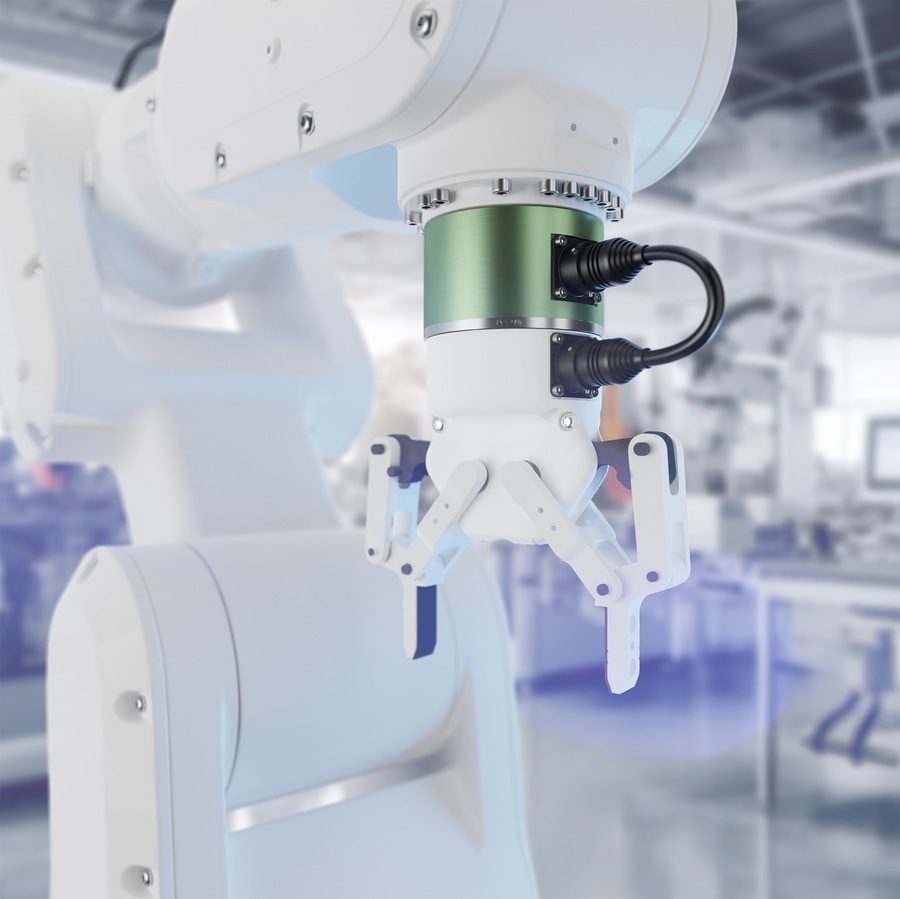
#Industry News
3D sensor for force and torque measurement
Force/torque sensor for x/y/z axis with robot flange allows precisely controlled handling and quality assurance.
Today, single-arm robots are used for a wide variety of tasks. The ability to precisely measure forces and torques that occur directly on the arm opens up many more possibilities. In assembly processes, for example, the measured values can be used to draw inferences about the right parts, their positioning and correct placement. For this purpose, the specialists at burster have developed a six-axis force/torque sensor with a robot flange conforming to DIN ISO 9049-1, which simply attaches to the standard fixture on the robot arm (see fig. 1). The 8565 3D sensor with a diameter of 95 mm and height of 60 mm can measure up to three forces and torques Fx/Fy/Fz and Mx/My/Mz simultaneously (see fig. 2). The individual values are not extrapolated, as is often the case. Instead, each measured variable is recorded via a separate strain gage. The respective values can be read out via standard instrumentation amplifiers with a linearity error (20 % - 100 %) of 0.1 % of full scale. Here too, the measurement technology provider offers various solutions. Depending on the application, custom axis configurations are possible, from one to three axes and with or without torque measurement. So users only buy what they actually need. The measuring range is up to ±1 kN in Fx and Fy and ±2 kN in the Fz direction; the maximum torque in all directions is 50 Nm. The sensor’s special internal geometry ensures low crosstalk between the individual axes. Sensors for other measuring ranges are in the pipeline.
Enabling new ways of working
Depending on the sensor configuration, new areas of work can be opened up for the robots, or quality assurance measures can be implemented inline. For example, the relevant forces and torques can be measured when loading tool holders and compared with specified values. This enables good/bad assessments to be made, and prevents damage. For other tactile movement sequences too – such as gripping, milling, and grinding– the torques that arise also provide direct information about the condition of the workpiece or the tool used. Furthermore, adjustments by means of various reference measurements, e.g. of the friction between the workpiece and the tool depending on the contact pressure (Fx/Fy in relation to Fz) can improve the work result e.g. when polishing. Since a separate instrumentation amplifier is used for each channel, the individual values can be recorded and evaluated largely independently. Hence there is no need for a cost-intensive multi-channel amplifier with correction calculation to record the individual channels, which significantly simplifies the setup.
Picture captions:
Figure 1: Direct force measurement creates new possibilities for production, assembly and quality assurance. (Source: burster)
Figure 2: The scalable model 8565 3D sensor can output measured values for up to three forces and torques (Fx/Fy/Fz and Mx/My/Mz). (Source: burster)
Company box: About burster
burster supplies measuring technology ranging from individual sensors to system solutions. Its customers are mainly in mechanical and plant engineering, automation, the automotive industry and its suppliers, electrical and electronic engineering and the chemicals industry. The range includes measuring instruments and testers as well as standard sensors for mechanical and electrical measured values, such as load cells, pressure, torque and displacement sensors, milli- and megohmmeters, and resistance decade boxes. In addition, individual custom OEM solutions are possible, including for many other sectors and future markets such as medical engineering, biotechnology and e-mobility. Many years of experience in designing and building measuring instruments and sensors guarantee optimum solutions every time. Developed and manufactured in Germany, burster sensors, amplifiers and transmitter modules, precision instruments and measuring systems for sensor signal processing are shipped to customers all around the world.
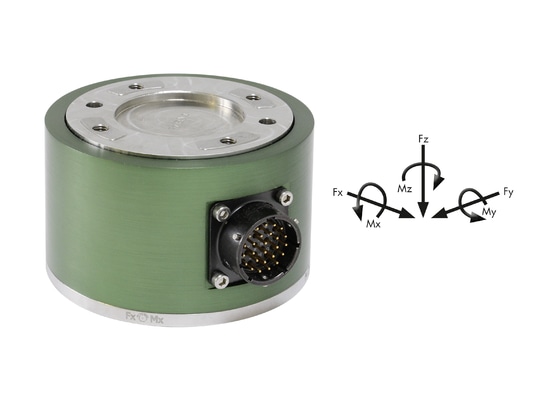