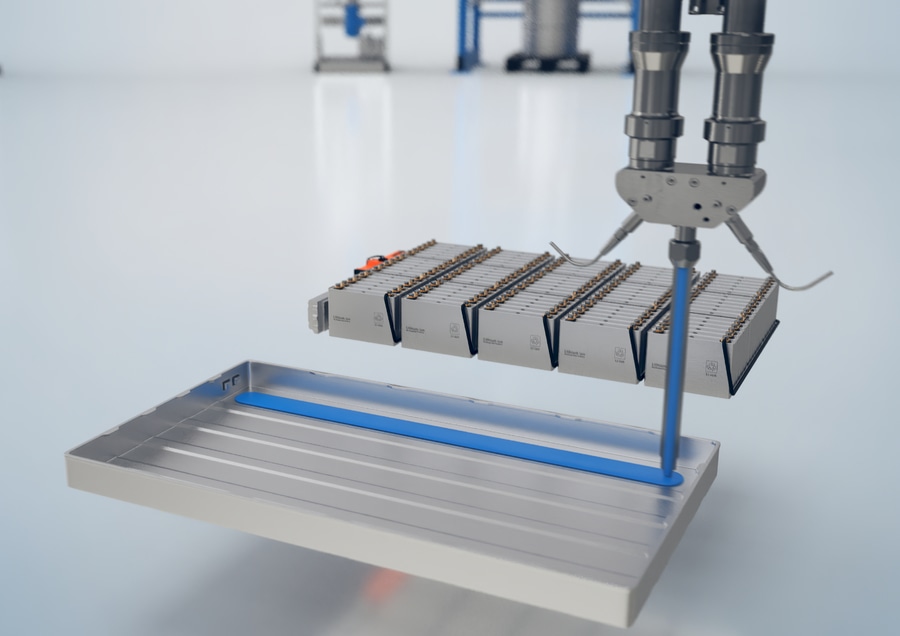
#Industry News
Thermal management – dispensing of liquid TIM and gap filler
Automated solutions for electronic components and battery cell assembly
The application and injection of TIMS or gap fillers on and into battery modules or electronic components requires an absolutely process-safe handling of 1- or 2-component materials. Precise, fully automated, easily adjustable, and endless dosing is the prerequisite. ViscoTec dispensing systems enable exactly that: Continuous, repeatable, and material-friendly dispensing of TIMs, gap fillers, sealing materials and adhesives – regardless of their viscosity. A specially developed ceramic rotor ensures long service life, even when using highly abrasive materials. For example, a long-term test with a 2-component gap filler, with aluminum-oxide fillers, showed a 9-fold service life compared to the standard rotor.
Learn more about this in the video and in the further text below: https://youtu.be/NidHtfUdFMI
Example battery cell assembly
High-voltage battery cells must be operated within a certain temperature range to maintain their performance and prevent overheating. However, thermal influences can affect the performance and safety of a HV battery and the connected components. Therefore, reliable thermal management is required for long-term operation at a high efficiency level – a heat-conducting paste is applied for this purpose. To ensure optimum heat dissipation between battery modules and housings, the materials used for this purpose are highly filled. These are usually 1-component or 2-component silicones or silicone-free materials such as acrylates.
These highly filled materials must be dosed without bubbles. Only then optimum thermal conductivity can be guaranteed. However, implementation is made more difficult because the liquid gap-filling material is applied in large quantities. In addition, the material is very abrasive, and the dosing system can wear out quickly.
In most applications the challenges are solved by high flow rates; by using the wear-resistant ceramic rotor. By using a material treatment system sedimentation of fillers can also be prevented. To improve the flow behavior, additional heating of the materials or processing equipment may be required.
Advantages of the ViscoTec dosing technology
Dispensing systems based on the endless piston principle are convincing due to their high-precision dosing of one- and two-component thermal conductive pastes – even with extreme mixing ratios of the latter. A repeatable dosing of the filled and highly abrasive materials takes place without loading time. Fillers retain their properties because they are only exposed to low shear stress thanks to the low-pressure system. Long service lives can be achieved by selecting suitable materials for the dosing components.