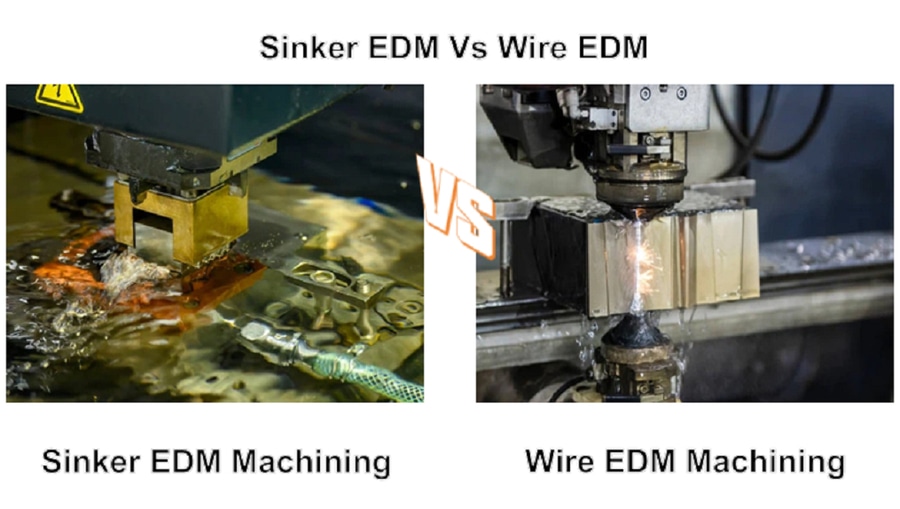
#Industry News
Sinker EDM Vs Wire EDM
Decoding The Machining Choices
Both Sinker EDM and Wire EDM fall under the broad umbrella of Electrical Discharge Machining[EDM]. While they share a common foundation in the utilization of electrical discharges to erode material and create precise shapes, their most significant difference lies in the shape of the electrode.
In Sinker EDM, a precisely shaped electrode, often crafted from materials like graphite or copper, is employed to meticulously machine the workpiece. In contrast, Wire EDM uses a thin wire as the electrode, typically composed of materials like brass or tungsten.
The Decision Between Sinker EDM And Wire EDM Is Multifaceted And Should Be Based On The Specific Requirements Of Your Project. Here Are Some Considerations To Guide Your Decision:
1.Material Type and Thickness: Wire EDM is better suited for thinner materials, while Sinker EDM excels with thicker materials.
2.Part Geometry: Wire EDM is ideal for complex shapes with stringent tolerances, whereas Sinker EDM is more suitable for deep cavities or intricate mold shapes.
3.Surface Finish: Wire EDM yields smoother surface finishes, while Sinker EDM produces coarser surface textures.
4.Production Output: Sinker EDM is typically slower than Wire EDM, making it a better choice for lower production volumes.
5.Project Progress: In the prototyping of new products, Wire EDM can swiftly cut certain sheet-like workpieces, eliminating the need for molds, tooling, and fixtures, thereby significantly shortening the product development cycle.
6.Cost: Wire EDM is generally more cost-effective than Sinker EDM, making it a financially prudent choice for specific applications.
For more detailed information or to ask related questions, please click the link in the lower right corner.