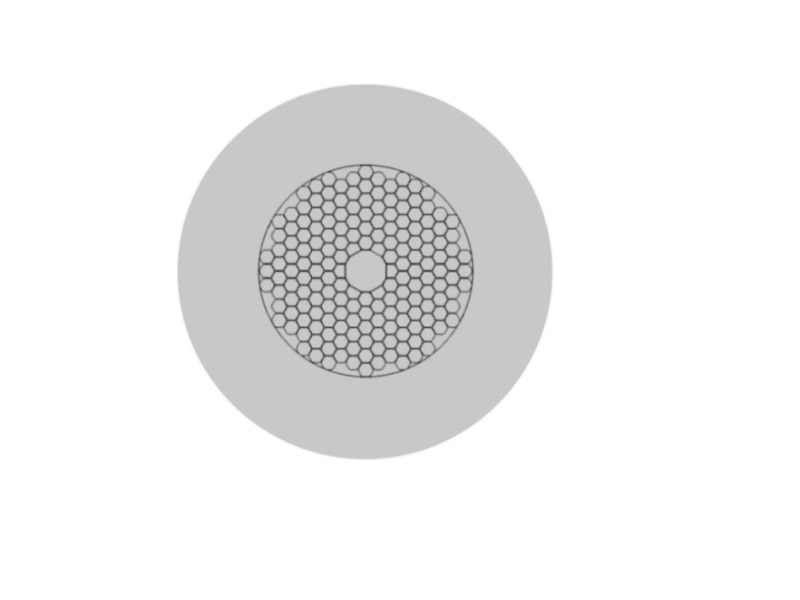
#Industry News
About Hollow-Core Fiber
About HC-PBGF
1. Hollow-core photonic crystal fiber
In 1987, E. Yablonovitch proposed that dielectric materials with different refractive indices are arranged periodically in one, two or three dimensions in an optical fiber, that is, the miniaturized glass capillaries are distributed in a periodic array, which can be used as a composite material to form an optical fiber cladding, and the fiber core is an air hole with a hollow structure, to realize low-loss optical guidance in the air core. The development source of the hollow-core photonic crystal fiber (HC-PCF) is as follows:
From 1995 to 1999, Scientists had launched the theoretical verification of the hollow-core photonic crystal fiber (HC−PCF), and then the hollow−core photonic crystal fibers of various structures emerged endlessly.
2. Classification of hollow-core photonic crystal fibers
Based on the principle of optical conduction, HC-PCF can be divided into two types of photonic crystal fibers: hollow-core bandgap fiber (HC-PBGF) and hollow-core anti-resonant fiber (HC-ARF).
1) Hollow-core bandgap fiber (HC-PBGF): It is based on the principle of photonic bandgap to guide light. The cladding is a photonic bandgap structure arranged in an array by periodic air holes. When the defective part in the center of the structure is air, the light with a wavelength within the bandgap range can be confined in the air core.
2) Hollow-core anti-resonant fiber (HC-ARF): Its light-guiding mechanism can be explained by the principle of anti-resonant reflected optical waveguide in a planar waveguide. Figure 4 shows the hollow-core anti-resonant fiber with a simple structure, and its cladding part is made of high-refractive-index quartz materials, and the black part is low-refractive-index air. The quartz capillary structure layer surrounding the air core around the fiber structure is the core part. This structure can make the light of a specific wavelength resonate to the outside of the cladding, and reflect the light that does not meet the resonance condition back to the air core, thereby confining the light in the air core, realizing an anti-resonant reflection light guide. The resonant wavelength depends on the thickness and resonant order of the quartz capillary.
3. Production process of hollow-core bandgap fiber
At present, the production of hollow-core bandgap fiber can be divided into the following4 steps:
① Draw the capillary with precise outer diameter according to the structural design, including the capillary of the cladding part and the central capillary, and arrange the capillary into a micro-structured capillary bundle;
② Insert the capillary bundle into the sleeve for assembly;
③ Draw the combination of the capillary bundle and the sleeve into a microstructure preform;
④ Draw the preform into the wire to form a hollow-core photonic crystal fiber.
4. Important applications of hollow-core bandgap fiber
Hollow-core bandgap fiber is mainly used in optical fiber communication, optical fiber sensing, and optical fiber lasers.
1) Optical fiber communication: The hollow-core bandgap photonic crystal fiber has the characteristics of low nonlinearity and low delay, can carry out long-wavelength transmission and has high-temperature phase stability. In addition, the low-loss transmission of light waves in the air core is an important characteristic of the hollow-core bandgap fiber. Therefore, in the development of optical communication systems, they are of great value as transmission media.
High capacity: The data transmission rate reaches 73.7Tb/s (3MDM × 96WDM × 256 Gb/s) through about 310m of hollow-core bandgap fiber. The net data rate is 57.6Tb/s.
Long distance: Hollow-core bandgap fiber can carry out long-distance data transmission at a rate of 50Gbit/s.
Low delay: 11km hollow-core bandgap fiber transmission, compared with traditional fiber, reduces the delay by about 16μs, and the bit error rate <1e°, which is equivalent to error-free transmission.
However, the loss of the hollow-core bandgap fiber will be limited by the scattering of the silica glass/air-core interface, and it is necessary to expand the bandwidth and reduce the loss to improve the competitiveness of the traditional communication fiber.
2) Fiber laser (energy transfer): High-energy short pulse transmission. High-energy short-pulse lasers can provide light pulses with a duration of sub picoseconds, a peak power higher than gigawatts, and a repetition frequency higher than MHz Because it can provide more high-precision micro-processing for various materials while minimizing the size of the heat affected zone, this technology is now widely used in the semiconductor industry, glass engraving, automobiles and plastic electronics; and used to perform complex and minor surgical operations, such as ophthalmology, dentistry or otology.
3)Optical fiber sensing: The low-loss transmission of light waves in the air core is an important characteristic of hollow-core bandgap fibers. It brings a long-distance, high-energy-density channel for the interaction between light and matter, and reduces the influence of fiber material properties on transmitted light (such as mid-infrared absorptiometer-optical effect), and provides an efficient new platform for sensing applications such as trace gas/liquid detection and high-precision fiber optic gyroscopes. The fine microstructure inside the hollow-core bandgap fiber has novel mechanical and thermal properties, which is conducive to sensing applications such as acoustic wave and vibration detection; it can also modify the structure or fill the material of the porous cladding by combining the technologies of optical fiber post heat. Treatment and selective filling, to obtain further performance and function expansion.
The sensitivity of the hollow-core bandgap fiber optic gyroscope to the Kerr effect, transient temperature drift and Faraday effect is greatly reduced. For a specific triangular wave phase modulated hollow-core bandgap fiber optic gyroscope, the Kerr effect is about 70 times smaller than that of ordinary single-mode fiber. This helps to improve the long-term stability of the gyroscope and the accuracy under various interference environments such as heat and magnetism, and further reduce the system cost.
5. Conclusion
With the continuous progress of hollow-core bandgap fiber manufacturing technology, its performance can be further improved in the following directions: (1) reducing loss and backscatter;(2) reducing the diameter of optical fiber;(3) more effective optical fiber joint fusion splicing technology;(4) expanding the transmission bandwidth. In application, with the improvement of the performance of hollow-core bandgap fibers, especially for systems with higher requirements in terms of nonlinearity and delay, the hollow-core bandgap fibers have become more and more attractive.