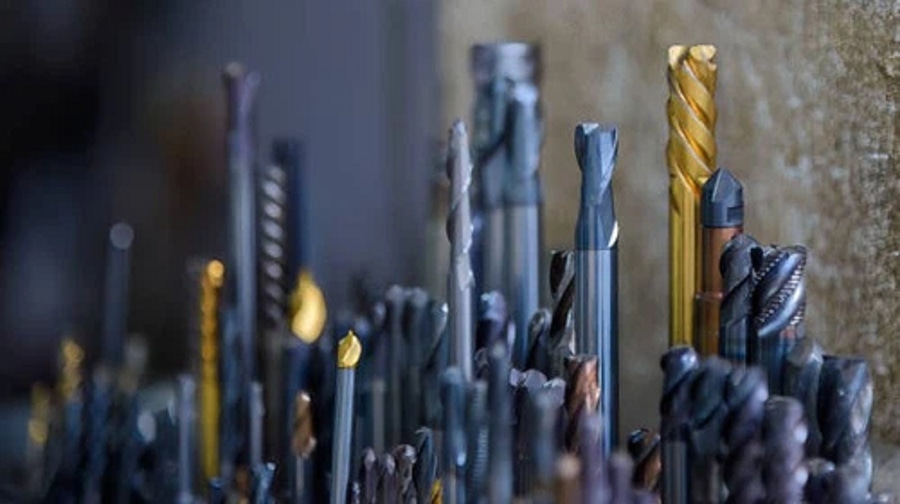
#Industry News
Types Of Milling Tools 101
Precision Crafting Essentials
A milling cutter is an essential tool in a milling machine or CNC center for material removal operations. These rotary cutting tools consist of one or more teeth, each of which intermittently removes a portion of the workpiece during the milling process.
Milling cutters are mainly composed of three key components: tool handle, tool body, and blade. These three parts work together to complete the milling operation.
The tool holder serves as the main support and is connected to the milling machine spindle.
The body is the main structural part of the handle, responsible for supporting and connecting the handle and the head.
The cutting edge is the part of the cutter body responsible for the actual cutting process, including the tip, main cutting edge and teeth.
The following are common types of specialized milling cutters:
End mills, also known as straight shank milling cutters, are the most widely used milling cutters on milling machines and are mainly used for small milling operations.
Ordinary milling cutter for machining flat surfaces on horizontal milling machines.
Three-edge milling cutters are standard machine tool cutting tools commonly used on horizontal milling machines, generally for milling grooves and steps.
Keyway milling cutters, also known as T-slot milling cutters, are very similar in appearance to ordinary milling cutters.
Saw blade cutters have elongated teeth that are suitable for cutting and removing medium-hard materials, especially in narrow and deep grooving applications.
Face milling cutters have relatively short cutting edges and are mainly used for machining flat surfaces. The cutting edge is always on its side and requires horizontal entry at a set depth.
Angle milling cutters efficiently create precise angles and grooves on a variety of workpieces.
The tool profile of a form milling cutter is made according to the intended final shape. These milling cutters may come in a variety of tip shapes, flute counts and tool materials to meet complex, curved or three-dimensional machining requirements.
Gear milling cutters use the profiling milling method to perform cutting motion along the contour of the gear to achieve precision machining.
Hollow milling cutters consist of a cylinder with cutting teeth on the outer surface. The center of the tool is hollow and can be mounted on a mandrel. It quickly creates a uniform pre-thread diameter, increasing productivity.
Thread milling is a precision thread processing method done on a three-axis machine tool (machining center).
Chamfer cutters are specifically designed to remove sharp edges during the cutting process, creating bevels or rounded corners rather than right angles.
For more information, please click on the link on the lower right. You can learn what a milling cutter is, the structure of a milling cutter, the types of milling cutters, how to choose a suitable milling cutter and the differences between them.