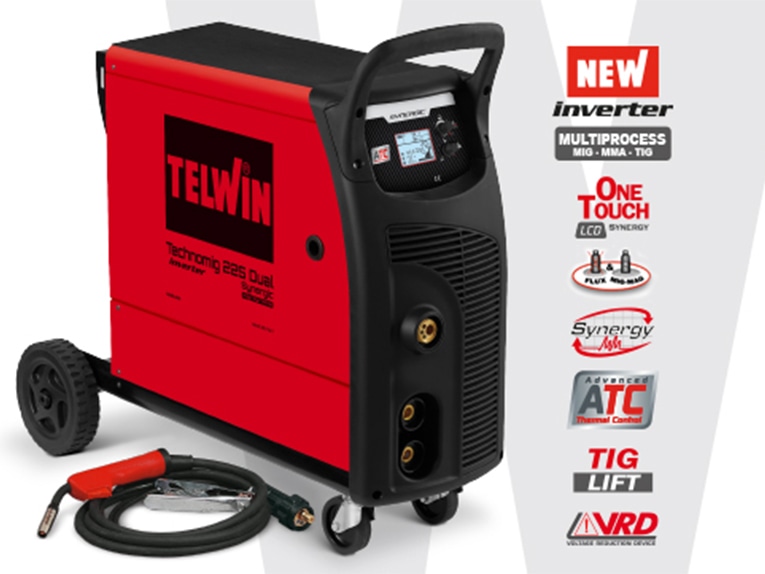
#Industry News
TECHNOMIG 225 DUAL SYNERGIC
WIDER CHOICE IN THE WORLD OF TECHNOMIG!
Technomig 225 Dual Synergic is a 220A, MIG-MAG/FLUX/BRAZING/MMA/TIG DC-Lift inverter, multiprocess welding machine, flexible and intuitive to use thanks to One Touch technology. The novelty of this model is the presence of wheels that allow it to be moved where necessary.
Technomig 225 Dual Synergic also stands out for its extreme versatility: it is able to work on different thicknesses and welded and brazed materials, making it the ideal tool for use in many fields of application, from maintenance to metal sheet works and bodyshops.
MORE FLEXIBILITY IN USE
Technomig 225 Dual Synergic is ideal for MIG-MAG operation but can work also with flux-cored wire, electrode and as TIG-Lift, making it suitable for a variety of applications.
MORE PRODUCTIVITY WITH ONE TOUCH TECHNOLOGY
Setting up the Technomig 225 Dual Synergic is simple and straightforward: simply set the material thickness and start welding. The 27 synergic curves for different gases and materials allow for quality welds on Steel, Stainless Steel, Aluminium and Galvanised sheets without wasting time setting up the machine.
MORE QUALITY WITH ADVANCED SETTINGS
> Tailored programs for welding on thin thicknesses (ATC), and to get best performances on Aluminium, Galvanised Sheets and Stainless Steel.
> Possibility of manual intervention on the arc length to modify the shape of the weld bead according to the style and preferences of the operator.
> Adjustment of several advanced settings such as: wire slope up, electronic reactance, wire burn back time, post gas time and selection of 2/4 time and spot operation.
MORE CONTROL WITH PARAMETERS ALWAYS IN EVIDENCE
The LCD screen allows you to keep the voltage, current and welding speed parameters under control any time, so you can see how your work is progressing.
VRD DEVICE FOR GREATER SAFETY
Thanks to the VRD device (Voltage Reduction Device) welding is safe, even in damp environments or with water present.
The VRD device reduces voltage output to a safe level when the welding machine is on but not in welding conditions, guaranteeing the safety of the operator who may come in contact with the electrode risk-free until welding starts again (mines, shipyards, etc.).