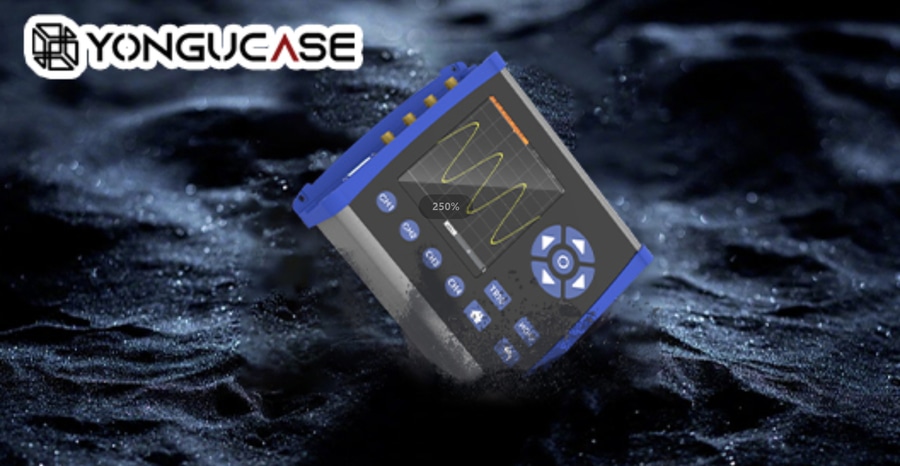
#Industry News
How to Set Correct Shielding for PCB Layers
yongu-group
Correct shielding method
In product development, from a cost, schedule, quality, and performance perspective, it is often best to carefully consider and implement the correct design early in the project development cycle. Add-ons and other "Quick" Fixes implemented late in the project are often not functionally non-ideal solutions, have poorer quality and reliability, and are more expensive than implemented earlier in the process. Lack of foresight in the early design stages of a project often results in delayed delivery and can lead to customer dissatisfaction with the product. This question applies to any design, be it analog, digital, electrical or mechanical, etc.
Compared to emi emc shielding a single ic and part of the pcb area, it costs about 10 times to shield the entire pcb and 100 times the cost to emi wire shielding the entire product. If an entire room or building needs to be circuit board shielding, the cost is truly astronomical.
The "Nested" Masking approach is one possible solution. A nested approach is a method of applying masking at every lowest level of product design. For example, masking is first applied to:
The nested shielding approach minimizes the overall cost of manufacturing a high-quality product on time and within performance specifications.
Use a low shielding level
Cable interference shielding at the lowest possible level (individual ic, small area of pcb, and pcb level) makes sense for a variety of reasons:
EMI shield box can help attenuate interference between individual ics located on the pcb, while pcb level shielding can help attenuate interference between individual ics
From a practical/cost-efficiency perspective, typical box shielding techniques cannot provide significant attenuation performance at higher (ghz) frequencies, whereas pcb shielding does.
The cost and weight of the shielding layer can be minimized by the effective use of the shielding on the pcb layer.
From a susceptibility point of view, modern integrated circuits have shrinking silicon characteristics, faster rise times, and lower noise margins. As long as rfi shielding tape is used at the pcb layer, they can work efficiently in noisy environments.
The integration of noisy wireless communication modules in products can lead to harmful inferences to other sensitive analog and digital components in close proximity. This noise can also be mitigated by using pcb level shielding
The EMC shield enclosure is often compromised to the point of complete failure due to the need to add holes and slots to penetrate input/output cables, displays, ventilation, contact removal media, etc. Whereas with pcb-level shielding, this is less of a problem. Yongucase has professional emc/emi electronic shielding electronic equipment enclosures, providing custom opening services, anodizing services, logo printing services, and custom size services. At the same time, there are multiple specifications in stock sizes, and conductive/non-conductive functions can be customized. Yongucase uses extruded aluminum profiles, which can efficiently use pcb shielding even if the holes are opened.
Effective enclosure shielding typically requires accurate filtering of all cables entering and leaving the product at the point where the cable passes through the enclosure shield. The need for this additional filtering can be reduced if a pcb level shield is used.
Whether designing cell phones, tablets, laptops, or other forms of electronics, in addition to pcb level shielding, good pcb layout is critical to minimizing emi. Ground and power planes can be used as emi shielding for high-threat noise signals, and this technique is a good first step toward minimizing noise in these high-threat signals. One problem with this approach is that rf energy is still radiated out of the component leads and package, so a more complete solution is required. A pcb level shield (also known as a "Shield can") can be used here to attenuate the noise emitted by these noisy devices.
To provide maximum benefit, the pcb horizontal shield must form a complete six-sided metal enclosure. This is accomplished by soldering the shield to a solid ground plane beneath all components that require aluminum foil emi shielding. To maximize efficacy, there must be no substantial gaps or openings in the ground plane. The actual performance of all shields and ground planes will always be affected by openings such as adjustment holes, indicators, wires, construction seams, and gaps between shielding electromagnetic fields can ground plane connections, so these items need to be avoided as much as possible.
The goal of EMI shielding is to use the six sides of a metal box to create a faraday cage around an enclosed rf noise component. The top five sides are made using rf shielding material caps or metal cans, while the bottom sides are implemented using ground planes within the pcb. In an ideal enclosure, no emissions would enter or leave the box. Hazardous emissions from these shields do occur, such as from perforations into holes in tin cans that allow heat transfer during solder reflow. These leaks can also be caused by defective emi gaskets or solder attachments. Noise may also escape from the space between the ground vias used to electrically connect the shield cover to the ground plane.
Traditionally, pcb shields are attached to the pcb using through-hole solder tails that are manually soldered after the main assembly process. This is a time-consuming and expensive process. If maintenance is required during installation and repair, desoldering is necessary to gain access to circuits and components under the emi cable shielding. In dense pcb areas containing highly sensitive components, there is a risk of costly damage.