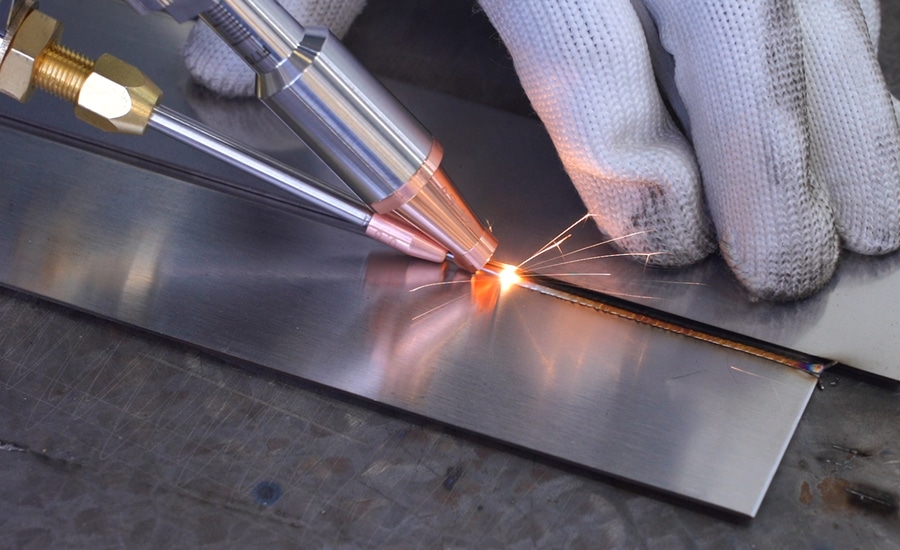
#Industry News
The Advantages of Laser Welding Over Traditional TIG Welding
Laser Welding advantages
Welding is an essential process in various industries, from automotive to aerospace. As technology advances, so do the methods used to join materials. Laser welding has emerged as a superior alternative to traditional Tungsten Inert Gas (TIG) welding, offering a range of benefits that enhance quality, efficiency, and precision.
Precision and Accuracy
Laser welding utilizes a highly focused beam of light to melt materials, allowing for extremely precise control over the weld area. This precision is unmatched by TIG welding, which relies on a tungsten electrode and an inert shielding gas. The accuracy of laser welding is particularly beneficial for intricate parts and delicate materials where a small weld pool is required.
Speed and Efficiency
The speed at which laser welding can be performed is significantly faster than TIG welding. The high energy density of the laser beam allows for rapid melting and solidification, which translates to shorter welding times. This increased speed not only boosts productivity but also reduces the heat-affected zone, minimizing the risk of distortion.
Non-Contact Process
One of the key advantages of laser welding is its non-contact nature. Unlike TIG welding, which requires the electrode to be in close proximity to the workpiece, laser welding does not need physical contact. This eliminates the risk of contamination from the electrode and reduces the chance of damaging sensitive components.
Cover
Material Compatibility
Laser welding is versatile and can be used on a wide range of materials, including metals, plastics, and ceramics. This adaptability is a significant advantage over TIG welding, which may require different filler materials or settings for various types of metals.
Cleanliness and Quality
The cleanliness of the welding process is another area where laser welding excels. Since there is no physical contact and the process is automated, there is less chance of introducing contaminants into the weld. This results in a cleaner, higher quality weld with fewer defects.
Reduced Distortion
The localized heat input of laser welding minimizes the risk of distortion in the workpiece. This is particularly important for applications where maintaining the original shape and dimensions of the material is critical.
Automation and Integration
Laser welding systems are highly automatable, allowing for seamless integration into automated production lines. This automation not only improves consistency and repeatability but also reduces the need for skilled labor, making it an attractive option for industries looking to streamline their operations.
Conclusion
While TIG welding has been a reliable method for many years, laser welding offers a new level of precision, speed, and quality. As industries continue to demand higher standards and more efficient processes, laser welding stands out as a preferred choice for joining materials in a wide range of applications.