control system: The control system in textile machinery mostly adopts PCBA technology, and integrates various sensors, microprocessors, actuators and other components to achieve real-time monitoring and precise control of the operating status of textile machinery. For example, in spinning machinery, the variable frequency speed regulation system controlled by PCBA can automatically adjust the speed of the motor according to the quality and process requirements of the yarn, so as to achieve energy saving and consumption reduction and the purpose of improving production efficiency.
Remote monitoring and operation and maintenance: Through the wireless communication module integrated in PCBA, textile machinery can access the Internet to achieve remote monitoring and operation and maintenance. Managers can view the operating status, production data, etc. of the equipment in real time through computers or mobile devices in offices far away from the production site, and can perform fault diagnosis and remote debugging, which greatly improves the operation and maintenance efficiency.
2. Enhance equipment automation:
Automated production line: On the production line of textile machinery, PCBA technology is widely used in the control system of automated equipment. By precisely controlling the actions of each actuator, the production line can be operated automatically. For example, in weaving machinery, the quality and production efficiency of fabrics can be ensured by automatic warp feeding, automatic winding and other systems controlled by PCBA.
Intelligent detection and identification: PCBA can also integrate various intelligent detection and identification technologies, such as machine vision, infrared sensing, etc., to monitor and identify the operating status and product quality of textile machinery in real time. Once an abnormal situation or defective product is found, an alarm or shutdown can be immediately processed to avoid the expansion of faults or product quality problems.
3. Improve equipment stability and reliability:
Efficient heat dissipation: Textile machinery will generate a lot of heat during operation. If the heat dissipation is poor, it will affect the stability and reliability of the equipment. PCBA can effectively improve the heat dissipation performance of the equipment by optimizing the PCB layout and using efficient heat dissipation materials, ensuring that the equipment can operate stably in high temperature environments.
Protective design: PCBA also has good protective design, such as dustproof, waterproof, and corrosion-resistant, which can ensure that the equipment can work normally in harsh environments. At the same time, the stability and reliability of the equipment can be further improved by using high-quality electronic components and strict manufacturing processes.
Application Cases
During the equipment transformation process, an international textile machinery group carried out energy-saving transformation on the spinning equipment in order to improve the intelligence and automation level of the equipment. The group adopted PCBA products such as frequency conversion control boards provided by Tecoo Electronics. Through the application of the frequency conversion speed regulation system, not only the precise control of the spinning machine is achieved, but also the energy consumption and noise are reduced, and the product quality and production efficiency are improved. The specific effects include:
Energy saving and consumption reduction: Through the application of frequency conversion speed regulation technology, the energy consumption of the spinning machine is reduced by more than 30%.
Improving production efficiency: The overall speed of the spinning machine has increased by nearly 10%, and the output has increased by nearly 10%.
Reducing production costs: Due to the reduction of yarn breakage and yarn defects, the rework and waste of labor hours and raw material costs are reduced.
Improving product quality: Through precise speed change and process adjustment, the quality and stability of textiles are improved.
The application of PCBA in the textile machinery industry is of great significance to improving the intelligence and automation level of equipment and enhancing the stability and reliability of equipment. With the continuous advancement of technology and the deepening of application, the application prospects of PCBA in the textile machinery industry will be broader.